Federal Motor Vehicle Safety Standards (FMVSS) specify stopping distances for passenger cars and light trucks based on vehicle weight, loading, pedal effort, system design and several other factors. Manufacturers have no trouble building vehicles that surpass these specifications, but vehicle testing is only conducted on new vehicles using OE components. Installing aftermarket brake parts can change everything, and the aftermarket parts manufacturers are not required to vehicle test their parts. Instead, many test the brake friction material in a laboratory using their own standards, OE guides or an SAE recommended practice. The SAE test determines a friction material’s friction coefficient, and finished parts made with that material are imprinted with what’s called an edge code — an identification system for describing the material’s friction coefficient. This test cannot measure the quality or stopping ability of a finished brake part, however, because the size, shape and design of the pads or shoes all affect its performance. This basic SAE test is merely a measure of the friction that can be generated by that material under standardized conditions. There are literally thousands of ingredients and limitless numbers of combinations used to make brake friction material. Particle size and the shape and distribution of each particle can affect wear, noise, dust generation and, most importantly, brake performance. Identical brake pads made with all the same materials in the same percentage, but with different particle sizes, will perform differently. Vehicle testing, while valuable, is extremely costly and has too many uncontrolled variables to accurately test all these combinations, so the brake manufacturing industry has developed a set of tests that can measure a friction material’s performance in the laboratory under a variety of conditions. These are not vehicle tests, but they can be used to compare the performance of aftermarket friction materials with the material that was used on the production vehicle for FMVSS certification. Clarifying methods The BEEP is a certification program based on data generated using SAE J2430, a test procedure that was developed in the late 1990s. This test differs from the earlier SAE friction material characterization in that it uses vehicle-specific brake parts, not just test samples of friction material. It is intended to provide an industrywide standard for describing the inertia-brake effectiveness of friction materials, and it gives manufacturers a better way to compare aftermarket friction material with OE materials. BEEP certification is issued by the Brake Manufacturer’s Council (BMC), a nonprofit organization founded in 1973 that includes 25 member companies in North America. The D3EA test was developed by Greening Testing Laboratories, which also issues the certification. Their test is based more closely on FMVSS requirements and is reviewed periodically by the National Highway Traffic Safety Administration (NHTSA). In addition to friction material evaluation, D3EA test results can be compared directly with FMVSS requirements because it evaluates the friction material used on both the front and rear brakes at the same time. This is possible because the D3EA laboratory test uses a different kind of dynamometer that mounts two actual brake assemblies that are used together on a specific vehicle platform. Laboratory brake testing is carried out on a brake dynamometer. An electric motor drives a shaft, and flywheels are mounted on the shaft to simulate vehicle weight. These can be changed to simulate the inertia weight of different vehicles. A disc brake assembly or drum brake assembly is mounted on the shaft and enclosed in an environmentally controlled chamber. When all is ready, the dyno is spun up to speed and the brake is applied with a measured force. Test results can be interpreted as brake torque, stopping distance, apply force requirement or a variety of other parameters. Powerful software is used to conduct the test and interpret the results. With a properly designed test matrix, the SAE J2430 test procedure used for BEEP certification can describe the effectiveness of a production brake pad, brake shoe, brake caliper assembly or drum brake assembly with a 95 percent repeatability rate. That doesn’t mean the test can predict a part’s real-world performance, but it provides a way to accurately compare the performance of an aftermarket part with an OE part under controlled conditions. Deciphering the differences The goal is to measure the combined performance of the front and rear brake friction material, drums and rotors, all in the same test. Greening Testing Labs says that a D3EA lab test compares with the FMVSS vehicle test with greater than 95 percent accuracy, meaning it can actually predict vehicle stopping ability from laboratory-generated test results. Both of these tests are relatively new to the industry, and both are voluntary. Previously, the only guarantee of the product’s performance or service life was the reputation of the company that made it. An aftermarket replacement brake pad can legally be made of anything, even cardboard, as long as it carries the edge code that identifies its friction coefficient. BEEP gives the industry a way to identify aftermarket brake parts that have been tested using an SAE brake effectiveness test procedure. The D3EA test certifies that those parts have been tested against government-mandated new-vehicle performance requirements. While there are differences, both of these certifications are a guarantee of quality parts to the shops that install them and to the vehicle owners who ultimately use them. |
About the Author
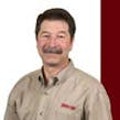