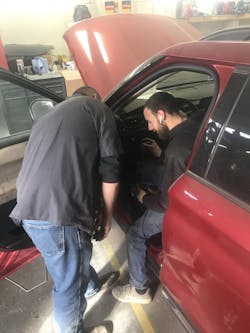
There's an adage that says, “No one likes to hear the word ‘no.’” There may be some truth to that in certain contexts. I want you to hear the word "know” loud and clear from this point forward. It will be referenced for what you already know and what you need to know!
I'm going to share at a high level and outline the basic path one needs to take to train a new technician. It's not all-encompassing, as I have a limited space to convey this theory. Let's be honest with ourselves and recognize that training a technician is not a path set in stone, and it isn’t straight or short, for that matter. You may have been thinking that this article would be solely focused on a person that is coming into our industry for the first time. You would only be partially correct. It's as important to focus on the facility and current staff before beginning any sort of training program. If you don't currently have such a program or are not entirely satisfied with the results you have been getting, this is the place you need to be at the moment.
There is an additional benefit to training new employees regardless of the role. It should be realized that all existing employees gain benefits from improvements to the system as well. What I will offer is a glimpse into a fresh thought process intertwined with some of the tried-and-true methods of days past. You see, we don't need to reinvent the wheel here, but we do need to add some new concepts and improve the old ones.
Before we get into the heart of the matter, I need to cover the following topic. As you know, our industry, as well as most other trades, is struggling to entice new people into the workforce. Before entertaining the thought of training a new technician, I would ask that you become part of the solution to that problem rather than endure it. Consider being active in your local I-CAR Committee. Join your local/state associations if available. Look into joining CIC (Collision Industry Conference), SCRS (Society of Collision Repair Specialist), NABC (National Auto Body Council), CREF (Collision Repair Education Foundation), ASA (Automotive Service Association), or any other related organization that fits your ability to contribute. Another active role could be taken in SkillsUSA. SkillsUSA is an organization that is a collaboration of the industry, teachers, and students working together. They serve middle school, high school, and college/post-secondary students. I'll relay their Mission Statement:
SkillsUSA empowers its members to become world-class workers, leaders and responsible American citizens. We improve the quality of our nation’s future skilled workforce through the development of SkillsUSA Framework skills that include personal, workplace and technical skills grounded in academics. Our vision is to produce the most highly skilled workforce in the world, providing every member the opportunity for career success.
These and similar organizations may very well have resources that can be of help when training a new technician as well. They will most likely enhance your business in several areas if used wisely!
We are finally getting to the word “know” now. It's going to be referenced a lot. There is a lot to know when training a technician and a clear path will help you succeed. That path starts before you even begin the hiring process, as noted earlier. I'm going to write this as more of an outline, but let me remind you that this is a high-level overview. There are a lot of ways to add detail to each section. I'll be asking many questions. Answer them honestly, and you should begin to see areas in need of improvement or a completely new spin on the process. It should also highlight what has worked in the past and what is worthy of continuing. I'll break down the categories with a brief description of each.
Know what you want
There should be a short- and long-term plan in place. It may be that you are replacing a technician due to retirement or they have decided to work elsewhere. Those two scenarios would fall under the short-term plan. It would be a replacement scenario versus a growth in the number of technicians employed. The long-term plan could be a vision of how many technicians you expect to employ in the future. Even if there are no immediate growth plans, it is going to be beneficial to have a training plan in place for any unforeseen events. You must also have an idea of what the outcome is and what success would be measured by. An easy target would be to train a new employee from ground zero and that technician would be a productive and valuable member of the team until they retire. Yes, that can happen, and it does happen. I'm not going to say it often does, but you can set that as a goal.
Long-term goals are different, but the training methods should be the same for both. What are the shop’s plans for 10, 20, or 30 years? Plans don't have to be set in stone, but they should be serious and realistic. The worst plan is not having one. Are there plans for location additions? There should be a training plan/system in place if it's one shop, hundreds of shops, or anywhere in between that you manage/own. It is far better to have a system in place and not design on “on the fly.” Plans can be improved or changed as needed of course. Changes should be small improvements, not large corrections.
Another aspect to consider is incorporating a cross-function component. During initial and recurrent training, consider expanding a technician's capabilities for use in a different role. Is there a technician that could fill in on the administrative/ estimating/blueprinting side during a vacation or illness? Ask yourself if those currently employed could function in a different role if expansion was on the horizon.
Know what you have
What is your shop's physical size? Is there enough room to add more technicians without encroaching on existing staff? Do you have current technicians that are willing and able to train? Do you have staff that are willing to mentor a person just starting in the business? If you have a mentor candidate, it is important to have a plan in place so that the production of the mentor is addressed. Compensation protection will be a factor as well. I've trained technicians in the past while working within a flat rate pay plan. The time I spent with the apprentice affected the hours I would normally produce. The same would be true for a salary-based pay plan, or even hourly for that matter. In any scenario mentioned, the production of the seasoned technician will likely be affected. As a shop owner, manager, or production-related person do you have the time available to spend with a new employee?
