If shops were polled on the least popular tasks they perform, wiring repairs certainly would finish near the top. Wiring work falls right into the wheelhouse of mechanical repairs where techs often fashion themselves as new-world bug hunters chasing down the sources of electronic issues. In collision work, electronic issues are frequently the product of damaged wiring, much of it compressed or crushed wiring or terminals that can be difficult to spot and just as challenging to repair. This work is frequently tedious, frustrating (since techs sometimes encounter multiple damaged areas that can bedevil the functioning of electronic components) and stressful as the hourly investment a shop must put in can have a serious impact on cycle times.
Making things worse, techs can make a difficult chore even harder by rushing their work and damaging wiring they must recover. At other times, they can miss important details, such as using the wrong gauge of replacement wire or shifting wiring to vehicle areas where it can be damaged by excessive heat. Fortunately, all these ills have a single solution – access the OEM repair instructions and follow them to the letter.
Refer to the following instructions from General Motors for the 2021 Chevrolet Colorado. Note how the steps are not overly-complex but feature very specific directions on using new sets of special tools from GM, specific replacement wire gauges and instructions on protected vehicle areas. These instructions are important reminders of how repairs that sometimes appear to be the easiest to complete also can cause the greatest problems – because one gets a bit rushed or overconfident and doesn’t stick to the latest steps from the manufacturer.
Folded-over wire repair
Special Tools
· EL-38125-10 Splice Sleeve Crimping Tool (non GM North America)
· J-38125-5A Ultra Torch Special Tool
· J-38125-8 Splice Sleeve Crimping Tool (GM North America)
For equivalent regional tools, refer to GM’s Special Tools documentation.
Danger: In order to reduce the risk of personal injury, loss of high voltage isolation to ground and higher system impedance, do not attempt to repair any HV wiring, connector, or terminal that is damaged. High voltage coaxial type cables are not repairable. Never attempt to repair a coaxial type cable. The entire cable/harness or component must be replaced. In order to maintain system integrity and personal safety, never attempt to repair any high voltage wiring, cables, or terminals. Performing this procedure on high voltage circuits may result in serious injury or death.
The GM global wire repair strategy uses connector assemblies (pigtails) and terminated leads to repair wiring harnesses. The service pigtails and terminated leads are designed with the largest wire gauge size that can be held by either the terminal or the connector housing.
The folded over wire repair technique, in which the copper wire strands are folded over before being installed into a splice sleeve, allows the service part to be used when repairing a smaller gauge size wire in a vehicle.
For this repair, the larger harness size wires will be placed in one side of the splice sleeve and match the splice sleeve closely in size. The wires are moved into the splice sleeve until they hit the stop in the splice sleeve. The smaller harness size wires will be placed in the other side of the splice sleeve. The smaller harness size wires will be folded over to match up with the splice sleeve size.
Use the folded over wire repair for:
· Increasing the amount of copper strands in the smaller gauge size to provide a better crimp
· Splicing wires of different gauges.
Note: When performing wire-to-wire repairs with wires of different sizes (Example: installation of Terminated Leads or Pigtails), refer to the GM’s Folded-Over Wire Selection Table document. Use the Service Information (SI) connector end-views section of this table to determine:
· Gauge size of wiring harness
· Recommended Repair: Terminated Lead or Pigtail
Follow these steps to use the folded over wire technique on an IP Harness.
1. Strip twice the amount of insulation on the smaller wire (IP Harness is the lower wire) than normally required. Normally, the terminated leads have 5 mm of insulation stripped off the wire.
Note: Use EL-38125-10 splice sleeve crimping tool (non GMNA) or J-38125-8 splice sleeve crimping tool (GMNA).
2. Twist the wires before you fold them over to prevent the wire strands from opening up. Fold over the copper wire strands of the smaller gauge wire so that it is the same length as the non-folded wire.
3. Insert the folded over wire into the splice sleeve.
4. Use the proper crimp tool to crimp the splice sleeve to the smaller wire (harness side of repair).
5. Complete the crimp as usual (using the heat tool to shrink the tube).
Repairing Connector Terminals
Special Tools
· J-38125–580 Terminal Repair Kit
· J-38125-6 Crimp Tool
· J-38125-7 Crimp Tool
· J-38125-8 Crimp Tool
· J-38125-64 Crimp Tool
· J-38125-101 Crimp Tool
· J-38125-641 Crimp Tool
· J-38125-642 Crimp Tool
· J-38125-643 Crimp Tool
For equivalent regional tools, refer to GM’s Special Tools documentation.
Use the following repair procedures to repair each type of terminal:
· For push to seat terminals, refer to GM’s Delphi Connectors documentation.
· For pull to seat terminals, refer to GM’s Delphi Connectors documentation.
Note: The first step for all terminal repairs is to find the connector end view in SI.
Cable Seal Terminals
1. Cut off the terminal between the core and the insulation crimp to minimize any wire loss.
2. Remove the old seal.
3. Apply the correct cable seal, per the wire gauge size, from the kit. Slide the seal back along the wire to enable removal of the insulation.
