Developing a reputation as a solid and reliable source of technical solutions definitely means knowing what you are doing. Familiarity with procedure and using the tools you have (properly) is definitely a must! But spotting deficiencies in tooling or procedure as well as being willing to adapt and evolve is what it takes to keep your business moving forward in a positive direction. When faced with adversity, you can pack it in and head home, defeated, or you can step up to the challenge and overcome it. I chose the latter!
I was called to a body shop for a 2019 Honda HRV (Figure 1) that recently had the right passenger side mirror replaced. This mirror had a blind spot camera incorporated into it and needed the camera calibrated. This was an easy task for me because I had the proper target and knew the exact procedures needed to perform the task. I also noticed there was an icon on the dash relating to an error with the front LKAS camera system. I asked the shop if the front windshield was replaced or the camera was disturbed. The shop was honest enough to tell me that he hired someone else to come out to calibrate the blind spot side camera and the guy he hired was unable to perform the task. After the guy left, he noticed more errors on the dash, but did not think much of it.
Preliminary evaluation
I proceeded to scan the vehicle to see what it would take to resolve the current issues this vehicle had. It turns out that the prior guy was unaware that the blind spot side camera calibration was all performed by the center dash panel electronics. He used his scan tool and went into the menu for the camera system that controlled the Lane Keep Assist System. He started the procedure and found out (a little too late) that he was working on the wrong system. What he did not realize was that once you initiate the procedure to start, there is no backing out without leaving a message that now said, “Static Camera Aiming Incomplete.” The problems were now compounded, and two separate procedures had to be done on the same vehicle.
The blind spot side camera calibration went well, but the real challenge was the LKAS calibration, because this vehicle would require both a static calibration (using a frame machine with a target) and then followed by a dynamic calibration (drive on a three-lane highway). Most manufacturers will opt to do either calibration, but not both at the same time. Some manufacturers will require you to properly set up a camera statically (using a target) then allow the camera to fine-tune its calibration over the accumulative highway driving by the owner of the vehicle. Then other manufacturers do not require any targets, but need the vehicle to be driven on a three-lane highway, keeping in the center lane, while it reads the lane marking to self-calibrate using a scan tool.
Climbing out of the deep hole that was dug
The first step in the static procedure is to make sure you have a level floor and about 4 meters of open area ahead of the vehicle to place the frame. This vehicle will require you to measure out 3 meters (9 feet 10 inches) from the center of the left front wheel extended out to the front of the car (Line “A” in Figure 2). A centerline will need to be established, under the vehicle from the rear of the car extending out past the front of the vehicle. This can be done using a plumb bob hanging from the trunk and one from the hood, aligned with the car emblem that is usually centered on the vehicle. You will have to mark the floor in the rear and place a laser target on its mark, then place a five-line laser under the front plumb bob centering it over the laser assembly, and line the laser housing to strike the rear laser target (Figure 3).
Once this is done, you can place a four-line laser down the left side of the vehicle, placing it 3 meters forward from the center of the left wheel and intersecting with the 5-line laser at the front of the vehicle (Figure 4). This would be the spot that the frame machine will be centered on. The frame machine has its onboard four-line laser to properly square it up with the laser grids that are already on the floor. Once the frame machine is in place, it is equally important to use the base knobs to lock it in place and make sure it is perfectly level (Figure 5). Once the frame and target are in place, you need to set the proper height of the target, center from the floor. On this vehicle, the spec is 1100 millimeters (43.4 inches) and this is achieved with a crank handle on the frame assembly and the use of a laser measure attached to the frame. The last step before aiming the camera would be to input the measurements of the front wheel housing arcs distances to the floor. Suspension height is critical to achieving the proper aim of the camera, so it must be within an allowable spec and on this car, the measurements were about 722 millimeters (Figure 6).
Everything was now all set to go so I next commanded the system to learn the target and it proceeded without any issues. This particular vehicle needs to see the same target in three positions, so I then moved the target to the adjustable target mount on the left side frame arm and slid the target mount out to 700 millimeters from the center of the frame (Figure 7). After learning position #2, I repeated this procedure for the right side, and everything went smoothly without any problems of any kind. The final step was not to cycle the key but rather to proceed with a Dynamic Calibration on a nearby highway. I dismantled my frame set up and put all my equipment safely locked into my vehicle and secured my truck inside the shop’s building, where someone could keep a close eye on it while I was away for the calibration drive.
