After four years as an insurance adjustor, Andrew Batenhorst made the decision to switch to a career in collision repair, taking a job at Pride Collision, a seven-location MSO in California. What inspired him to make the switch? Batenhorst said that after visiting hundreds of repair shops as an adjustor and seeing how inefficiently they ran, he said the way that Pride Collision ran its body shops was eye-opening. After working as a blueprinter at Pride, Batenhorst now serves as general manager for two of the locations.
For over 10 years, Pride Collision has used process-centered environments (PCE) in its shops. PCEs encourage the same processes every single time; think of an assembly line or the way fast food is replicated all across the world. Shops that use PCEs use standard operating procedures (SOPs) and quality-control checks at every step of the repair process to ensure efficiency.
“[PCEs] help produce higher quality repairs, reduce waste, and allow managers and owners to easily analyze what’s going on in his or her shop,” Batenhorst says.
Each of Pride Collision’s seven steps in its repair process has an SOP associated with it. Before the vehicle can move to the next step of the repair process, it must meet the standard and be accepted into the next step.
Batenhorst warns that the transition to using PCEs is not easy, and it’s not for everyone, but with the right amount of dedication and willingness to learn, it pays off in the end. Batenhorst shares the keys to implementing successful PCEs.
Support Team
Shops that are interested in implementing a PCE don’t need to go at it on their own, Batenhorst says. Pride has a PCE consultant through it’s paint company, AkzoNobel, that provides support and helped them make the change over. Batenhorst says that AkzoNobel is not the only company that provides this and that interested parties should reach out to their vendors.
The Right Team
Although Batenhorst wasn’t there when Pride first made the switch, he knows there was a period where the shop went through growing pains and a number of people either left or had to be let go.
“This type of work environment is not for everyone,” Batenhorst says. “That’s why we make sure that we do a thorough job of interviewing to make sure we’ve found the right person.”
Batenhorst says that the right person to work in a PCE has an open mind and a willingness to learn. Anyone that thinks that he or she knows everything already will not work out in a PCE. In order to screen its candidates, Pride Collison makes sure to ask the right questions and also teams up with a third party that administers personality assessments.
Onboarding
Whether you’ve just hired a new member of the team or you’re switching your entire staff over to a PCE, Batenhorst says it’s important to take a handholding approach.
“You can’t expect someone from a traditionally run collision repair shop to adapt right away,” Batenhorst says. “It’s up to the manager and the team to onboard the new person and help them understand exactly what we’re doing.”
Quality Checks
In order for PCEs to work, SOPs need to be created—from check-in to detailing. Batenhorst says that all of Pride Collision’s SOPs have a time frame associated with each step that all of the members of the team know about and are expected to meet. Before the vehicle is taken into the next step, it’s up to the team at the upcoming stage to decide whether or not the team ahead of them has done its part of the repair to Pride Collision standards.
“It’s a seamless handoff to the next department,” Batenhorst says. “A quality control check is done, and if it meets the standard, it moves on. If not, the job will not be accepted into the next department until it does.”
Batenhorst is in charge of the final sign-off of the vehicle before it is handed off to the customer.
Productivity Checks
All of the technicians at Pride Collision are tracked on their labor hours, Batenhorst explains. At Pride, every department set a goal for how many hours they need to produce in their respective PCEs. This is how the shop tracks how each department is doing. Batenhorst says that he gives daily feedback to his staff, so it should never come as a surprise how they’re performing.
Check-Ins
Along with checking-in on a daily basis, Batenhorst says that the entire staff has two 10-minute production meetings during the day to update everyone else on where each department is at with each job.
“I ask the entire staff, ‘What are you working on? When will it be done? What are you working on next?’ After that, I find out if each department feels like they’ll meet their goal. If not, I find out what the rest of the team can do to help.”
Batenhorst explains that these meetings aren’t a way to micromanage. They’re meant to be a reminder that nobody is alone and that the team is there for support.
Batenhorst also does daily walkthroughs to make sure all of the PCEs are running properly. He takes pictures throughout and brings those photos to the daily meetings.
“If I see that the trash wasn’t taken out, I’ll take a picture of that and I’ll show it at the meeting,” Batenhorst says. “We then have a group discussion about why this wasn’t done. It makes it a team thing rather than an individual thing because these are all processes that have been established by the team.”
Plan of Action
Once the problem has been identified, the team figures out a solution. For example, a delay that lasts longer than 10 minutes in any of the PCEs is documented in what Batenhorst calls the delay tracker. That delay and what department it is in is noted. At the end of the month, the delays are discussed and the team lead from each PCE is responsible for creating a plan of action to make sure it doesn’t happen again.
“We have to make sure that we’re not making the same mistakes over and over,” Batenhorst says.
Constant Reminders
It can be easy to slip back into old habits. At Pride Collision, Batenhorst says that the shop provides constant reminders of exactly how each repair should and is expected to be done. The shop hangs up all of its SOPs and provides visual aids, including process boards, throughout each step of the repair process. In addition to photos, Batenhorst says there are physical examples of what is expected. There are panels, pieces of steel and other various vehicle components throughout the shop that show both a poor example and an example of what is expected by Pride Collision.
Lead by Example
As Batenhorst mentioned in the beginning, the decision to make the switch to PCEs is challenging, but ifit starts with you and with an open mind, it can make your shop a better place. Batenhorst says the leaders within MSOs need to keep an open mind and be willing to learn. Employees will see that and will hold themselves to that same level.
About the Author
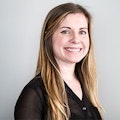