When the brake pedal pushes you, the reason might not be obvious.
When a brake pedal pulses beneath your foot, no doubt your first thought is "warped brake rotors." Your next thought might be about how it happened, because if you're going to get paid for the repair, you have to make sure it doesn't happen again. Fortunately, most of the things that cause pedal pulsation happen in the service bay. With close attention to detail, it's easy to avoid those particular comebacks.
The term 'warped brake rotor' is used pretty loosely to define any brake rotor that isn't absolutely flat and parallel with the plane of rotation. But there are other things that can cause pedal pulsation. There are also ways rotors can warp that don't produce pedal pulsation but do affect braking. Understanding these things is the only way to guard against them or deal with them successfully if they do come back.Rotor run-out
If you know how a disc brake works, it's not hard to understand why you can sometimes feel warped rotors in the brake pedal. If the rotor is shaped like a potato chip, the high spots will push back against the caliper pistons as they rotate between the brake pads. That push is transmitted directly to the pedal, and if steering or suspension bushings are worn, it might even cause a slight steering wheel shimmy.Several things can cause a rotor to warp that way. Most of us are aware that uneven heating or cooling is one culprit. A frequently cited example is driving through a deep puddle on a dry day with hot brake rotors. Another example is parking the vehicle without a "cool-down lap" after very heavy brake use, such as road racing or towing in hilly terrain. In that scenario, so much heat has soaked into the pads and calipers that it keeps one section of the now stationary rotor hot while the rest of it cools. Both of these scenarios will warp a brake rotor, but in most parts of the country, they don't happen very often.
By far, the single most common cause of warped brake rotors is improper installation of the wheel.There was a time that this was not so, but modern brake rotors are made thinner to reduce a vehicle's unsprung weight. They're not just thinner at the friction surface, there's less material everywhere, particularly in the hat section. This makes the rotor more susceptible to warping due to a combination of heat and improper lug nut torque.
Manufacturers specify lug nut torque for the same reason they specify cylinder head bolt torque: to control distortion of the parts being bolted together. Most front-wheel-drive cars have one-piece cast iron brake rotors shaped like a top hat. The hat section of the rotor fits over the wheel studs and is clamped between the hub flange and road wheel. When the rotor is mounted onto the hub, the hat section does not fit flat against the hub flange; there's a slight gap either toward the center of the hub or toward the outer diameter of the hub flange. That gap is less than two-thousandths of an inch, and on most cars, it's supposed to be there.
As the lug nuts are tightened, the hat section is pushed tight against the hub, closing the gap. This slight bend loads the hub/rotor assembly, increasing the overall strength and stiffness of both parts together.If the lug nuts are not torqued evenly, or if they're torqued evenly but over-tightened, the stress loading is uneven. After a few heat cycles, the uneven loading creates a permanent distortion, as much as three-thousandths of an inch, according to General Motors (GM). Usually the rotor face becomes no longer parallel with the plane of rotation. In that case, there won't be any rotor thickness variation. But because the rotor face wobbles between the brake pads, the brake pedal will pulse.
GM recognized this as a problem several years ago and approved the use of a product called Brake Align. These are shims that go between the hub and rotor to correct lateral runout. (See GM Service Bulletin 0105-23-001.) The most effective way to avoid this kind of rotor warping is to tighten the lug nuts in the proper sequence using a torque wrench...every...single...time.
Just as uneven lug nut torque will warp a rotor, so will contamination. Imagine the bending forces and stress risers created by corrosion, clumps of brake dust or anything else clamped between the hub and rotor or between the wheel and rotor.
Because they are dissimilar metals, aluminum wheels often corrode heavily where they contact the rotor hat. GM recommends cleaning the hub, rotor hat and wheel with a wire brush, and other manufacturers recommend brushing a thin coat of anti-seize on each surface before assembly. But remember, it's a brake system, so don't use so much anti-seize that it flings out onto the braking surfaces.Thickness variation
The late Carroll Smith, a racing driver and engineer, wrote of what he learned about disc brakes while working on the original Ford GT40 racecar, which he described as "one of the most intense brake development programs in history." Smith noted that although a brake rotor can warp in many different ways, he never saw a properly assembled rotor warp in a way that causes brake pedal pulsation. He said whether on a high-performance racecar or street-driven grocery getter, when everything is assembled properly, the most common cause of pedal pulsation results from uneven transfer of friction material from the pad to the rotor. To understand this, we need to understand two other concepts first.
