Unfortunately, much of this knowledge can’t be found in textbooks or service manuals. That’s why our sister publication Motor Age had readers send in their best technical advice. Here are some interesting fixes and time-saving tips.
Disclaimer: Publisher endeavors to collect and include complete, correct and current information but does not warrant that any or all information is complete, correct or current. Publisher does not assume any liability for any loss or damage caused by errors or omissions of any kind, whether resulting from negligence, accident or any other cause.
Fuel and emissions
Injector test
Prop the throttle open and listen in the intake to the injector spray noise level using a length of hose as a stethoscope. Trigger one injector at a time with a 2 ms triggering device. The plugged injector will sound noticeably quieter than the good ones. Cycle the key for initial pump prime between each injector test.
— Michael L. Martin, ASE Master Mechanic
Martin’s Garage, Maugansville, Md.
Diagnostics
Fuel sender tests
Fuel sending units can be tested in the vehicle with a lab scope. Configure the scope to test a TPS, connect a scope lead to the fuel gauge input wire and rock the vehicle side to side. It is best if the fuel level is near the point where the sender is suspected to be inaccurate. Erratic scope readings point to a bad sender. With the fuel sender out of the tank, configure a graphing multimeter to graph resistance through the sender as the float arm is moved. Both tests can detect a bad sender easily, but experience is needed to discern test results. Some “hash” is normal, but OBD II systems are more sensitive to a bad signal.
— Michael L. Martin, ASE Master Mechanic
Martin’s Garage, Maugansville, Md.
Brakes
Unintended low-speed ABS activation
If ABS is being activated for no reason when coming to a stop, check wheel speed sensors for proper air gap. It should be approximately 0.070 inch (1.8mm). However, some sensors cannot be checked. Also, check the toner ring for chips and/or missing teeth. If the sensor data is accessible, watch the speed reported by each sensor. If one sensor signal appears after the others, suspect excessive air gap due to rust buildup under that sensor. To repair, remove the suspected sensor and wire brush the mounting surface. Slight filing may be necessary to achieve the correct air gap.
It is common that rust under the sensor will tend to increase the gap, thus decreasing the strength of its output signal. This, in turn, will cause that sensor to stop reporting before the others when approaching a stop. For example, while the other sensors are reading 4 to 5 mph, the one with the “too-big” gap is reading zero. As a result, the module will interpret this signal as a “lock-up” on that specific wheel and will activate the ABS. The signal strength (amplitude) differences can be easily seen on an oscilloscope.
— Craig Burkhart, ASE Master / L1, HD Truck Technician
Hoffman’s Automotive, Massillon, Ohio
Fluids
Coolant removal
Here’s how to siphon coolant from a cross-flow radiator when the drain cock is not accessible. Use a 1⁄4-inch ID, 6-foot section of latex or vinyl tubing. Insert it as deep as possible into the end tank. Hold the other end lower than the radiator and blow out over the end of the tube with an air nozzle held at a sharp angle. Continue the flow of air until liquid starts to flow, then insert the end into a drain pan.
— Michael L. Martin, ASE Master Mechanic
Martin’s Garage, Maugansville, Md.
Battery terminals
How do you clean corrosion from battery terminals? Soak them in a container filled with a baking soda-and-water solution. This neutralizes the acid and cleans the cable, too.
— Michael L. Martin, ASE Master Mechanic
Martin’s Garage, Maugansville, Md.
Engine/Mechanical
Turning the crank
To align the crank pulley timing mark to top dead center (TDC), use the alternator belt. Turn the alternator nut while holding the belt tight using the tensioner and your hand. This is usually easier than trying to turn the crank pulley by its bolt.
— Michael L. Martin, ASE Master Mechanic
Martin’s Garage, Maugansville, Md.
Replacing valve stem seals
This procedure is not originally my idea, but I have found very few people who know of it. We all know the shortcomings of using air pressure to keep the valves closed and of losing air pressure with the spring retainers removed. Try this: with the valve cover, rocker arms or cams and everything else already removed, remove all the spark plugs. Using a socket on the crankshaft pulley bolt, turn the crank until the piston in the cylinder you’re working on is all the way down. Cut a 3-foot section of 3⁄8-inch nylon rope and feed about 2 1⁄2 feet into the cylinder through the spark plug hole. Turn the engine forward until the piston pushes the rope against the head, then keep turning to put about 35 to 45 foot-pounds of torque on the crank pulley bolt. The valve spring retainers can be removed without fear of the valve falling into the cylinder. When finished, simply turn the crank backwards to release pressure on the rope and carefully pull it out of the cylinder.
— Joseph Cantrell
Stockbridge, Ga.
Tools
Coolant removal
I’ve found a water/coolant suction gun that really works and won’t rust like a metal suction gun. This device is a “drenching gun,” used by veterinarians and farmers to shoot medicine down the throats of animals. We use this large “gun” to suck down radiator coolant in the tank so we can inspect the tubes, add stop leak and adjust the coolant level.
The gun has a strong plastic squeeze handle, a translucent acetate 200cc barrel and a 7-inch-long, 3⁄8-inch diameter tube end. We removed the round nozzle end and added a length of hose for longer reach.
Please note: the piston O-ring is not compatible with oil but works OK with coolant solutions. It’s available in different barrel sizes, but not from automotive tool suppliers, only Ag/Vet suppliers.
— Michael L. Martin, ASE Master Mechanic
Martin’s Garage, Maugansville, Md.
Electrical/Electronic
Test probes
In Richard McCuistian’s article “N E W = Never Ever Worked,” (Motor Age, June 2004, page 20) a photo shows meter leads backprobing a sensor connector. It’s a very intrusive test; the leads of the meter must have ruined the connector.
To avoid causing more problems than I fix, I use “T” pins from fabric or craft stores. Available in various sizes, they are chromed and have a nice point. The top is shaped like a “T” so your test lead clips nicely on either side.
— John Conley, ASE Master Tech L1
Bumper To Bumper Automotive Inc., Norwood, Mass.
About the Author
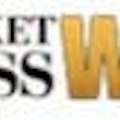