4. To minimize wire loss, remove only the amount of insulation required.
5. Using the connector end view, determine the correct crimp tool and crimp jaw.
6. Align the seal with the end of the cable insulation.
7. Position the stripped wire and seal in the terminal.
8. Hand Crimp the core wings first.
9. Hand Crimp the insulation wings around the seal and the cable.
Unsealed Terminals
1. Cut off the terminal between the core and the insulation crimp to minimize any wire loss.
2. To minimize wire loss, remove only the insulation required.
3. Position the stripped wire in the terminal.
4. Hand Crimp the core wings first.
5. Hand Crimp the insulation wings around the cable.
Micro-Pack 100W Size Terminal
The Micro-Pack 100W connectors have small terminals that are difficult to handle and hold when crimping. In order to aid the technician when crimping these terminals, a new crimping tool was developed. The J 38125-101 (W jaw) crimping tool was developed to crimp these terminals. The J 38125-101 (W jaw) crimping tool provides a terminal holding block that holds the terminal in place while the terminal is being crimped. After the terminal is removed from the connector, perform the following procedure in order to repair Micro-Pack 100 terminals.
1. Cut the wire as close to the terminal as possible.
2. Note: After cutting the damaged terminal from the wire, determine if the remaining wire is long enough to reach the connector without putting a strain on the wire. If the wire is not long enough, splice a small length of the same gauge wire to the existing wire, then crimp the new terminal on the added wire.
3. Strip 5 mm (3/16 in.) of insulation from the wire.
4. Depress the spring loaded locator of the J 38125-101 (W jaw) crimping tool until the terminal holder is completely visible.
5. Insert the terminal into the crimp tool until the core wings are flush with the anvil on the crimp tool. Be sure that the wings are pointed toward the crimp tool former and release the spring locator. The locator will hold the terminal in place. Inspect the alignment of the terminal wings with the crimp tool former. If the terminal wings are wider than the crimp tool former, remove the terminal and bend the terminal wings in slightly.
6. Place stripped wire into the terminal.
7. Crimp the new terminal to the wire. If a jam occurs, press the emergency release to open applicator.
Micro 0.64 Size Terminal
The Micro 64 connectors have small terminals that are difficult to handle and hold when crimping. In order to aid the technician when crimping these terminals, the J 38125-64 (M jaw) was developed. The J-38125-64 crimping tool has a terminal holding block that holds the terminal in place while the terminal is being crimped. The J-38125-64 crimping tool also is designed to crimp both the wire and the insulation at the same time.
After the terminal is removed from the connector perform the following procedure in order to repair Micro 64 terminals.
1. Cut the wire as close to the damaged terminal as possible.
2. Note: After cutting the damaged terminal from the wire, determine if the remaining wire is long enough to reach the connector without putting a strain on the wire. If the wire is not long enough, splice a small length of the same gauge wire to the existing wire, then crimp the new terminal on the added wire.
3. Strip 5 mm (3/16 in) of insulation from the wire.
4. Depress the spring loaded locator of the crimping tool until the terminal holder is completely visible.
5. Insert the terminal into the appropriate terminal holder until it hits bottom and stops. The correct terminal holder is determined by the wire size. Also ensure that the terminals wings are pointing towards the former on the tool and the release locator.
6. Insert the stripped cable into the terminal. Insulation should be visible on both sides of the terminal insulation wings.
7. Compress the handles until the ratchet automatically releases.
8. Place the terminal into the appropriate cavity and assemble the connector.
High Temperature Wiring Repairs
Identifying High Temperature Wiring
Note: High temperature areas are located near exhaust manifolds, catalytic converters, exhaust pipes and turbocharged engines.
Wiring that is exposed to high temperature, 275 degrees Fahrenheit (135 degrees Celsius) or higher, for prolonged periods of time need special considerations when making wiring repairs. Areas that may be exposed to higher temperatures can be identified by heat resistant materials that are being used in those areas. These materials may include heat reflective tape and high temperature shrink tubing. Also conduit and other protective coverings may be used. Because conduit or similar coverings are used throughout the vehicle regardless of the temperature, it may be necessary for the technician to determine if an area is exposed to excessive heat before making a wiring repair.
Note: All wiring repairs need to be conducted no less than 7 9/10 in. (200 mm) from a heat zone. Areas of consideration would be any those located near the exhaust manifolds, catalytic converter, exhaust pipes and turbocharged engines.
Items Required
· DuraSeal splice sleeves to crimp and seal connections (refer to Standard parts catalog for Part Number)
· High temperature SCT1 shrink tubing to protect the splice sleeves (refer to Standard parts catalog for Part Number)
· Terminated leads or pigtails
· The correct tools to remove the terminals from the connectors.
Use high temperature bulk wire rated at 302 degrees Fahrenheit (150 degrees Celsius) continuous temperature of the same or larger gauge size as the original wire when repair damage wire. Also replace any reflective tape removed during the repair.
High Temperature Wiring considerations
Wiring that is exposed to high temperatures for prolonged periods of time may use materials, for example, wires, connectors and shielding that has a higher heat rating than typical wiring. When making a repair in a high temperature area observe the following:
1. Use high temperature bulk wire rated at 302 degrees Fahrenheit (150 degrees Celsius) continuous temperature to replace any damaged wire.
2. Replace any heat shielding that is removed.
3. Cover any DuraSeal splice sleeves with SCT1 shrink tubing.
4. After making a wiring repair, ensure that the location of the wiring is not moved closer to the heat source.
About the Author
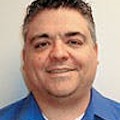
Tim Sramcik
Tim Sramcik began writing for ABRN over 20 years ago. He has produced numerous news, technical and feature articles covering virtually every aspect of the collision repair market. In 2004, the American Society of Business Publication Editors recognized his work with two awards. Sramcik also has written extensively for Motor Age and Aftermarket Business World. Connect with Sramcik on LinkedIn and see more of his work on Muck Rack.