A swing and a miss
Luckily for me, this shop was not too far from a three-lane highway, because if it was, it would be hard for me to spend a lot of time to get to a highway of choice within the time frame I allow for each shop visit. The time of day is crucial, and you can’t have a lot of traffic on the roadway. You need to maintain at least a four-car distance (with a speed about 40-70 MPH) on a straight and flat road. This has to be carried out without stopping, while the camera is using the highway lane markings to perform the calibration. You also need to make sure the weather conditions are correct and not have rain, snow or darkness on the roadway or the calibration process will not succeed. I drove this vehicle for almost a half hour in one direction, turned around and drove another half hour and the camera system would not learn the roadway. I returned to the shop to tell the shop owner that there was something wrong with the vehicle or the process, and I had no answers for him. The windshield and camera were never touched, but I was unable to finish the job. The shop owner was under pressure with the owner of the car and the insurance company, so I lost the job to the dealer who tried calibrating the camera. In the meantime, I was only paid for the Blind Spot camera system I calibrated.
I walked away puzzled because I have been successful in calibrating windshield cameras for other manufacturers. This one beat me for now, but I was ready for the next one and hopefully the next shop would be patient and willing to work with me. That day came soon enough, and I was served another Honda SUV with the same target and equipment set up. The static calibration went very well, but the dynamic calibration would be the challenge. I was ready for anything this car would serve me. Well, after another hour of wasted time, another failure hit me that sent me into a denial mode. I had to reach out to a friend of mine who was an “A” tech at a local Honda dealership to see if he could unravel my problem. He invited me over to the dealership to show me their setup.
When I arrived at the shop and showed him the target I was using, he chuckled and said, “You’re using that?” I compared the target he was using with my target, side by side and discovered that his target was about 42 percent larger than my target! The diameter of his target was 12 inches compared to the one I was using, which was 7 inches (Figure 8). If you look at the Honda set up, you can see that they use three identical targets at the same time, and they are all preset on the frame, equidistant about 1200 millimeters from the center to center of each target (Figure 9). My frame was set up to place the targets 700 millimeters apart at a 42 percent reduction of spacing. My frame machine could only measure out to 800 millimeters max. I was very confused when he even told me that the distance from the target to the center of the left wheel was 6 meters (19 feet 8 inches) and not 3 meters (9 feet 10 inches). At this point, I was suddenly having a “Honey, I shrunk the frame” moment.
The frame I was using was reduced to accommodate mobile service, but I am guessing the company had to accommodate a fix to do this procedure on certain Hondas. When I started to reach out to the company, they were aware of the problem, but did not have a newer/larger target available yet. So, I needed to spring into action. I reached out to a Honda tool supplier and they had the target kit for a price of $350, but it would take a week to get. Well, guess what? I lost this job also because the wait time was too long for this shop, and they had to get the job out sooner. A lot of these shops are on cycle time and are pressed by the insurance companies to get the cars out ASAP, and I fully understand their position.
A shot at redemption
So, my part finally arrived, and I removed the mounting plate from the back of my original target. I glued it to the rear of the Honda target so that my frame could accommodate the mounting of this target and be ready for my third attempt (Figure 10). I was anxious for my next chance and sure enough, it came within a week. I followed all the Honda specs on this third vehicle, but wasn’t able to lower my frame to 950 millimeters (because the frame was only able to reach a low point of 1007 millimeters), but I was hoping all my other measurements would meet the criteria to teach the camera statically. This would allow it to be trained properly and look down the road with no issues. The only drawback with my altered set up was having to set the frame up in three equidistant positions of 1200 millimeters (the frame arms were too short), but it was all I had to work with. I finally finished my static calibration, packed all my stuff away and went for a dynamic calibration down the highway. Then the most incredible thing happened!! The dynamic calibration was done in 10 minutes. I could not believe how fast the procedure went, once I did the correct factory static procedure.
I can tell you that I lost many hours on these three Hondas (and lost my credibility with the first two shops), but in the end, I won the war. You fight these issues in small battles, keep moving forward and do not give up. You need to suffer losses in your business on that never-ending learning curve to be successful. You can also provide valuable input to companies that build factory (or aftermarket equipment) to let them be aware of glitches in their systems. It is up to us, as a working force, to help these companies by testing their products in the field. As I am writing this article the company whose frame I am using has already addressed the problem with a new target and new updated procedures. Many companies will go as far as to Beta test their equipment and software daily. That also becomes a valuable asset to our industry so we as technicians are not plagued by issues that make us scratch our heads and put us into denial mode. My only hope is that this article has enhanced what you know or did not know.
About the Author
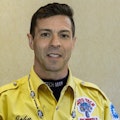
John Anello
Owner and operator of Auto Tech on Wheels
John Anello is the owner and operator of Auto Tech on Wheels, established in 1991 in northern New Jersey. He provides technical assistance and remote reprogramming with 21 factory PC-based scan tools. Driven by a passion for cars, John's business now services roughly 1,700 shops.