Is there a dedicated space in the shop that is conducive to being able to deliver online training? This question can also affect existing employees. If there is a dedicated space/office for training it will be easier to manage everything that needs to be done. I've oftentimes seen an area of a breakroom equipped with a desk and computer station for such needs. Is there an office space or other area in the shop that's not being utilized and could function for training needs? Initial and ongoing training would both be served if there is. It's also a way to send a clear signal of your willingness to be up to date.
Know how to get there
There are several ways you can begin to train a new employee. A lot of that is going to be based on what they know. Did they come from a post-secondary school? Did they attend a High School program? Do they know anything related to our field? You get the picture here. Be ready to either assess what they know or begin a ground-up training program in conjunction with I-CAR from day one. A mentor in your shop will be able to ascertain what level they are in in a short period. Maybe you can do a 90-day partnership with a seasoned technician and develop a path based on those results. Never underestimate the knowledge you and your current staff possess. When I was beginning my career many years ago there was no internet, so everything I learned came from my High School vocational instructor, textbooks, and the techs I worked with. I learned the most by watching and being guided by the techs at the shops I worked in. That is still a common way one learns anything — by watching and doing. Learning from mistakes is often cited, and I was no different, but I don't think enough comments are made about learning from not making mistakes. Every time someone accomplishes a task, no matter what it is, for the first time there is knowledge gained at that moment. The short version is this: we learn from making mistakes AND from not making them! Is the culture in your shop positive towards growth and learning? It should be, and that can make training a new technician a lot smoother.
Know who can help
My article published in the March 2020 issue of ABRN asked that you think “inside the box” when it comes to technicians. That still holds true when focusing on technicians, but thinking outside the box will help when developing a training strategy. I-CAR has the initial and recurrent training our industry relies on, but make sure you are using all the available resources that you can. Ask for help! Your paint supplier, jobber, or equipment representatives may have programs in place that are available for your use. Those programs may very well be compliant with the I-CAR Industry Training Alliance program. Several equipment, product, and vehicle manufacturers’ training may very well satisfy some requirements put forth by I-CAR. An example would be that if training is taken from Polyvance, relating to plastic repair, that training may satisfy an annual requirement in an I-CAR knowledge area. Be sure to inform your Customer Care representative of any training you have completed outside of I-CAR, and they may be able to apply it to your records if it meets the requirements and they are a Sustaining Partner.
If there is an opportunity for a material/product representative to come in and do a “lunch & learn,” take advantage of that opportunity. Your seasoned techs should welcome the refresher (there will be some grumbling and/or jokes made, but rest assured a good technician will welcome the knowledge). Make sure your training encompasses OSHA requirements and the EPA HAPS 6h Rule as well as respiratory fit training, as they are among several different but related topics that should be addressed regularly.
Regardless of if you are currently training a new technician or not, as always, safety should take a front seat when considering training. Federal, state, and local criteria should be kept current as well. Hazardous waste considerations should be near the top of the list. Initial training needs to start in this area. This is another example of where training a new technician can benefit the whole shop by remaining compliant.
Know when you see it
As I've stated in the past, become involved in the training. Your interest and involvement make the whole process meaningful. The whole shop stands to benefit regardless of the role of the trainee. Find ways to reward the training and milestones throughout the development or recurrent process. Make sure the training received is understood and watch for performance improvements. Implement the training. That sounds basic, but it is oftentimes a downfall of a shop not to act on the knowledge gained. Have you utilized an assessment program throughout the training? Attempt to make a loose schedule of achievements. It may be initially based on experience but keeping track of the progress of a new trainee may very well become a guide for future endeavors. Most folks learn at different paces, so stringent timelines may not apply. What will apply is your involvement in the progression. It will benefit all involved.
Know how to keep it
Maintaining an atmosphere that is conducive to longevity is one that trains on a path and keeps recurrent training in play. Investing in equipment, technology, and training benefit the shop as a whole. Realize the benefits of training. Compare statistics you track to make sure the training is having a positive effect. It may show in increased customer satisfaction, fewer adjustments to scheduled deliveries, or other improvements. The benefits may not show instantaneously, of course; it may take months or even a year to see results. It may be just a culture improvement. Not everything equates to improved profits and that's OK. A smoother running, happier shop should be reward enough for most. Reward performance improvements. That can take the form of monetary compensation or other forms. Either way, if you acknowledge it, the recipients of that gratitude should appreciate those gestures.
As I stated from the beginning, there is a lot more material to cover than we have space for here. I hope I have conveyed the importance of a framework around training that is necessary. Preparation is the key here. We are well versed in adaptation in this industry and this subject is no different. Just be careful not to make too many or sweeping changes mid-course. Training does cost and it is a real expense — make no mistake about it. The question is what is it going to cost you if you don't? I'm confident that if you implement these techniques and tips presented you will be successful in training your new technicians. I KNOW you will!
About the Author
Dave Brinkley
Dave Brinkley works for I-CAR as an in-shop knowledge assessor and instructor. He has worked in the collision repair industry for more than 35 years, working as a technician, manager and insurance appraiser. He's the founder of CR Tools LLC, a development and consulting company for collision repair tools. Connect with Dave on LinkedIN or Facebook.