A tire is built of many separate parts, all bound together and encased in rubber. The bonding is generally latex that's specially formulated for the materials it's holding together because complete bonding is critical to strength and heat dissipation.
The rubber makes up only about 30 percent of the tire by weight, and it is a mixture of natural and synthetic materials with various chemicals added. The most important additive is carbon black, a petroleum-based soot that influences elasticity and heat resistance and provides the tires' black color (natural rubber is white).
Fillers, such as clay, silica and oil, are used to add strength and adjust hardness, and sulfur and other chemicals are used in the curing process. With the right chemicals mixed into the compound, heat curing prevents the rubber from turning sticky when hot and brittle when cold. This process, called "vulcanization," was discovered accidentally in 1839 by Charles Goodyear.
The tire carcass is made of manmade fibers, including nylon, rayon, polyester, fiberglass and aramids such as Kevlar. The yarn-like fibers are woven into wide strips called plies, and at least two plies are used to form the carcass. In bias ply tires, the plies are wrapped at a 30- to 40-degree angle to the centerline of the tire. On radial tires, the plies are wrapped straight across the certerline from bead-to-bead.
The ends of the ply strips loop around a steel cable hoop, and the space in this loop of fabric is filled with a hard rubber compound to form what's called the "bead chaffer." The steel hoop and the chaffer give the bead its size and shape, and the bead chaffer usually extends up into the sidewall to improve support and durability. The inside of the carcass is coated with a thin layer of soft rubber, called the "inner liner," to form an air seal.
For passenger car tires, the carcass is generally overlaid with two steel belts that support and stabilize the tread layer. The belts are made from thin steel wire that is sometimes brass-plated to improve rubber adhesion, and then wrapped into cords that are woven to form the belts. The belts wrap around the circumference of the tire with the individual cords at an angle across the carcass. Wedges and gum strips locate the belts, and fiber overlays are added to separate the steel belts from the tread layer.
Two layers of different rubber compounds are molded together to form the tread cap. The base layer is hard rubber that adds structure and, when the tire is cured, adheres to the belts. The top layer is a softer compound that provides grip, and the tread pattern is molded into this layer.
The tread pattern is designed to prevent water from building up under the tire, but on some tires, the tread blocks are also designed to deform or "squirm" on the pavement to generate friction. Some snow tires have a soft compound on half of the tread layer to improve grip on icy roads. Some motorcycle tires have a hard wear-resistant compound in the center of the tread and a softer compound on the sides to provide more grip when the bike is leaning into turns.
The sidewall is another component, made of special rubber that resists weathering, protects the carcass and influences the ride. A tall, flexible sidewall acts like a supplementary spring for increased comfort; high-performance tires have short, stiff sidewalls and maybe even a steel or nylon insert to add more stiffness. The outside of the sidewall is molded with all the numbers and letters, and whitewall tires have yet another layer of rubber laid over the structural sidewall.
Building a tire requires computer controls and some of the most highly skilled hand labor in the automobile industry. A computer selects the ingredients for the rubber and operates the giant mixing mill.
The resulting product is passed through rollers to expel air and more rollers to press the fabric and rubber together, forming plies of the specific size and thickness needed to build the tire carcass.
The tire builder lays the plies, assembles the bead and sidewall components and adds the inner liner. After adding the belts and tread layers, the "green tire" is inserted into the mold. The tread and letters are formed when a bladder inflates to press the green tire against the mold walls.
The computer controls the heat and duration of the cure, which are critical to getting all the various parts and materials joined together into one inseparable assembly. If the finished tire passes final inspection, it's ready for the road.
About the Author
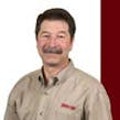