Dale Soos has tested automotive lifts for nearly a quarter century. Because of his work, he takes OSHA’s general duty clause to heart.
That clause, Soos notes, requires furnishing a safe working environment for employees.
“And a planned maintenance program,” he says, “is the best security for shop owners to keep employees safe for now and for the future.”
And take it from Soos, a senior project engineer with the Automotive Lift Institute: vehicle lifts can, and do, break down over time, making periodic inspections and maintenance imperative.
“The majority of lifts are made out of steel, which can corrode,” Soos notes. They’re “made of the same steel as automotive bodies—they rot from the corrosion, the rust.”
An American National Standards Institute (ANSI) national regulation covers lift inspections and requires that every installed vehicle lift be inspected at least once per year. But that’s not enough, Soos says. Body shop employees need to be vigilant with regard to checking lifts continuously.
Otherwise, issues can arise with lift equipment like hydraulic hoses that can leave shops susceptible to OSHA citations or violations of city codes.
“As you become familiar with any piece of equipment,” Soos notes, “you become complacent, as you rely on that product to do what it’s supposed to do, day in and day out.” And complacency, the engineer notes, can lead to workplace injuries involving lifts. For evidence of that fact, type the term “vehicle lift injury” into an Internet search engine and note the thousands of recent incidents—including deaths—involving that key piece of body shop equipment.
Fortunately, such unfortunate workplace incidents can largely be avoided if body shops iron out clearly defined procedures for inspecting and maintaining their lifts—steps like those indicated below.
Purchase a certified lift.
Soos, who tested his first automotive lift in 1995, suggests that shop owners do their homework up front before purchasing a lift. If they don’t heed that advice, shop operators open themselves up to potentially being liable in the case of a workplace injury.
“With a certified automotive lift,” Soos explains, “you know that it was designed correctly by a duly represented engineering staff, and that there are drawings and calculations that back up the design and the strength factors. If [shop owners] purchase a certified automotive lift that’s a great start to the safety equation. And, if they don’t, then you have no idea of the history of a particular product.”
Utilize qualified inspectors.
In Soos’ experience, certified lift inspectors leave no stone unturned when examining lifts. Not only does a certified inspector typically apply a serialized, dated and signed label to each lift that passes an inspection—making it clear to all when a lift was last inspected—but their exhaustive knowledge of lifts tends to provide peace of mind to all involved, as well.
After all, Soos notes, before certified inspectors can even step foot on a shop floor, they must pass written examinations, practical experience testing, and have a written quality system.
“They also have to sign a code of ethics,” he adds, in reference to qualified lift inspectors, “saying, ‘I’m taking responsibility for the safety of this product and, today, as I perform this inspection, it is safe for continued use."
Keep written documentation.
Shop staff would be well-advised to keep notes of every inspection that’s performed on their lifts.
Such documentation can ease any shop safety concerns expressed by insurers, OSHA, or corporate health and safety directors, Soos says. Otherwise, businesses like body shops run the risk of being fined several thousands of dollars by organizations like OSHA if they can’t prove that an annual lift inspection was conducted by a qualified lift inspector, for example.
Thoroughly train lift operators.
Established ALOIM (automotive lift operation inspection and maintenance) standards dictate that every automotive lift instructional package includes various elements like a lifting points guide that identifies where vehicles are to be picked up, and a safety tips card.
In Soos’ view, training of a shop’s lift operators must include an exhaustive review of such equipment manufacturer instructions.
“This is probably the biggest element that’s misunderstood,” he says. “The training of a lift operator isn’t a two-minute, ‘Hey, you press this button and it goes up’ type of thing.
“When OSHA’s giving out citations, they’re [largely] based on lack of operator training. … You know, it’s not simply purchase a product, install it, and forget about it.”
Implement a maintenance program.
Similar to how vehicles need to have their tires rotated every 5,000 miles, or their transmission fluid changed every 50,000 miles, automotive lifts require meticulous—and fairly frequent—maintenance. For example, hydraulic lifts require periodic filter or fluid changes, as the manufacturer’s instructions dictate.
“And one thing that most people don’t think about as a replacement item are the hydraulic hoses; they’re susceptible to fatigue by age," Soos notes.
Do daily examinations.
The ALI recommends that shop employees regularly check lifts and report any irregularities or concerns to their supervisors. Items that should be addressed daily include: a check for any corrosion, cracks, or leaks, or low fluid levels, and observance of any unusual noises. If those checks aren’t done daily, lift maintenance can become unwieldy, in Soos’ experience.
That’s why he hates to hear shop workers gripe about being forced to perform daily walkaround checks of their workplaces’ lifts.
“It’s frustrating to hear that when it’s something that can easily be performed in 3–5 minutes,” Soos says.
“What do you see the flight crew do before a plane leaves the ground? You see them do a walkaround of the aircraft,” he says. “Everything that has a safety implication, like an aircraft, any time that crews come on shift, they’re checking all their equipment to make sure that it’s in tip-top condition.”
About the Author
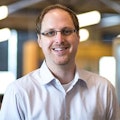