“’I believe I can repair anything’ is no longer the case. Technicians need to be courageous enough to say I need training in order to repair this vehicle properly..”
This is a quote from an industry colleague and applies not only to training, but also to actively researching OEM information, to ensure that all collision repair technicians are following the vehicle-maker recommendations for repair. Today’s vehicles are vastly different than those of just a few years ago. The use of new steels, aluminum, carbon fiber, and other materials require new repair methods and new tools and techniques for joining to achieve complete, safe, quality repairs.
As the use of different materials continues to grow, the collision repair industry will be faced with new challenges; not only for repairability, but also for the joining technologies that will be required to replace parts on these vehicles. The vehicle makers continue to evolve their attachment methods, but many of the technologies they use today and will be using in the future cannot be duplicated during the collision repair process. Laser welds, friction stir welds, spot welding of aluminum and dissimilar metals are all techniques that are impossible today for repairers. These technologies will likely not make it to the collision repair industry anytime soon; perhaps never. This will require repair professionals to rely on OEM information more than ever.
Get Free OEM Training
Now is your chance to register for an expo pass to NACE Automechanika Chicago, where you'll have a chance to walk the show floor and take part in free OEM trainings.
GMA (MIG) Welding
While GMA (MIG) welding had been the preferred welding method for the past 30 years, we’ve seen a significant change in recent years and expect we’ll see a decline in the number of vehicles that require GMA (MIG) welding for part replacement. We will also expect to continue to see an increase in the number of vehicle makers that warn against using this process for repairs on vehicles that employ a high level of high- and ultra-high-strength steels (HSS and UHSS). This is due to the heat-effect that GMA (MIG) welding produces on HSS and UHSS. GMA (MIG) welding heat damages the areas adjacent to the weld and can potentially produce an inferior repair. It’s imperative to follow the vehicle makers’ recommendations for when GMA (MIG) welding is acceptable.
In addition to determining if the vehicle maker has specifications for the welding equipment, it also important to identify the type of electrode wire the vehicle makers recommend. While conventional ER70S-6 remains the preferred electrode wire for many vehicle makers that allow GMA (MIG) welding, there are a handful of recommendations for ER70S-3 from some vehicle makers. With regard to Honda GMA (MIG) welding, where allowed, they have an additional consideration. For steels up to 440 MPa, Honda allows conventional ER70S-6. For steels above that, up to 990 MPa, Honda had previously required an electrode wire from Bosch: DS980J. That wire has now been replaced with new electrode wire, available from https://www.techniciantools.net/ part number HWW-98008. Honda also requires an 80/20 mix of Ar/CO2 (C20), not conventional 75/25 (C25) shielding gas. More information on Honda’s welding requirements can be found at the I-CAR Repairability Technical Support (RTS) Portal (i-car.com/rts); note login information is required.
Squeeze-Type Resistance Spot Welding
Squeeze-Type Resistance Spot Welding (STRSW) has become the welding method of choice for many of today’s steel vehicles, especially those with a significant use of HSS and UHSS. While each OEM may have welder specifications for spot welding equipment, STRSW is accepted, and more often than not preferred, for collision repairs on late-model vehicles. Additionally, some OEMs require STRSW for certain applications and warn explicitly against GMA (MIG) welding. Repairability guidelines from Ford Motor Company, General Motors, Fiat Chrysler and others outline which welding methods are acceptable and should always be adhered to. As mentioned earlier, Honda also has published welding guidelines that are available to the collision repair inter-industry. Deviating from the vehicle maker recommendations may produce an inferior repair and may open the door for a potentially litigious situation.
MIG Brazing
MIG brazing has started to gain popularity in recent years amongst some OEMs and this momentum will continue to build over the next several years. MIG brazing is different from the oxy-acetylene brazing you may have learned years ago. While the principles of capillary action are similar, MIG brazing is done with much less heat. This limits the heat-affect on HSS and UHSS and leaves more of the corrosion resistant coatings intact.
Honda has been the biggest proponent of MIG brazing, beginning with the launch of the 2013 Accord and its 1,500 MPa A- and B-pillar reinforcements. The use of 1,500 MPa steels in Honda and Acura vehicles continues to grow and is now being leveraged for the rear rails on the 2016 Civic sedan. Honda requires MIG brazing for any 1,500 MPa steel that cannot be spot welded. There are several locations on each of the models that leverage this type of steel. If you repair late-model Honda and Acura vehicles, you must have equipment capable of MIG brazing in the pulse-synergic transfer mode. More information on HSS/UHSS repairs to Honda vehicles can found in the Honda & Acura High-Strength Steel Repair (HON11e) course, offered through I-CAR at i-car.com.
