New technologies and standards are in store for refrigerant recovery/recycle equipment.
By law, every R&R machine sold — new or used — must be certified to meet the SAE standard J2210. In December, SAE announced the new J2788 standard that defines new performance requirements for R&R equipment. The EPA is planning to update its rules too by requiring shops to purchase only those machines meeting the new standard.
But the rulemaking process takes time, and EPA's Dr. Steven Anderson, who spoke at the conference, says at this point, "SAE is requiring that the equipment cannot be labeled to the old standard after December (2007). Implementation of (upgrading equipment) in the market is being accomplished by the SAE standard," meaning EPA rules do not drive the upgrade. EPA rules will be updated, but he says it will take at least several months.
Anderson also says the EPA plans to allow distributors to sell older specification equipment for a period of time after December 2007 to use existing inventory. However, the Agency will set a "drop-dead date," after which that equipment no longer can be sold. That date had not been determined at press time, but other sources within the EPA believe it will be announced later this spring.After that date, a shop purchasing service bay R&R machines must purchase new equipment that meets J2788 standards in order to obtain Section 609 Certification required to be in the air conditioning (A/C) service business. Anderson notes shops will not be required to replace existing equipment: "(The) EPA absolutely favors voluntary programs. We don't intend to go out and sweep up obsolete equipment, but we do intend to create incentives for the equipment to be retired."
Beginning in December 2007, only equipment meeting the new specifications will be made. In 2008, shops could buy only new or used new-spec equipment, but no one will be forced to stop using their existing equipment.
Instead, the EPA is looking for ways to make it attractive for shops to retire older specification equipment sooner and switch to the new machines. During the press conference, Anderson mentioned the word "rebate" and suggested funding could possibly come from the Chicago Climate Exchange. While this statement was speculation, it was intended to show that the Agency is actively searching for incentives for shop owners to upgrade to the new A/C service equipment.
Shops should expect to pay more
One reason those incentives may be needed is the expected rise in the price of new R&R equipment. Brian Berdan, A/C product manager of SPX Service Solutions and a presenter at the press conference, described the company's new Robinair Model 34788, an R&R machine fully compliant with J2788 standards.Berdan says "the technology that's required to meet these new standards is expensive" and the new machine will retail for about $500 more than its previous top-of-the-line model. Berdan says new requirements for the machine say it:
1. Must recover 95 percent of the refrigerant in 30 minutes.
2. Must have a charge accuracy of plus/minus 0.5 ounce.
3. Must lock out the user when filter service is required.
4. Must minimize cross-contamination when switching from one oil to another.
Berdan explains the machine includes an on-board computer and database that allow it to be operated in a fully automatic mode. While these are optional features, the lockout requirement makes it likely that software and computer controls will be required on all new R&R machines, accounting for at least part of the cost increase. The other major cost factor is hardware needed to meet recovery and charge accuracy specifications.
Specs are for certification only
The specifications calling for 95 percent recovery and a charge accuracy of 0.5 ounce (14 grams) are for certification only. In conversations with SAE and RTI engineers, we learned such tight tolerances can be reliably measured only in the lab, and no one really expects to hold those tolerances in the field. Machines built to perform at that level in the certification lab will be far superior to what's used now because old certification standards say nothing about charge accuracy.In the certification lab, the R&R machine will be weighed on a special scale with a resolution of ±1 gram. After the machine's starting weight is recorded, the hoses are connected to the test A/C system and the refrigerant charge is recovered. Then the hoses are disconnected and laid across the top of the machine, and the final weight is recorded. Because the weight of the refrigerant in the test A/C system is known, the refrigerant in the machine's holding tank and hoses equals the amount recovered from the test A/C system.
The test A/C system is a copy of that used in the 2005 Chevrolet Suburban with rear A/C. It has an orifice tube on the front evaporator and a thermal expansion valve (TXV) on the rear evaporator, a receiver/dryer and a suction filter in front of the compressor. This is a large system with lots of places where refrigerant can hide from a vacuum pump. However, the total refrigerant charge is 3 pounds (48 ounces), and recovering 95 percent means up to 2.6 ounces can remain in the system and the machine will still pass the certification test.
Why all the fuss?
The first specification standard for R-134a recycling equipment was written in 1988 and deployed in 1991. There have been several updates, but the basic strategy behind the standard has not changed.
SAE Standard J2210 defines equipment that can recover R-134a from a mobile A/C system by pulling the system to 4 inches of mercury (105 mmHg) below atmospheric pressure and maintaining that vacuum for 30 minutes. It was assumed that this would be enough to recover all the refrigerant in the system. Though field experience showed this isn't quite true, it was years before it was measured how much was left behind.
At SAE and EPA's urging, engineers at General Motors ran several tests of the same equipment used by its dealers by recovering a known refrigerant charge from a 2005 Chevrolet Suburban with rear A/C. After each recovery cycle, the vehicle sat at room temperature for 24 hours, then a second recovery was run on what should have been an empty system. Each second attempt recovered, on average, another 5.5 ounces (160 grams) of refrigerant, roughly 10 percent of the total charge. Further testing revealed that on smaller systems and at low ambient temperatures, up to one-third of the charge can remain in the system.
When pressure decreases, so does temperature. Reducing system pressure during the recovery process reduces the temperature of the refrigerant and everything it touches. After a small drop in pressure, the temperature is low enough in some parts of the system to freeze any moisture. If moisture is near the expansion device, it can form ice that seals that part of the system, shielding it from vacuum. Refrigerant on the other side of that blockage can remain in a liquid state.
So simply holding a vacuum on the system — even for an extended period of time — may not cause any more liquid to evaporate because of the cold temperatures and the vacuum not reaching every part of the system. Adding heat to the system helps, which is the reason for warming the engine to normal operating temperature before starting the recovery job.
Incomplete recovery leads to overcharging because charge quantity specifications are based on an empty system. In addition to reduced cooling efficiency, overcharging can drive high-side pressure dangerously high on hot days, increasing the stress on compressor seals and generating more tailpipe emissions. Excess oil in the system slows cooling by coating heat exchanger tubes, reducing efficiency; the natural tendency is to compensate by increasing the refrigerant charge.
Complete recovery and charge accuracy are fast becoming more critical than ever. Being 2 ounces low affects system performance more in a 2003 Nissan Altima that holds 17 ounces of refrigerant than in a 2003 Ford Excursion with rear A/C that holds 56 ounces. As manufacturers try to reduce the lifetime carbon dioxide (CO
The real goal
According to the National Oceanographic and Atmospheric Association (NOAA), 20 percent of all the R-134a in the world is loose in the atmosphere.
According to the EPA, almost 65 percent of that comes from mobile air conditioners, making the Agency responsible for working on that part.
The EPA consulted with the automobile industry, A/C service equipment manufacturers and SAE, and in 2004 formed the Improved Mobile Air Conditioning (IMAC) Task Force, which consists of four teams with different responsibilities. Team Four is aimed at reducing R-134a emissions during vehicle service and disposal.
It has resulted in new standards for R&R machines, new standards for leak detectors (J2791) and recommendations for improved hose couplings. IMAC's ultimate goal is to avoid having to replace R-134a with a new refrigerant and force a redesign of the automotive air conditioning system. Improving the A/C system will reduce emissions and new service equipment will help, too.
Over the next few years, look for stricter certification requirements and an increased emphasis on training.
About the Author
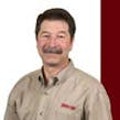