ABS, traction and stability control systems open the door to pre-accident systems.
If you wanted to tag the last 20 years of auto development with a movie title, none could be more suitable than “The Fast and the Furious.” Computer generated modeling and advanced production methods have shaved years off the design and implementation process. Technological upgrades now leap from drawing boards to showrooms in a matter of months.
As the evolution of the automobile has become supercharged, an interesting “power struggle” has erupted between driver and vehicle. On one side, auto manufacturers have delivered new levels of power and performance to all areas of the market. Buyers of even the most basic econo-cars now can count on plenty of horsepower and bang-for-your-buck fun. Unfortunately, putting all this muscle in the hands of millions of drivers facing countless distractions during their daily commutes sometimes means one thing—trouble, the kind of trouble that causes accidents. Knowing this, carmakers have provided for the occasional revolution, or outright coup d’état, in the driver’s seat.
Anti-lock braking systems (ABS), traction and stability control systems take command when circumstances—poor driving decisions, road conditions, etc.—warrant. If that wasn’t power enough, these “pre-accident” systems are evolving, incorporating additional vehicle systems as they take on more driving and safety responsibilities. They’re also commanding greater miles of roadway each year as they become standard features on more vehicles. Here’s a look at the past, present and future of these systems and how they’re shaping the automotive world.
Control technology: Building blocks of safety
Understanding pre-accident, or control, technology is tantamount to knowing how your home theater system works. Both require a modular approach. Both build upon relatively simple or basic constructs, adding more features until they produce a complex system capable of producing a number of functions.
For example, in your home entertainment center, you start with a television and DVD player then add a receiver, speakers and other components. In the end, you have a system that produces multiple combinations of image and sound. With an automobile, start with braking and add throttle control and power disbursement. The result is optimal stopping and directional control created by the interplay of several electronic systems under the guidance of one.
Module 1: ABS
ABS came to market in the mid 1980s first in BMW and Mercedes models fitted with brake technology developed by Robert Bosch GmbH. Headquartered in Stuttgart, Germany, Bosch works exclusively with German auto manufacturers (which explains why many pre-accident systems first appear in German automobiles).
ABS operates by sensing and preventing wheel lockup during hard braking situations—for example, braking while a vehicle slides on ice. The function of ABS is to restore traction during deceleration. ABS does this by automatically slowing and increasing wheel spin until the wheels create the traction necessary to stop.
ABS uses four basic components: speed sensors, pump, valves and controller. Located at each wheel or sometimes in the differential, the speed sensors indicate when a wheel is about to lock up. The valves act to release pressure on the brakes, and the pump replaces the pressure. The controller acts as the computer that monitors speed sensors and controls the valves.
The controller continually searches for unusual decelerations in the wheel, for example, rapid decelerations that typically precede a wheel lockup. When left unchecked, these decelerations cause the wheel to stop much more quickly than the vehicle, sending the vehicle into a skid. To prevent this, the controller reduces the pressure to the brake until it detects acceleration, then it increases the pressure until it detects deceleration again. ABS acts so quickly (cycle times can reach 15 per second), tire speed doesn’t significantly change. The result is that tires slow down at the same rate as the car. Because the system automatically keeps the tires near the point of lockup without allowing them to lock, maximum braking power is yielded and maximum stopping power is produced.
Anti-lock braking systems come in three basic different types, based upon channel number (how many valves are individually controlled) and the number of speed sensors. Four-channel, four-sensor ABS schemes feature a speed sensor and a separate valve at each wheel. The controller monitors each wheel individually to make sure it achieves maximum braking force. This system provides the most effective braking of the three.
In a three-channel, three-sensor ABS scheme (typically used on pickup trucks with four-wheel ABS), each of the front wheels has its own sensor and valve, while both rear wheels share the same valve and sensor, located on the rear axle. This system provides individual control and maximum braking force of the front wheels. Because the rear wheels are monitored together, they both have to start to lock up before the ABS activates. The drawback here is that one of the rear wheels can lock and thereby reduce brake effectiveness.
Pickup trucks with rear-wheel ABS sometimes feature a one-channel, one-sensor scheme, where the valve and sensor both are located on the rear axle. Operating the same as the system on the rear of a three-channel scheme, both rear wheels are monitored together and both have to start to lock up before the ABS takes command. As with the three-channel system, one of the rear wheels also can potentially lock.