Brakes are designed to work within a specific temperature range, and the friction material used to make the pad is selected with that range in mind. The reason for this is that the mixture of friction materials best suited for racing pads won't work when the brakes are cold, and the materials that work best for noise reduction can be severely overheated when used on high performance applications.
During normal use, brake pad material abrades from the pad and adheres to the rotor, forming an extremely thin layer of friction material on the rotor. When the pads and rotor are new, the bedding-in process establishes the initial layer. With continued use, the friction material is constantly being abraded away from the rotor and replaced with new material from the pad.
If the brakes are not properly bedded-in when new, or if the pads are severely overheated at any time, the transfer of friction material from pad to rotor becomes uneven. Heavier deposits can be seen as stains or dark spots on the rotor that won't wash off. Even if you can't measure a thickness variation at these spots, they will have a different coefficient of friction when hot. Since that layer of material is only microns thick, it can be cut away by turning the rotors. If uneven deposits happen again, it's time to select a brake pad that can handle higher temperatures.
Smith says this is why the ideal "all-around" brake pad doesn't exist. The friction material that works well at higher temperatures will be noisy and perform unevenly at low speeds. Pads that work well in relatively mild applications will fade when driven hard, and even mild overheating can cause uneven deposits.
A fresh surface
If the brake pads are worn but everything else about the brake system is satisfactory (flat rotors, no signs of overheating, no pedal pulsation), it can be tempting to just install new pads and be done with the job. It's also a pretty good bet that the brakes won't grip that old rotor like the old pads did, especially if they're a different friction material than when the car was new.
The main reason for resurfacing rotors is to give the new pads a fresh surface for that thin layer of friction material. So even if the rotors are still flat and true, resurfacing them is not a bad idea, provided there's enough thickness. Remember, the discard thickness specification is just that, not the minimum refinish specification.
By now the main advantage of an on-car brake lathe is well known: the resulting friction surfaces will be absolutely parallel with the plane of hub rotation. Not only does that go a long way toward eliminating comebacks, the fact that some manufacturers require their dealers to use this tool indicates it can also save time.
However, with sincere attention to detail, the older rotor refinishing tools and techniques still work just as well as ever. Before removing the rotor, it should be checked for run-out with a dial indicator. If there is run-out, it's not a bad idea to check the hub for run-out before deciding what to do next.
Other problems
Hubs can warp, wheel bearings can wear and become loose and CV-joints can become stiff and cause the stub axle to wobble ever so slightly. At worst, each of these things would produce rotor run-out that can barely be measured, but stacked together they can be felt in the brake pedal. By changing the position of the rotor on the hub, total run-out as checked with a dial indicator can reduced or maybe even eliminated.
Faulty brake calipers also can cause pedal pulsation and they can cause rotor wear that doesn't necessarily show up in the brake pedal.
Worn guide pins on a floating caliper will allow the caliper to cock at an angle to the rotor. The pads will wear unevenly; one pad will wear at the outside edge and the other at the inside edge, or one will wear more at the leading edge and the other at the trailing edge. Pedal pulsation is unlikely, unless the guide pins are so worn out that the caliper rattles on the pins .
The same kind of uneven pad wear can show up with a fixed caliper that has a jammed piston on one side. As the brake pads wear, the piston that moves freely will constantly bend the rotor slightly toward the stuck piston. With enough heat cycles, the rotor can actually assume that new shape, and the brake pads will wear unevenly. Again, the warp is extremely slight, but unless the rotor is resurfaced during the brake job, it's enough to impede bedding-in of the new brake pads.
Even just old calipers can contribute to higher-than-normal temperatures. The rubber seal on the caliper piston has a square cross-section. When fluid pressure forces the piston out, the seal cocks slightly in the groove. When fluid pressure is released, the seal springs back to its normal shape. That's the only spring that retracts the pad away from the rotor. In a high-mileage caliper that's seen millions of heat cycles, that seal won't spring back quite so completely, allowing the pad to drag just a bit longer than normal. This increases the possibility of an uneven layer of friction material on the rotor.
Is pedal pulsation dangerous? When mild, it's merely annoying, which is enough to make most people want it fixed. But even mild pulsation can influence ABS performance and increase braking distance in a panic stop situation. In extreme cases or when traction is marginal, uneven braking caused by pedal pulsation can make the car difficult to control.
Fortunately, you can control most of the causes of brake pedal pulsation, through understanding how brakes really work and by paying attention to the details.
About the Author
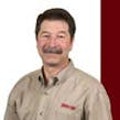