Other vehicle makers that allow, or recommend, MIG brazing for repairs include GM, Ford, Jaguar, and Land Rover.
If you are unfamiliar with MIG brazing, I-CAR now offers two courses on this subject. MIG Brazing Theory (BRZ01e) is a one (1) credit hour online course that covers the MIG brazing process, equipment options, techniques, and other pertinent information. The new I-CAR MIG Brazing Hands-On Skills Development (BRZ02) offering is an in-shop, instructor-led training program designed to teach technicians how to set up MIG brazing equipment and make common MIG brazing welds, including slot welds, open butt joints, and Honda’s double plug on lap welds. The instructor and student(s) work with the repair facility’s equipment to ensure the best possible learning environment. The course is a great primer for students enrolled in Jaguar/Land Rover’s (JLR) network. JLR students, as part of JLR’s Global Learner’s Journey, are required to successfully pass a challenging hands-on welding assessment that includes numerous MIG brazing joints.
Adhesive Bonding
When adhesive bonding first became popular for collision repairs, it was limited primarily to exterior panels such as door skins, roofs, and quarter panels. Since then, much has changed and adhesives are becoming a requirement for many different repair procedures, usually in conjunction with welds (weld-bonding) or rivets (rivet-bonding).
Adhesive bonding technology has evolved over the past ten years and is a common replacement requirement for a lot of unitized structure parts, as well as exterior panels, when used in conjunction with welds or rivets. Similar to all other attachment methods, the only way to determine if adhesives are required, and which type of adhesive, is to refer to the vehicle maker part replacement procedures. This has become even more critical with the arrival of some of the newer structural adhesives. These adhesives are different than panel replacement adhesives should be used where specified by the vehicle maker.
Adhesives offer benefits, in addition to provide a strong bond between panels. Adhesives are often used to provide improved noise, vibration, and harshness (NVH) prevention and offer a way to improve corrosion protection from panels that may otherwise be corrosion hotspots when factory e-coat and other coatings are removed. Adhesives also offer protection when joining dissimilar materials, such as aluminum and steel. This aids in the prevention of galvanic corrosion that can occur between dissimilar metals when exposed to moisture and air.
Rivets
Rivets have been used for several years on aluminum-intensive vehicles from Jaguar/Land Rover and Audi, but have gained significant popularity with the launch of America’s most popular vehicle, the Ford F-150. Although welding is an option for some panel replacement procedures, rivets are the most common attachment method on the F-150.
There are a variety of rivet types that collision repairers will encounter from the vehicle maker and during the repair process. It’s important to note that often the replacement rivet will be different from the vehicle maker installed rivet. It’s important to not only identify which rivet is used by the vehicle maker (this will help determine the best removal process), but it’s important to know which rivet(s) are required for part replacement procedures.
The most popular vehicle maker installed rivets are self-piercing rivets (SPRs). SPRs allow the vehicle maker to leverage rivets, without the requirement of pre-drilled holes. SPRs do exactly as their name implies; they self pierce the panels, creating their own bucktail when the SPR meets the die on the SPR gun. For repairs, SPRs are replaced with a new SPR (adjacent to the original SPR hole), blind rivets, or welds. To determine if an SPR is allowed for replacement, refer to the vehicle maker repair procedures. This will also help identify the diameter and length of the SPR. When removing and installing SPRs, it’s imperative that the technician uses the correct SPR to match the material and length of the rivet. If the SPR is slightly too long or too short for the application, the joint can fail. Using the correct dies is also very important. Incorrect dies can cause damage to the panels, rivets, and rivet gun dies; and replacement of dies on a regular basis will quickly become a costly venture. SPRs require access to both sides of the panel for installation.
Blind rivets are often used when replacing panels that were installed with SPRs from the vehicle maker. When SPRs are removed, holes are left in the panels. Blind rivets allow for installation of replacement panels using the hole that remains on the vehicle. Similar to SPRs, it’s important to install the correct diameter and length blind rivet. Blind rivets are also installed by the vehicle maker and may be replaced with a blind rivet or sometimes by an aluminum weld. Blind rivets only require access to one side of the panel.
