More than 40 percent of the new cars sold in Europe last year were powered by a diesel engine. Betting that the diesel market will grow here too, Volkswagen, Audi and Mercedes-Benz all plan to launch new diesel engines in the United States starting in 2005.
Using low-sulfur diesel fuel that’s expected to become available everywhere in 2006, those vehicles will be ready for strict new diesel emissions standards that take effect here and in Europe over the next few years. A big part of the reason these engines run so clean is that they are equipped with electronically controlled direct fuel injection, in which the fuel is injected directly into the combustion chamber instead of into a prechamber in the cylinder head.
Electronic diesel fuel injection
Direct Injection (DI) on small diesel engines is not new, as VW’s 1.9L TDi has been on sale in this country since 1996. Electronic controls on this and other small diesel engines also are a mature technology, but they’re different from those used on larger engines. In the TDi’s pump-line-nozzle fuel injection system, only the injection pump’s speed/load governor is controlled by the PCM. Most of the injection event itself is still determined by mechanical design features, such as cam profile, regulator valves and timing springs. But while the injectors do communicate with the PCM through a needle lift sensor, they are still completely pressure operated and therefore cannot be manipulated by the PCM to suit different operating conditions.
In contrast, the DI systems used on larger engines, including International Truck and Engine’s Power Stroke, have electronically controlled injectors. The PCM can control fuel quantity, start-of-injection, rate-of-injection and other critical functions that affect fuel efficiency and emissions at all speed/load conditions because the PCM controls the injectors themselves.
Developing a new electronically controlled injector for light-duty DI diesel engines presents some big challenges. Like the mechanical injector, it has to be robust enough to handle the extremely high fuel pressures needed for direct injection. But unlike every other diesel fuel injector, it must be completely electrically powered — able to open and close by itself without relying on assistance from outside hydraulic pressure — just like a gasoline injector. A traditional solenoid valve strong enough for that job is either quite large or requires lots of electrical power, or both. To solve these problems, engineers at Siemen’s began developing another way to operate an injector using a “new” technology that’s actually been around for quite some time.
A new technology
Piezoelectricity (pee aa zo) was first discovered in 1880 by two Frenchmen, Pierre and Jacques Curie. They were able to demonstrate that certain specially prepared crystals will generate voltage when subjected to mechanical stress, which we in the non-
scientific world call bending or impact.
The following year, they learned that the reverse reaction also is true: that those crystals will become stressed and actually change their physical shape when voltage is applied to them. The scientific description of this is complicated; stated in plain language, given the right crystal material with the right structure and the right temperature conditions, the relationship between mechanical and electrical energy conversion in these crystals is basically direct. For a given mechanical stress input, the electrical output will always be the same, and vice versa. This kind of repeatability means that piezoelectric crystals can be developed into a useful tool, although it was long after this discovery that any serious development work began.
The first real-world application was sonar, developed at the end of World War I. It works by sending a single high-voltage pulse to a piezoelectric crystal submerged in water, causing the crystal to vibrate and generate mechanical energy that we know as sound. When the sound burst bounces off of something, like a submarine, and is reflected back to the crystal, the vibrations cause the crystal to generate electric voltage. The strength of that voltage signal and the time between the output and input vibrations will tell the operator the size of and the distance to the object that reflected the sound burst.
This ability to turn vibration into electricity and its reverse was soon refined using piezo crystals that can generate/respond to a range of vibration frequencies instead of just one frequency. Soon the crystals were used in radio tubes, pressure sensors, microphones, phonograph pick-ups and a wide array of research and testing equipment. A second generation of man-made ceramic piezo crystals was developed, called piezoceramics, and they can be tailor-made for specific jobs. They’re used in tone generators (that little “beep” when you push a button), ultrasonic TV remote controls, gas grill igniters, sophisticated audio equipment, fish finders and much more. Since 1980, the number of patents for specialized piezoceramics has skyrocketed, and today they’re used almost as often as any other electronic component. One application that you might be aware of is the engine knock sensor, but they’re also in a car’s warning chimes, in your cell phone and wristwatch and probably in some of your professional customers’ diagnostic equipment, too.
In all of these applications, the piezoceramics vibrate in response to an electrical, a mechanical input/output or sometimes both. The newest type of piezo devices, the piezoactuator, is the first application that is not used for vibration, but for what is called solid-state motion. For instance, some ink jet printers use piezoactuators to force ink from the cartridge. In this application, the movement of the actuator is still just a controlled vibration in response to a modulated input signal, but instead of being used to make sound, it’s used to physically pump ink through a nozzle. The actuator can control the size and shape of the ink droplets with astounding precision, but that’s at room temperature and ambient pressure. Using piezoceramic actuators in a more challenging environment requires something a bit different, and a lot more powerful.
There are several different structures that can be used to make a piezoactuator. In the simplest type, a piezo-active ceramic wafer is bonded with adhesive to a flat piece of metal called a beam. Applying a voltage to the piezoceramic causes the beam to bend into a “U” shape, but only slightly. A piezoactuator that is 1 inch long and 1/4 inch wide will bend or displace at the tips only about 0.012 inch (0.3mm), using 125 volts but only milliamps of current.
By gluing a beam to both sides of the piezoceramic, the voltage will cause the whole assembly to bulge in the middle instead of bend at the ends, and total displacement is almost doubled. By stacking a number of actuators together, the total displacements are added together; the bigger the stack, the greater the total displacement. Doing the math, a stack of 13 double actuators as described above will give a total displacement of about 0.160 inch (4mm), but that’s under no-load conditions. With a fixed wall at one end of the stack and a spring at the other end, total displacement declines almost linearly as spring pressure increases. Still, using the right design and the right materials for the beams, adhesives and piezoceramics, an actuator stack can be built that will actually do some useful work.
