SHOP: Nadalin Auto Body
LOCATION: Washington, Pa.
OWNER: Norm Nadalin
SIZE: 6,600 square feet
STAFF: 6 (3 body techs, 1 teardown tech, 1 painter, and 1 helper)
AVERAGE CAR COUNT: 13-15 per week
ANNUAL REVENUE: $1.8 million
THE INSPIRATION: Norm Nadalin, owner of Nadalin Auto Body in Washington, Pa., has one of his own mistakes to thank for the inspiration behind his efficient shop. Nadalin’s shop runs on a key system—when a car is checked in, the key is tagged and assigned to a technician. Once the job is done, the technician informs Nadalin that the car needs to be moved (at Nadalin Auto Body, technicians don’t move cars—if they’re moving cars then they are not working on cars, making the shop less efficient, according to Nadalin). Once the car is moved, the process begins again.
One morning around 9:30, one of Nadalin’s bodymen told him that his car was ready to be moved. When Nadalin circled back around the shop at the end of the day, he noticed that the car was still there. He had forgotten to move it. “I’ve got to come up with a better system than them talking to me,” Nadalin thought.
Nadalin Auto Body already had a light system to show when the bathroom was in use (red meant occupied). Nadalin figured that if it worked for the bathrooms, why not make it work for the rest of the shop? So, when an electrician was in doing some work for the shop, Nadalin had him install a light system for two of his stalls.
WHAT IT DOES: Two of the bays (soon to be three) have a fourcolored light system mounted on top of them for everyone to see. The lights, which are extremely bright, indicate to the rest of the shop the status of the technician’s current job. The tech just presses a button that correlates with his needs, and someone will come around to answer the request. The light remains on until the request has been answered.
A green light means everything is running smoothly. If the technician switches his light to blue, it means he needs something from the painter. A red light means that there’s a parts problem and that the person in charge of parts is needed. The yellow light alerts Nadalin that the tech is almost finished with the job and to get the next job lined up.
“They’re constantly saying, ‘Hey, I need something’ without ever having to say a word,” says Nadalin.
HOW IT’S MADE: Light boxes were purchased at Lowe’s and mounted on top of each stall. The electrician then wired the boxes to the fuse box so that when the technician flips the appropriate switch, the color that they need lights up.
THE COST: Nadalin paid about $100 per light box set. Since the electrician was already doing work in the shop, the rewiring was added to the cost of the ongoing job. Nadalin says if you’re able to do the wiring yourself, the cost is only as much as the light box. However, if you need to hire an electrician it could cost closer to $400.
THE ROI: Just by changing certain processes, Nadalin estimates that the shop has doubled its gross sales since opening in 2000. The light system, which began generating an ROI immediately, brings in 1-2 additional jobs per week by allowing cars to move through the process more efficiently. The technicians are able to work more because they are not wasting their time walking back and forth.
About the Author
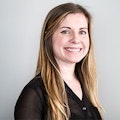