Module 2: Traction Control
Following ABS to the market, traction control (more specifically, acceleration slip regulation (ASR) traction control), uses the same operational premise: maintain as much traction as possible between the tires and the road. In this case, traction is maintained while the vehicle is accelerating.
Building upon the ABS model, traction control uses the brakes along with the throttle to maintain adhesion between the vehicle’s tires and the pavement. Traction control works by preventing wheel spin in low-traction situations such as snowy or wet roads, by adjusting vehicle acceleration. In some cases, the brakes are automatically applied. At other times power is redistributed to the wheel(s) with the most traction. These actions typically are achieved either through a series of quick braking pulses or redirection of engine power through directional clutches in the rear differential.
Module 3: Stability Control
Electronic stability control (ESC) systems also use braking and throttle control elements to help drivers maintain control of their vehicles. These systems control yaw—the lateral movement of the vehicle front or back end (side skidding).
Stability control systems typically integrate ABS and traction control along with a yaw-sensing feature usually referred to as a rotational-speed sensor or yaw-rate sensor. They also can use elements such as steering angle sensors, wheel speed sensors and hydraulic modulators.
A system with all these elements would act accordingly. The yaw-rate sensor determines if the vehicle is rotating in a turn. A microcomputer examines this information and correlates it with data on steering angle, wheel speed and accelerator position. If the system determines there is too much yaw, it activates individual or a combination of brakes and sometimes throttle control, until it determines the vehicle is stable.
Stability control systems are marketed under a number of names. Bosch-designed Mercedes systems are referred to as an Electronic Stability Program (ESP) while its BMW stems are marketed as Dynamic Stability Control (DSC) and Cornering Stability Control (CSC). Delphi markets a TRAXXAR system. Auto makers use a variety of monikers, including AdvanceTrac for Ford and Active Safety for many General Motors’ (GM) models. While these systems share a basic architecture, each operates and offers different levels of performance according to its own unique engineering. For example, GM’s Active Handling Chassis Control System (built by Delphi) allows more oversteer for the Corvette than other vehicles. Greater oversteer allowance is designed to give the Corvette more sports car-like handling.
Future Control: More systems, more integration
The next generation of pre-accident systems offer upgrades in the form of more effective ABS and traction and stability control systems, along with integration of other systems. Phil Cunningham, Director of Chassis Systems Product Planning for TRW, notes that his company has integrated suspension and steering control into its Active Roll Control (ARC) system, a stability control system designed to prevent rollovers in vehicles such as SUVs.
In an ARC setup, stabilizer bars linking both sides of the suspension connect to computer-controlled actuators. These actuators use hydraulic pressure to move the ends of the bars. When an accelerometer sensor detects lateral movement during cornering, a computer signals for increased hydraulic pressure. Hydraulic pressure, produced by the power-steering pump and valve, powers the actuators to move the stabilizer bar—reducing body lean and holding the vehicle flatter. In 2002, TRW and GM integrated ARC in the GM Safari.
Ford has followed suit by being the first auto manufacturer to engineer its own anti-roll system. Integrated first on the 2003 Volvo XC90, Ford’s Roll Stability Control (RSC) continuously monitors roll potential and intervenes when it calculates a vehicle is approaching a rollover situation. RSC utilizes a gyroscopic sensor to determine body roll angle and roll rate. It correlates this information approximately 150 times per second with data collected from other sensors, for example, yaw rate with lateral and linear acceleration. When a vehicle approaches an unstable situation, RSC reduces engine power and/or applies brakes to the appropriate wheels until vehicle stability is returned. The Lincoln Aviator and Navigator already feature RSC. Ford plans to integrate RSC on 2005 models of the Explorer, Expedition and Mercury Mountaineer. Lexus and Range Rover will offer similar systems on their vehicles.
Because SUV owners often use their vehicles to tow boats and campers, sources of potential stability problems, BMW’s new X5 3.0d will feature a stability system that monitors the pendulum-like motions of the trailer. At speeds above 40 mph, the system’s sensors begin searching for excessive motion. If so, throttle is reduced and the brakes are applied until the trailer goes back in line with the vehicle.
