It is not uncommon for a vehicle recently involved in an accident to be towed or driven to your shop to have prior underlying issues. There are vehicles out there that accumulate different problems over time and then manifest into a cluster of issues. Then comes a day when that vehicle is involved in an accident and delivered to your front door with the “Ever Since the Accident” syndrome. The vehicle will have to be assessed of the damage incurred and any underlying problems you discover at the time. Some vehicle owners may not necessarily come clean to what issues the vehicle had prior to the accident, so it becomes your task to see what problems are really related to the insurance claim. It is hard enough to be a body shop tech, but now you need to take on another job as an automotive CSI expert. Your job now involves unraveling the events of the accident and trying to decide what issues are really going to be covered by the insurance company even if it involves thoroughly interviewing the owner of the vehicle.
This was the case when I was called to a shop for a complaint on a 2018 Toyota Camry that was involved in a front-end collision. The vehicle suffered minor damage to the front end, and the shop made repairs to put the vehicle back to its original condition. During the shop’s post-repair procedural check, they had noticed that there was a fault on the dash that directed them to an issue with the Blind Spot Detection system. The vehicle was hit in the front, and the driver door mirror was removed and replaced as part of the repair process. The indicator light for the Blind Spot Detection was located within the mirror lens, but there were no issues with its operation. It was hard to believe that the accident was responsible for the fault, because the main functions of the Blind Spot Detection system were located in the rear sides of the vehicle.
When the customer was contacted about the issue, they claimed that they were not positive if the error message was on the dash prior to the accident. The customer felt that the issue was caused from the accident and that their car was in fine working order. At this point it now becomes the responsibility of the shop or the insurance company to resolve the issue as part of the claim, because nobody can prove the problem was not preexisting—because of course the customer is never wrong and in business we must respect their account of what issues their vehicle now presents. The Blind Spot Detection system is part of the ADAS safety components, and it is a critical liability issue that must be addressed prior to releasing the car back to the owner. The shop took the initiative upon themselves to go forward in addressing the issues with the hopes that the insurance company would pay if it were related to the accident in any way at all.
When I arrived at the shop, I scanned the vehicle and retrieved a Code C1AC1 with the definition “Master Module Horizontal Axis Misalignment” (Figure 1). This was an indication that there was an alignment issue with the right rear blind spot module assembly. On this vehicle the “Master” module is located on the passenger rear of the vehicle and the “Slave “module is located on the driver rear of the vehicle. This may not always be true on other manufacturers because they could favor either side to place the Master module, but a dead giveaway would be to check the number of wires going to the module. The one with the extra two CAN wires would be the Master module on vehicles where only the Master module is available on the vehicle network; thus, the Slave module would have an isolated CAN network to the Master module.
There was a chance that the battery could have gone down low enough to cause the loss of calibration with the Master Blind Spot module, so I went ahead to set up my equipment to calibrate the Blind Spot System. The shop I was serving had an exceptionally large working area that was about 35x65. The shop floor was perfectly level and recently resurfaced because the building was just renovated prior to the shop making it its new home. The average width of a vehicle is about six feet, and most Blind Spot calibrations that require both sides to be performed at the same time would require at least a minimum of 30 feet across the back of the car with nothing in the radar’s path except for a wall. I was only doing the passenger side blind spot, so I opted to place the driver side of the vehicle near the wall to give the radar unit plenty of room behind the target so it would not skew its target’s location.
I needed to first plumb the front of the vehicle to find the center, referencing off the front emblem and marking the floor (Figure 2). The next step was to also plumb the rear of the vehicle using the rear emblem and mark the floor (Figure 3). This would set up my two center points of the vehicle so I could set up a centerline under the vehicle and out towards the back of the vehicle with use of a green 4-line laser at the rear of the vehicle and a laser target placed at the front marked point on the shop floor (Figure 4). Once the laser was in place, I had to finalize my placement of the target using the specs addressed in my ADAS software (Figure 5). This required me to place a horizontal line at 1686 mm / 66.41 inches away from the back of the vehicle; this would be point C. I also had to measure out from the centerline of the vehicle to the passenger side of the vehicle at 2365 mm / 93.11 inches, this would be point E. I placed a second 4-line laser in tandem with the first laser to make the process easier for measurements and achieve my target set point (Figure 6).
Once the target was in place, I had to level it on the floor, so it stood vertically and horizontally correct using the adjustable knobs on the target stand. The cone target on the stand had to be adjusted about 521 mm / 20.51 inches off the shop floor and fine-tuned with its red laser pointer to hit the area on the rear passenger quarter panel to where the Blind Spot Module was located. Once this was all set and the area was all clear of any obstructions, I commanded the radar unit to emit a radar wave towards my target using the ADAS software. I was shocked to see a reading of 38.02 degrees positive when you were only allowed about -3.6 to about +3.6 degrees (Figure 7). There was something terrible wrong behind that bumper, and you could also see a slight mark on the bumper in the area of the module if you looked close enough (Figure 8).
I instructed the body shop tech to pull the bumper so I could inspect the quarter panel or module bracket for issues. When the bumper was removed, I was further shocked to see that the quarter panel that the blind spot module bracket was mounted to had been pushed in (Figure 9). The body shop tech explained that this vehicle could have been hit in a parking lot or the owner could have backed up into something where the bumper guard was pushed in and the quarter panel was comprised. The elasticity properties of the bumper guard allowed it to spring back into its normal position after the hit—only leaving behind a rub mark. The body tech grabbed his special set of tools and told me the hit was not so bad and he could access the quarter panel from the trunk to straighten it out back to its original position.
I watched this guy go to work and I was extremely impressed by how well he managed to reshape the area of the hit. The manufacturer did have a tolerance of a 3.6-degree swing from center of the mounting area, so I was hoping he could put the panel close to where it had to be. Once he was finished, I again commanded the Master Blind Spot module to emit a radar wave to the target and I was amazed to see a reading of -1.82 degrees (Figure 10). The quarter panel was not pushed in that bad and required no paint or material. It was an easy fix to satisfy the ADAS system and safely put the vehicle back on the road. Had this quarter panel been severally damaged, this would have been a costly measure involving replacing the entire quarter panel.
The job was done, and the body tech put the vehicle back together. The entire process took him less than an hour. It was now up to the shop owner to deal with the owner of the car and the insurance company to see who pays for this repair as well as my fees. This is one case where I feel that pre-repair scans play a vital role in finding underlying issues that may not be seen when you are estimating damages on a car. If these vehicles are fully scanned, you may come across prior issues that have nothing to do with the accident, and you may need to address them prior to finalizing a claim. This would make life a lot easier for all parties involved in the repairs of the vehicle and for unwanted repairs that may not be covered. I hope that this article has touched home with many of the readers out there and has enhanced what you know or do not know.
About the Author
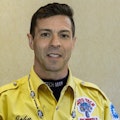
John Anello
Owner and operator of Auto Tech on Wheels
John Anello is the owner and operator of Auto Tech on Wheels, established in 1991 in northern New Jersey. He provides technical assistance and remote reprogramming with 21 factory PC-based scan tools. Driven by a passion for cars, John's business now services roughly 1,700 shops.