Let’s start with a hypothetical: Imagine a school bus going down the road with 60 children on it. Better yet, imagine it being your child’s school bus. Sure, nothing looks different about it; it’s just a typical yellow school bus.
“But let’s say it was in an accident a few months ago, maybe a large accident,” Mike Anderson says. “You would probably like to think the same repair information, repair processes, procedures—you’d think that all of that would be the same to repair that school bus as it would be for any other vehicle on the road, right? It’s just not true.”
Anderson, a longtime shop operator and industry consultant who has facilitated a 20 Group of heavy-duty truck (HDT) repairers for years, says that if you’re reading this, you likely already know this is an issue. Simply put: The data, resources and information needed to repair a heavy-duty vehicle—be it a school bus, ambulance or big rig—simply isn’t readily available to you.
“It’s a serious, serious issue,” Anderson says.
So, what’s the solution? It starts with an acknowledgement of the issue by the greater industry, and pushes forward when key stakeholders get involved.
Let’s break it down.
The Issue
The “Right to Repair” bill passed through the Massachusetts legislature in 2013, only later to be adopted into a memorandum of understanding by automakers and industry organizations the following year to create a national standard of accessibility to repair information and diagnostic abilities. One exception to this agreement, though, was the heavy-duty vehicle segment.
“It wasn’t included in the legislation or agreement, and because of that, nothing has ever changed,” Anderson says. “So, today, these shops have no repair procedures. They just aren’t available to them.”
And as the greater automotive industry has seen an influx in advanced computer systems and structural materials, so too has this segment. Add in the fact that many of these vehicles have critical functions—from hauling or pulling immense loads to navigating traffic to arrive at the scene of an emergency—and the thought is frightening.
The Current State
Ask Anderson how HDT shop operators have gotten by this long, and he’ll start rattling off names—each a prime example of a repairer who goes to great lengths to research and understand the vehicles his team works on and how to fix them properly.
“But it’s just too difficult,” Anderson says. “There are so many great people in this segment who do really exceptional work, but they have to work twice as hard as any other [segment].”
The Solution
Here’s the simple answer—get automakers to share the repair procedures with independent shops. That’s not quite as simple in the real world, though.
“What we need to do is get people behind this issues, and personally, I think this starts with I-CAR,” Anderson says. “They are the ones that can bring a lot of leadership to this charge and get others involved. The fact is that it’s not an issue at the forefront for most in this industry, and that needs to change.”
For you, the shop operator fixing these vehicles, Anderson suggests reaching out to others with similar business models. Combine resources, share information, fight this cause together. Work with your vendors, reach out to automakers, and get in touch with I-CAR. Make your needs known. Even call Anderson.
“We just have to do this together,” he says. “Sitting on an island wishing for it won’t get it done. I’m here, I-CAR is here, we’re all here. Let’s get this done. It’s 2017 and the fact that this is an issue is embarrassing. We need to fix this now.”
About the Author
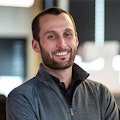
Bryce Evans
Bryce Evans is the former vice president of content at 10 Missions Media, overseeing an award-winning team that produces FenderBender, Ratchet+Wrench and NOLN.