Solid rivets are another type of rivet that may be recommended by the vehicle maker. Ford, for example, has a number of locations on the F-150 that solid rivets can be used. Similar to blind rivets, a hole is required for installation of solid rivet, but also requires access to the panel backside to allow for the use of a bucking bar to create the solid rivet bucktail.
If you’ve recently purchased a self-piercing rivet gun and are looking for expert training on its proper use, I-CAR now offers a Rivet Bonding Hands-On Skills Development (RVT01) course. Similar to the MIG brazing course, this course is delivered in-shop, with the repair facility’s equipment.
Other Mechanical Fasteners
There are a couple of other mechanical fasteners that collision repair professionals may encounter on today’s late model vehicles. Flow drill screws (FDS), such as EJOTs, may be used for some vehicle maker attachment methods when only one-sided access is available. FDS are similar in appearance to a sheet-metal screw and during vehicle manufacturing are rotated at a high rate of speed until the base material begins to soften. The FDS then pierces the material, creating its own threads to attach to. When the material cools and solidifies, a secure joint is created. Some vehicle makers allow FDSs to be reused, if the threads aren’t damaged. If the threads are damaged, FDSs are replaced with rivets. Some vehicle makers have oversized FDSs that can be used when the original threads are stripped.
Clinches are primarily used by the vehicle maker and don’t often require any type of replacement procedure, other than on some door skins in the belt-line molding area. If clinches require replacement they are replaced with rivets.
Aluminum MIG Welding
Aluminum MIG welding is allowed for a number of different repairs and technicians should be familiar with the equipment requirements and differences in techniques between steel and aluminum welding. It’s also important to be familiar with aluminum MIG welding for repair facilities considering getting involved with some of the OEM aluminum repair networks, such as JLR, Audi, Tesla, Mercedes-Benz, and Ford. I-CAR offers an Aluminum Welding Training and Certification (WCA03) program to teach technicians how to set up their equipment and how to make some of the welds they may encounter when repairing aluminum vehicles. The course is also a great way to prepare technicians in advance of attending a multi-day OEM welding assessment, including the ISO 9606-2 certification.
Future Joining Technologies
There are some additional joining techniques that have started to appear. Many in the collision industry have questioned what, if any effect, these new methods will have on the repair process. Processes such as friction stir welding, aluminum spot welding, and steel-to-aluminum spot welding are a few that have been noted recently. Fortunately, for collision repair professionals, these vehicle maker attachment methods will have minimal impact on the repair process. If there are replacement procedures available for parts installed with these techniques, they will likely include one, or more, of the aforementioned collision repair attachment methods.
Conclusion
As vehicles continue to evolve and vehicle makers expand the use of HSS, UHSS, aluminum and mixed materials, the attachment methods used will continue to evolve. A few key takeaways to consider:
- Conventional steel GMA (MIG) welding will continue to decrease for part attachment; however, we’ll continue to see it leveraged for sectioning and welding in areas where there is no backside access for spot welding.
- STRSW will continue to grow as the preferred attachment methods for steel-intensive vehicles.
- MIG brazing will be increasingly popular for vehicles that are primarily steel structured vehicles in areas where spot welding arms cannot access the welds zone.
- Adhesives, in conjunction with other attachment methods, will grow in popularity for both vehicle manufacturing and collision repairs.
- Rivets and flow drill screws will continue to grow in use for not only aluminum-intensive vehicles, but also many steel applications, and for vehicles that use a mixed-material architecture.
Today’s and tomorrow’s vehicles are different than the vehicles we’ve been repairing in the past and each new model year will present the industry with new challenges. The only way to ensure complete, safe and quality repairs is through adoption of new tools and equipment, training, and access to vehicle maker technical information.
About the Author
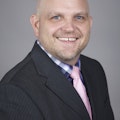
Jason Bartanen
Director - Industry Technical Relations, I-CAR
As Director, Industry Technical Relations at I-CAR, Jason Bartanen is leading I-CAR's Repairability Technical Support (RTS) Initiative. Prior to I-CAR, Bartanen worked part-time as a collision repair technician while pursuing his BQA in communications from the University of Wisconsin-Green Bay. Bartanen is a member of the collision repair and refinish advisory committees at Fox Valley Technical College (FVTC) and Northeast Wisconsin Technical College (NWTC). Bartanen is also a member of the SkillsUSA National Collision Repair Technology committee and is the segment leader for the collision repair, welding segment.