AWARDS NOMINEE JOSEPH MAGGARD OWNER JOE’S COLLISION REPAIR LONDON, KY
Earlier in his career, bottlenecks were the bane of Joseph Maggard’s existence. These days, however, he largely avoids them, as the owner of Joe’s Collision Repair, in London, Ky.
“Bottlenecks come with a price to pay: the person that runs the place has to stay late,” Maggard says with a laugh. “So, you try to eliminate them from happening, unless you don’t like going home.”
Working efficiently is a must when you run a shop with a small staff like Maggard, a veteran
of three decades working in collision repair. He’s the only full-time painter at the southeast Kentucky shop, which has four total employees and does approximately $40,000 per month in gross sales.
“One time I worked in a shop where it was like everybody’s goal was to go against the next guy,” Maggard says. “That creates a bad problem. You need everybody on the same page. If we’re fixing a spot the size of a quarter, don’t make a primer spot 8 inches around just for that little spot. … You need everyone looking ahead at jobs.”
Maggard, who has won awards for his work on restored vehicles like 1956 Chevrolets, has developed a few proven methods for sidestepping bottlenecks at his shop. Here’s his advice for avoiding shop floor constraints.
Schedule with your head, not heart.
At Maggard’s shop, he tries to schedule repairs in a manner that provides a consistent flow of work throughout his facility, and that also provides his staff with at least a bit of wiggle room.
“You don’t want to schedule more than you think you can handle,” the shop owner says. “Because, you might think you’ve got yourself a balanced schedule for the week, but lots of times there will be two more people that come in, wanting repairs done. … And, when you’re a shop that does warranty work for dealerships, drop-offs sometimes come in unexpected. So, always leave a little bit of room so you can adjust the workload.”
At his 5,000-square-foot Kentucky facility, Maggard typically schedules in a manner that allows 3–5 days per vehicle. He also schedules in a manner that rarely leaves the vehicles on site untouched for a full day.
“That way,” he explains, “nobody feels like they’re being put to the side. You shouldn’t make any customer feel like they’re playing second fiddle. Everybody should think, ‘My car’s being worked on first.”
Maintain constant communication.
Over the course of his career, Maggard has learned the importance of doing repair work right the first time. As a result, he takes several steps to ensure that his staff can avoid costly delays. For example, he often double orders parts if he fears there’s a chance a hood or fender might come in incorrectly, and he instructs his staff to have parts prepped in advance of scheduled repairs.
He’s also an ardent believer in making sure his staff gets a clear explanation of what’s expected of them for each repair, via thorough worksheets, estimates and dry-erase boards. For example, his instructions for his part-time painter typically note what a vehicle requires with regard to mix of paint, clear, and which vehicles need to be in the paint line for the day.
Maggard stresses the importance of having his staff members maintain an open line of communication during the repair process.
“The worst thing you can do is have a vehicle that you think is ready, taped up, and in the booth,” he says, “and you find out you’ve got to go back and re-do stuff like sanding edges.”
Lay down the law.
These days, the root of many body shop constraints is having a staff member who’s addicted to their cell phone, Maggard says. And, because that makes for occasional battles at his facility, the shop owner doesn’t hesitate to send an eye-opening message on occasion.
Maggard will occasionally send an employee home for the day if they’re causing delays because they just can’t pull themselves away from social media or YouTube.
“That’s how you get bottlenecks, is having guys not staying focused or staying busy, because they’re watching videos,” Maggard says. “One time I counted an (employee) stopping work 39 times in a little over an hour to get back on the phone, texting.”
When an employee causes bottlenecks due to carelessness like that, Maggard feels shop owners need to be authoritative. He even fired one employee in recent years, due to chronic smartphone use on the shop floor.
Frequent cell phone use, Maggard says, “is the worst workforce problem I see right now.”
About the Author
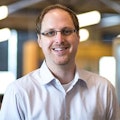