Diagnosing and fixing an Allison Hybrid EP 40/50 no start
It can be very taxing sometimes finding faults on the such heavily networked busses of today. On an Allison Hybrid, many messages are sent from the Gateway module so it can start. There must also be valid messages from the Dual Power Inverter Module, Energy Storage System, Transmission Control Module and the Vehicle Control Module, too. So, if one of these components malfunctions, how do you figure out which? And how do you do so efficiently? In this article, I am going to show you how I logically approached this problem using scan data and oscilloscope captures.
Scan tool data
I entered the vehicle and noticed that the Shifter is not powered up. After seeing this, I decided to use the Allison Doc (the OE scan tool) to see if I can communicate with any of the modules within the hybrid system. The laptop software is telling me that it cannot communicate with any of the modules on the network that pertain to Allison (Figure 1).
So after seeing this (and also noticing that my dash is not booting up either), I used my Picoscope (PC-based 4-channel oscilloscope) and sampled from CAN HI and LO at the J1939 Powertrain Data Link Connector to see if I have any activity on the bus. Getting to the connector took hardly any time at all. That is the reason I chose to measure at this location. It was a quick and easy location to access to see bus activity. I captured the information and see that I have an issue on my communication lines. Just by a glance, I see that my CAN LO is not pulling down past 1.5 Volts. So I do have an issue present. Let’s zoom in on the capture and see if we can see anything else noticeable. As we look at the capture (zoomed in) we see that the bias voltages are low for both CAN HI and CAN LO. Respectively, they should be at 2.5 and 2.4 Volts Bias. Something is loading the CAN bus and causing this issue (Figure 2). Now, we do see pulses on the bus, but unfortunately (since the CAN bus is loaded), the TCM, VCM, the Cummins ECU and Meritor ECU cannot output or receive proper data.
So what is our next step? I decided to pull the paneling out (at the TCM and VCM) inside the bus first. Pulling this panel is very easy compared to trying to pull connectors at either the Cummins ECM Connectors or ABS unit. Another reason why I wanted to go here first was because there was no wake-up signal available at the shifter. If you do not have a wake-up signal to the shifter, and also notice that you have no wait-to-start lamp function, this leans towards a few potential faults:
- A low voltage input to the TCM (and thus, nothing is powering-up)
- A voltage or ground issue with the shifter.
As indicated by my CAN bus trace, the system is being pulled down. If it was just a power or ground issue, the CAN bus bias would be more elevated (in an accessory or a dormant mode) as it is here. This is a known-good capture of the Allison CAN bus in a dormant sleep mode (Figure 3).
I had a hypothesis to follow up on. I saw that there was no output from the multiplex module to the shifter. If the TCM had awakened, it would have signaled the multiplex to energize the shifter. To prove this, you can see that the multiplex output LED # 6 is not illuminated (Figure 4). I then energized the ignition-supply wire for the shifter (with a PowerProbe) and the red LED of the shifter illuminated, indicating it is functional (Figure 5). The display on the shifter, however, shows a set of dash lines crossing each other on the display (which means no communication). Thus, this information directed me to investigate the TCM’s functionality.
What were my findings?
I pulled the paneling off of the road side of the bus to gain access to both the TCM and VCM. I removed the connectors, for inspection. The connector to the TCM was wet, and both the ignition and the ground wire terminals were green with corrosion (Figure 6). With the TCM disconnected (which removed it from the communication bus) the scope trace resembled a normal communication waveform (Figure 7).
After I cleaned the corrosion from the TCM and its connector, I also checked for water intrusion at the VCM. None was found. I re-mated all the connectors and the dash, as well as the shift selector were awake, but the vehicle still would not start. I was finally able to communicate with the TCM and VCM, via scan tool, and there were 20 codes stored.
What are these codes telling us?
All of these codes stored pointed us to a communication stop, with the TCM. Either by a fault in the bus circuitry, loss of power or ground supplying the TCM, or perhaps the codes are indicating the TCM is not supplying a wake-up signal. I started looking at the freeze frame data (for all the codes) and the only codes that clued me into the problem being with the TCM were codes 17-14 and 17-15 (Inverter A and B Hardware Enable mismatch). As seen by the freeze-frame, it indicated low TCM voltage (for both codes). Since the TCM had low voltage, it could not communicate with any of the modules on the network. This resulted in a no-start, because it was not receiving signals from the TCM. The water intrusion caused the low voltage and also made the CAN bus voltage go down (resistively shorting the circuit to ground).
So after seeing this data, I was 100 percent sure that the TCM was damaged by the water intrusion and was no longer able to communicate properly with any of the modules on the Powertrain Network. After replacing the TCM, the bus came back to life and no more diagnostic trouble codes (from Allison) were present.
Communication problems can be quite tasking, but if you have a plan of attack and use the info in front of you, these issues can be solved efficiently. An oscilloscope wasn’t a necessity. But choosing to utilize it helped me see the deficient CAN bias voltage. It would have taken me much longer to isolate the cause otherwise. These are the tools and the testing techniques that are not found in the service information and flow charts published. They are developed over time and come from an understanding of the vehicle I’m working with and the tools used to capture the faults.
About the Author
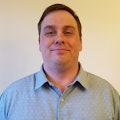
Michael Eilbracht
Michael Eilbracht is a transit bus technician for the Champaign and Urbana Mass Transit District in Urbana, Ill., and is the owner of MJE Diagnostics, a heavy-duty mobile diagnostic and training business. He is also an ASE Certified Master Transit Bus Technician and also holds an Advanced L2 Certification.