One element that every team needs is trust. Businesses are often compared to football teams. And if you think about how teams are set up within the shop, that analogy works, too. Think about it: The A-tech is the quarterback. One thing about quarterbacks and their teams is that trust has to go both ways. If I have my team in front of me to protect me, I can face the other way on the field. They’ll protect me. That’s the secret to my success.
As I said in my last column, we started out with one team that was the entire shop, until we outgrew that set-up (it grew to nearly 20 people) and moved to six-person teams. That way, everyone was forced to perform to the best of their abilities because underperformers couldn’t fade into the background.
The biggest downfall is you have to have the right mix of techs: A-, B- and C-techs. The reason is that all A-techs can fix a dent quickly but they might struggle with R&I because they’re older. That’s why you need that right mix of people.
On a five-person team, they all hold each other accountable. That’s a lot of the reason why those smaller teams are better. The A-tech usually acts as that coach and holds everyone accountable. If someone comes in late, he’ll tell him or her, “This is unacceptable, stop coming in late.” Selfishly, it’s super nice for me because my early days used to be watching who showed up at 8:05 a.m. Now, they decide the time they start in the mornings. They might know they need their paint prepper to come in at 9 a.m., versus the rest of the team. I don’t know how they figure it out and frankly, I don’t care. It took the petty management stuff away from me and the hiring managers and put it on the team to figure out how to produce the hours they need.
When we bring someone on, each person has their own team lead that’s appointed by them. There are the guys that want to be involved and those who don’t. When we hire someone on, it’s always a trial basis for two weeks. The company will pay for that employee when the team tries them out and makes sure they’re a good fit. They’re going to go with one of our techs who is good at training and work side by side with them.
An A-tech is the most difficult to hire, so we’ve taken the approach of not hiring them. In fact, we’ve made it a company goal of only hiring someone who’s never worked at another body shop. We’re working as a 20 Group to line things up to create an apprenticeship program. We’re not there yet, but I’d have to have a good feeling about him to hire him from outside. Instead, we hire at a C-tech level and train them to become an A-tech.
People know that they have the opportunity to grow. We have tons and tons of work, so everyone has the opportunity to move up. For C-techs, their No. 1 responsibility is to get to the B-tech level. For B-techs, they’re responsible for disassembly, blueprinting and reassembly. A-techs also tend to be really good at that and can fill in as needed, but their times might not be good enough.
Obviously, it takes years to go from a B-tech to an A-tech. Typically C-techs move up very quickly, so we may have a larger mix of B-techs on the team or move B- and C-techs around within the teams. However, the beauty of teams is they’re able to feed each other very well. The A-techs are doing structural repair or mud work, the B-techs are doing disassembly and reassembly and the C-techs are learning and helping. Generally, the A-techs are going to stay in structural repair and the B- and C-techs are going to bounce back and forth, but sometimes you have them all in one area. They may all be reassembling a car if that car needs to go home at some point that day.
Really, it all depends on the team, and I let them make that call, for the most part. Their No. 1 thing is that you have to have whoever is best at something do it most of the time—especially during crunch time. It’s just like with the Super Bowl; during slower times or extra time, they can learn and do other things that they’re not the best at. But when it’s go time, the person who is best at welding needs to do that to benefit their time.
About the Author
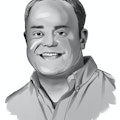