Bryant: Finding Balance in an Unpredictable Work Environment
In any industry, there are always going to be variables that are out of our control. As business owners, it's our job to find ways to manage those variables in order to maintain a sense of stability and balance within our companies.
In the collision repair industry, we deal with a lot of unpredictability. Parts availability, insurance claims, and the volume of work can all fluctuate on a day-to-day basis. This can make it difficult to maintain a consistent workflow and ensure that our technicians and administration are productive.
However, there are some things we can do to help find balance in an unpredictable work environment. By being proactive and flexible to an alternative approach, we can adapt to whatever changes come our way and keep our businesses running smoothly.
Time blocking gives your team the ability to be proactive.
Time blocking is an underutilized approach to organizing one’s day-to-day life. Not only does it allow you to experience a predictable balance between work, life, and leisure, but it also is an effective means of avoiding the tendency to be constantly “on-demand,” reducing the accompanying sense of pressure. Done correctly, time blocking can help manage stress levels throughout your operation more efficiently by allowing team members to distinguish between what should be taken care of now and what can wait a while longer. Although it takes consistent effort to implement and maintain, this valuable tool provides an opportunity for proactive management rather than the reactive response in everyday activities—giving one enough space and focus to be at their most productive best.
How does time blocking apply to collision repair?
Time blocking is an incredibly efficient way to manage the workload of a collision repair business. Nobody is on demand, as customers are encouraged to drop off their vehicles for appointments or consultations at a convenient predetermined time. All phone calls made with customers or adjusters for repair estimates and updates are scheduled events so that nobody’s time is overextended, or unnecessary/redundant conversations may be had. In addition, time blocking makes sure that busy employees have enough time in between commitments rather than rushing from one task into another. Although challenging to perfect, once established and executed properly, it will allow your team to accomplish far more with their time and energy. As such, when implemented successfully, it makes a huge difference in helping the overall productivity of any collision repair shop.
Avoid being on demand
We all are experiencing the impact of insurance companies recently reducing field positions one way or another, negatively impacting our cycle times and throughput. As your walk-in estimate requests increase daily, call volumes are also up higher than usual, but now we are forced in many cases to manage it with limited office personnel. During the repair process, customers expect advocacy, which can be difficult for us to provide, given the current circumstances. Being dependent on everyone else's schedule simply isn't something that we have the luxury of doing anymore. In order to manage our shops today, we must ensure that nobody within our operation is on demand. Everything is scheduled and scheduled around existing obligations or previously made commitments.
How to schedule your team’s day to maximize productivity
For best results in team productivity, it is important to establish an organized schedule at the start of the day. To achieve this, everyone should have a defined role, and commitments should only be made based on the amount of time each individual has while considering any previously scheduled events. All necessary meetings should be planned accordingly, with everyone's availability taken into account, while avoiding random interruptions that can pull team members off of their tasks and cause increased transitional waste, thus negatively impacting your facility's performance. Ultimately everyone should work together to ensure everyone's time is respected and that they stick to the schedule. For example, an incoming call to a team member is always answered with, "That team member is currently helping another client. Would you like me to send you a link to their availability for you to schedule a call with them that works for your schedule & theirs?"
Tips for implementing solid scheduling
Solid scheduling entails setting appointment times and dates manageable for clients and your organization. To ensure maximum efficiency throughout, look into automation software solutions, as there is a considerable array of service providers offering minimal-cost applications that will duly recognize any previously-made commitments. Develop and maintain a regular meeting schedule to increase communications & accountability in scheduling all events and calls (walk-ins, vendor visits, etc.). Leverage the automation for appointment reminders to avoid clients showing up late or team members missing a scheduled call. These notifications can also help facilitate necessary information before calls or consultations to avoid rescheduling or being unprepared for a scheduled commitment. One of the biggest impacts you will experience during implementation is your newfound ability to regulate the number of cars entering and exiting the facility for a far more predictable workflow.
- Are you guilty of coming home only to ask yourself, "What did I actually accomplish today?"
- Is your workflow dependent on whatever rolls through your front door that week?
- Is the day-to-day calls & client pressure leading to improper prioritization of your team?
- Would you consider your overall operation proactive or reactive?
These are all common challenges that we all have faced as shop owners at one point or another, but there is a way to change the paradigm. Having pursued this method myself, I can attest to its benefits firsthand. It will help you better understand what’s happening in your business daily and allow you and your team to proactively approach each day with set goals and priorities. When you take the time to schedule your team's day, you can maximize productivity and effectively avoid any unnecessary downtime. While implementing solid scheduling practices may seem daunting at first, the benefits of automation and increased productivity will quickly become apparent. I challenge you to give it a try—your business (and your team) will thank you for it!
About the Author
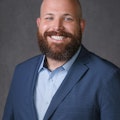
Drew Bryant
Drew Bryant has been the owner of DB Orlando Collision since August 2011. A 20 group leader, in-demand conference speaker, and award-winning shop owner, Bryant takes a nontraditional approach to process implementation, lean process development, and overall operational experience while remaining dedicated to his staff's personal and professional development.