SHOP: Premier Autobody & Frame LOCATION: Santa Clarita, Calif. OWNER: Frank J. Pinto SIZE: 7,500 square feet STAFF: 7 AVERAGE MONTHLY CAR COUNT: 43 ANNUAL REVENUE: $1 million
Tracing the Shop’s History
Frank Pinto Sr. had been in the industry since he was 18 years old and worked at a General Motors dealership for almost 30 years. In 1987, he and his wife decided to open Premier Autobody & Frame, located in Santa Clarita, Calif.
Frank Pinto Sr. and his wife came up with the name and logo for the shop. Frank Pinto Jr., now the owner, remembers his parents went through several names before coming up with Premier Autobody. His parents purposefully chose to make “autobody” in the shop’s name one word. Pinto Jr. remembers his parents tossing around other names for the shop before deciding on Premier Autobody. Although he’s not entirely sure why his parents picked the name, Pinto Jr. is sure he won’t be changing it.
The shop is also big on maintaining its family culture; Pinto Sr.’s other children have worked in the shop and his wife holds an administrative position.
Shop Floor Refresh
After Frank Pinto Sr. retired almost 15 years ago, his son, Frank Pinto Jr., took the helm and started managing the shop in 1991. Keeping efficiency top of mind, Pinto reconfigured the shop floor and rearranged the location of the shop’s equipment.
All 10 of the shop’s bays are fully operational and he’s designated areas on the shop floor for body work, frame work and mechanical work. Premier Autobody & Frame’s shop floor is different than other collision repair facilities, as there are five stations that make up the shop floor. Once Pinto Jr. took over the business, he worked on designating these five stations into departments, including the body department, paint department and suspension department, which also doubles as a stock room.
Pinto Jr. also made some significant additions to the shop, which included adding hoists to aid in the vehicle inspection process, an A/C service machine, a resistance spot welder and a frame measuring system.
Staying Organized
Over the past 6-7 months, Pinto Jr. has integrated a system to better track the repair process and help technicians stay organized.
He added bins right outside of the shop’s front office, so that technicians and staff members alike can place repair orders and cut down on time spent going in and out of the shop.
There are three key bins: one for supplements, one marked as “Waiting 4 Parts/ Problems” and one for repairs that are ready for quality control.
Connection to the Community
As another way to help the shop stand out, the Pintos reached out to a local artist to paint a mural on the back of the building.
The mural is a snapshot of what the neighborhood looks like and it has been a staple for the last 15-20 years. Since it’s on the back of the building, which faces the road highway, drivers and potential customers can recognize the shop.
Over the years, the mural has been updated to reflect minor changes in the area.
About the Author
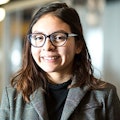