Thinkstock
According to Armando Arvizu, general manager of Service King in Tolleson, Ariz., the biggest problem for collision repairers is a lack of communication in the shop. Arvizu describes it as a snowball effect. If a customer relays something to the estimator and the estimator doesn’t communicate that effectively to the technician, there’s no way that the repair will be done according to the customer’s satisfaction.
Arvizu says that the reason communication is so difficult in this industry is because every repair is different. On a typical factory assembly line, people can get into a groove and create a standard set of rules. In the collision repair business, almost every situation is unique—which is why communication is so important.
Service King is working to eliminate miscommunication by bringing technicians into the communication process. Currently, Service King is beta testing a mobile application that will allow the front office and technicians to communicate in real time. The app should be available sometime in the first half of 2017 but shop operators do not have to wait until then to improve communication. According to Arvizu, there are a couple of different strategies that every shop can implement to improve communication.
Don’t be Afraid of Technology
Arvizu encourages shops to use all avenues of technology. From texting to email, there are so many ways to increase communicate in the shop. Arvizu says that, at facility he manages, emails are constantly being sent back and forth, and his team makes it a rule that nothing can happen before there is communication. This is important not only to the shop in Tolleson, but the entire Service King organization. According to Derek Kramer, CIO of Service King, the company has had long-standing use of technology and is building on it by reaching the technicians.
“With technology, one of the things that we noticed was absent was the technician population,” Kramer says. “That’s over half of the population. That’s a missed opportunity.”
With the app Service King is readying for launch, technicians will be able to send repair status updates and let the front office know when a vehicle is ready for its next step. The app has email access, calendars, access to repair orders, the components of the repair, a way to take photos of the repair and notifications.Through the app, technicians also will be able to access methods of instruction, view KPIs and see how their shop compares to other shops.
Arvizu says that one of the most inefficient points in a day is when a technician is not in a stall. If a technician is leaving his or her stall to track someone down to communicate something about the repair, work is not being done. By using technology, a tech can send a text to the front office without ever leaving the stall. Whether it’s sending a simple text message, downloading an app, or using a visual cue, there are a number of different ways technicians can communicate with the front office without ever having to leave his or her stall.
Increase Face-to-Face Communication
Using technology isn’t enough. Arvizu says that his shop has multiple production meetings per day. He says that the meetings do not have to last very long, but staying in constant communication is a great way to make sure that everyone is on the same page. Arvizu says that his shop usually has between three and four check-ins per day.
Keep a Hard Copy
Technology is great—but sometimes it fails. That’s why Arvizu says it’s important to have a separate process for communicating what’s going on with vehicle repairs beyond technology. The Tolleson shop uses Quality Assurance (QA) cards throughout the repair process. When a customer drops his or her car off, that car is automatically given a QA card that follows the vehicle through every stage of the repair process. The cards have room for all the information that anyone in the shop will need, including a spot for special customer requests and even a place to show where customers were sitting at the time of the accident. Once the QA card is filled out, it begins moving with the vehicle. At every step of the repair process, a staff member needs to sign-off on the car, indicating that they’ve done everything that was needed. The card (and the vehicle) cannot move on before it has been initiated.
Use Visual Cues
Arvizu says that visual cues are another great way to keep everyone in the shop on the same page when it comes to a vehicle’s repair. An example of a visual cue that Service King uses is the way it sets up its parking. Arvizu explains that his shop has defined parking for every step of the vehicle repair process. Drop-off vehicles are left in the front before they move along. There are designated spots throughout the shop for the various steps of the repair process including teardown, waiting for parts, paint line, and awaiting reassembly. By using these designated spots, anyone can walk through the shop at any time and see exactly where a vehicle is in the repair process.
Using parking spots isn’t the only visual cue that a shop can use. Arvizu says that he’s seen a number of different methods utilized; it’s just important to find one that works for your own shop. Arvizu says he’s worked at shops that use a color-coded chart where moving a vehicle to green means it’s “ready to go” to the next step of the repair process. A large chart in the front, a map where vehicles can be moved to various stages in the repair process, or color-coded folders that depict a step in the process are other examples of visual cues that work.
About the Author
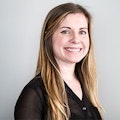