That brings us back to diesel fuel injectors. How much work — force times distance — does the piezoactuator stack need to do in a fuel injector? Putting it another way, can a big enough stack be built into an injector body? The answer to the second question is yes, but only depending on the answer to the first.
Direct injection
Whether it’s a gasoline or diesel engine, injecting fuel directly into the combustion chamber extracts more power with lower emissions for every gram of fuel that reaches the combustion chamber. The higher the injection pressure, the greater the improvements. But generating that pressure consumes some of that additional engine power. Still, with each new generation, engineers have sought ever-higher injection pressure as the best way to improve engine efficiency.
In traditional diesel DI systems, the high fuel pressure is generated with unit injectors that have a plunger-type pump built into the injector itself. On earlier engines, the unit injector’s pump is operated with a lobe on the engine’s camshaft, and while that’s a good way to generate very high injection pressure, it has the same control limitations as the pump-line-nozzle system described earlier. All the important functions are timed mechanically, and therefore can only be optimized for a narrow band of operating conditions. Think of it as a gasoline engine with fixed ignition timing.
Electronically controlled DI for medium-duty diesel engines arrived several years ago with the Hydraulically Actuated Electronically Controlled Unit Injection (HEUI) system originally developed by Caterpillar and popularized in Ford pickup truck engines. It still uses unit injectors, with fuel supplied to each injector from a single pump through common supply passages. But instead of generating injection pressure with a cam lobe, this system uses high-pressure oil supplied by an engine-driven pump and some well-known principals of hydraulic force multiplication built into the injector itself. (For more on this technology, see the August 1999 issue of Motor Age.) The oil pressure in each injector is controlled with a solenoid valve, so a computer can be used to control the injectors. Critical functions like pilot injection, start-of-injection and rate-of-injection can be adjusted for any speed and load, drastically improving the engine’s flexibility and fuel efficiency, to say nothing of its environmental manners.
But it’s still unit injection. The large, heavy injectors, high-voltage solenoid valves and separate high-pressure oil system are bulky and far too expensive for use in smaller engines.
Common rail direct injection
Isuzu and Bosch worked together to develop the first electronically controlled common rail DI system for diesel engines, and it debuted on GM’s Duramax. It’s laid out like a typical gasoline injection system, with a single pump supplying fuel to the injectors through a common supply rail. Like the gasoline system, all the fuel pressure is generated by the pump, not the injectors, and it’s supplied to the injectors continuously. Also, like the gasoline system, the injectors don’t need an external source of power (high-pressure oil), but are operated completely by electric solenoid valves. But that’s where the similarities end.
This system operates at 27,500 psi (1900 BAR). The injectors use a needle-and-seat-type valve to control fuel flow, and fuel pressure is fed to both the top and bottom of the needle valve. By bleeding some of the pressure off the top, the pressure on the bottom will push the needle off its seat and fuel will flow through the nozzle holes. The key to controlling that pressure bleed is a calibrated orifice and a powerful solenoid valve. While the solenoid is small enough to fit on the injector itself, it operates on 93 volts DC and requires 18 amps to open and 12 amps to hold, so two different drivers are needed for each injector.
The next generation of common rail DI will debut in late 2005, most likely on the Audi A8 diesel. It will have piezoelectric fuel injectors developed by Siemens. Like their Bosch/Isuzu counterparts, the new injectors use a needle-and-seat valve with fuel pressure supplied to both the top and bottom. The difference is the solenoid valve that controls the top-pressure bleed orifice has been replaced with a stack of piezoactuators. The stack is small enough to fit inside the injector body itself, so the injectors are compact.
This answers the question we asked earlier about how much work the piezoactuator would need to do in a diesel fuel injector. Even though it’s operating against 27,000 psi or more, it only needs to open a mere crack in a fuel passage, flowing just enough fuel to create a difference in pressure between the top and bottom of the needle.
The actuator stack operates on 125 volts DC but draws only milliamps of current, greatly simplifying the electrics and electronic controls. But its biggest advantage is low mass. Without the solenoid valve’s moving parts, the piezoactuators are able to open and close the bleed orifice four times faster than the solenoid valve. This is fast enough to allow up to five discrete needle valve openings over the course of a single injection event, and like the piezoactuator in the ink jet printer, fuel can be metered through the nozzle holes with extreme precision. It’s this precise control over rate-of-injection that makes piezoinjectors different.
With multiple small injections, pressure increase in the cylinder is far more gradual, which reduces noise and emissions at every engine speed/load. Piezoinjectors themselves are expensive, but the whole system is less expensive, smaller and requires less power to operate than everything that’s come before.
They’re coming
As diesel engineers have steadily pursued the holy grail of higher injection pressure, each advance started with parts and ideas from systems that came before. Piezoinjectors are no exception, but the piezoactuators themselves are the first new technology introduced to diesel fuel injection in a very long time.
Piezoinjectors have already been proven capable of 29,000 psi (2000 BAR), a pressure that was only dreamed of 20 years ago, and this is the first generation of development. With these new levels of pressure and precise control, the diesel engine is finally fulfilling its promise of being cleaner and more efficient than gas engines of similar power. From the size of their investment, it’s apparent that European engine-makers are betting heavily on this promise to help them reach strict new emissions targets. And all of this ripples out from a minor discovery made in a small French laboratory 125 years ago.
About the Author
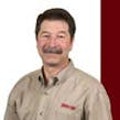