Regardless of what type of stability system a vehicle may use, Nick Zielinski, GM’s chief engineer for advanced vehicle integration, says engineers will continue upgrading the functionality of system modules and sensors. “This means tapping into an ever-increasing number of sensors for additional input to help system actuators, the mechanisms that activate stability control actions, react sooner and more effectively. We’re talking about reaching a whole new level of control,” says Zielinski.
One system
Frank Lubischer, director of braking systems for TRW, says along with controlling vehicle direction and motion, pre-accident systems also will branch out into a total protection system for drivers and passengers. “Stage one will be crash prevention,” he says. “Stage two will integrate interior safety systems to protect vehicle occupants in the most effective manner. For example, yaw sensors will help tell the passive restraint system to pull the driver back into a more effective driving position. Airbags will be tied into this system too and will activate in a manner that best protects the occupants.”
Lubischer and Cunningham explain that automotive engineers have begun looking at the chassis as one fully integrated, central system tied into other vehicle systems. The chassis is becoming both brain and cocoon, designed to protect passengers while commanding all vehicle operations to work together in a way that provides the safest, most efficient traveling experience possible.
Delphi uses this same philosophy to build its line of Unified Chassis Control (UCC) systems, which similarly integrate performance and safety systems into one scheme. Currently, Delphi is able to integrate offerings, such as its Active Front Steering (AFS) and Active Rear Steering (ARS) with braking systems.
Delphi also has introduced other pre-accident systems that have the potential to be integrated. These include its Lane Departure Warning system (TRW has built a similar system), which sends out audible warnings when a vehicle begins to leave its driving lane, and its Forewarn Adaptive Cruise Control with Driver Alert system. Forewarn uses a vehicle’s braking and throttle systems to automatically manage vehicle speed to maintain a headway gap (following distance) selected by the driver. The driver sets the cruise control and following distance. The vehicle responds by maintaining the set speed, automatically slowing when approaching slower traffic and accelerating when appropriate. It’s almost enough to make you consider bringing along a good book the next time you drive. Almost.
A new era for collision repair?
Looking at all the innovations in vehicle control systems, it’s tempting to wonder if the day isn’t far off when getting from point A to point B simply will be a matter of programming a vehicle autopilot. Certainly, as vehicles are given more power to protect themselves (along with their drivers and passengers) trips to collision repair facilities should be less frequent. That’s good news for motorists, but potentially bad news for you, depending upon how the collision field adjusts to keep up with the changes.
For now, rest easy. Zielinski points out that control systems aren’t designed to let motorists drive more aggressively; neither can they protect drivers in every circumstance. Motorists can and do overpower these systems and get themselves in all sorts of trouble. And they’ll need your help putting the pieces back together.
To better service these customers and help yourself in the meantime, make sure you stay up to date on pre-accident systems and learn how they affect your job. Even if you turn over their repair to a mechanical shop, these systems still are tied into a number of parts and other systems you do fix. Remember too, these systems rely on greater numbers of monitors and sensors placed around wheels and other vehicle areas. You’ll need to be aware of their locations to avoid damaging them.
You’ll also want to be aware of the direction collision repair could take based on the growing presence of pre-accident systems. As electronic and computer-based systems become more prevalent in automotive construction, understanding and repairing them grows closer to being a requirement for collision repairers. Someday, much like a mechanical technician, you might find yourself accessing on-board computers to search for damage information, using the thousands of bits of data normally collected by these systems to prevent accidents. Vehicles will tell you what happened to them and where they hurt.
With that done, perhaps the next step auto designers take is the one you’ve spent years waiting on—programming vehicles to automatically arrive at your shop the moment they’re damaged or in need of repairs.
About the Author
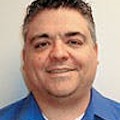
Tim Sramcik
Tim Sramcik began writing for ABRN over 20 years ago. He has produced numerous news, technical and feature articles covering virtually every aspect of the collision repair market. In 2004, the American Society of Business Publication Editors recognized his work with two awards. Sramcik also has written extensively for Motor Age and Aftermarket Business World. Connect with Sramcik on LinkedIn and see more of his work on Muck Rack.