I was called to a shop to do a simple headlight calibration procedure that I have done many times before. The vehicle in question was a 2016 Audi A8 Quattro (Figure 1) that was recently involved in a front-end collision and suffered damaged to the left front of the vehicle. The most expensive cost of the claim was the left headlight assembly, which had a cracked housing from the accident. This vehicle used an advanced “Metrix Beam” system and luckily for the parties involved the external control modules were usable because they were not damaged or exposed to the elements of nature while sitting in the yard waiting for repairs. Someone was smart enough to plastic wrap the front of the vehicle to protect the electronics of the vehicle.
I have seen many headlight modules destroyed from water intrusion and not necessarily from the accident. These modules are sometimes located at the underside of the headlight and once the headlight housing is cracked it is no longer sealed. When cars are towed into a body shop and left outside in the rain, water will enter the headlight assembly and always settle at the bottom of the headlight and corrode and damage the modules over time. Once the vehicle is ready to be repaired and pulled from its storage area, it is a little too late. This only increases the expense of the claim and in some cases puts the vehicle closer to a total loss.
There are some towing companies I have seen that will actually charge to plastic wrap part of the vehicle to protect the vehicle from the elements of nature and just add the service to their tow bill. I think it is an excellent service, especially if they know that it is being towed to a shop where it most likely will be sitting outside. I don’t think most insurance companies would question the cost of wrapping a vehicle because it is to their benefit. The cost of exterior lighting and electronic components has risen so sharply that a plastic wrap fee overshadows any questions of its charge.
The headlights used on today’s cars can get very costly due to the amount of electronic control modules used internally. With the onset of LED technology, there are multiple LED modules needed to control their operation. Some headlights will combine these with high-intensity discharge lamps, which will require a separate module to control them. If these control modules are replaced, they may not always be plug and play. Manufacturers may make the headlight or LED lamp inoperative to alert you that programming is needed, but this only confuses a repair tech in thinking that there is a fuse or wiring issue with the vehicle. Reprogramming of these modules will require access to a factory website to download specific files into the headlight modules so they can properly function. Then after programming the lights, there are post procedures such as adapting and calibrating the headlight for proper aiming.
The shop did not replace the modules, but simply swapped them into the new headlight and plugged the new headlight into the vehicle. The headlight worked fine with no problems, but there was just an error message on the instrument cluster (Figure 2). I proceeded to place my scan tool on the vehicle and do a complete scan of the system prior to calibrating the headlights just to make sure there were no underlying issues with the headlight system. I was surprised to see a Code C116601 stored as an active code in the main headlight control module (Figure 3). This code referred to a cooling fan internal to the new headlight assembly. Could this headlight be defective? I verified a wiring diagram to see if there was an external wiring issue that feed the headlight fan (Figure 4). You could see that the fan was directly controlled by the LED #1 Module.
There were actually four modules in this headlight assembly. One was for the Metrix Beam that is mounted externally on the headlight housing with large cooling fins because the Metrix Beam Power Module controls up to 12 individual LEDs that provide light that is brighter than xenon lighting and these modules run very hot. The other three were for separate LED lamps used in the headlight’s assembly for signal lights and daytime running lights and were smaller in size with only one being installed on the exterior housing. The shop had no choice but to pull the headlight for further inspection of the cooling fan.
Once the headlight was pulled from the vehicle, you could see the large Metrix Beam Control Module mounted on the back side of the headlight assembly and a smaller LED module mounted on the inner side (Figure 5). These were the only modules that were transferred from the original headlight, but the other two LED modules were within the headlight and came with the headlight assembly. We did not want to avoid warrantee on a new headlight but we had no choice, so we carefully opened up the headlight back cover mount under the Metrix Beam Power Module for further inspection (Figure 6). We opened up the old headlight as well so we could compare the headlights for anything that was different.
We noticed that the old headlight had a fan mounted directly below the removed back cover (Figure 7), but the new headlight assembly had a fan missing in action. There was a large void where the fan should have been. When we called the dealer, they told us that the new headlight was not supplied with a headlight fan motor and it was sold separately. We had to remove the fan from the old headlight (Figure 8) and place it into the new headlight assembly. If the body shop had thrown away any parts from this car it could have held up the job. This is one reason why it is critical to hold onto ALL parts associated with a vehicle until the repair job is completed and out the door because you never know when you may need to dig back into the pile. This avoids any dumpster diving on your part.
We next proceeded to put the headlight assembly back together and into the vehicle. I then calibrated the headlight control system and cleared out the entire vehicle of any error codes stored in memory. All the error messages on the dash were extinguished and there were no more codes in history. I just can’t believe that a manufacturer would leave out a $20-$30 cooling fan on a very expensive headlight that must run in the $2,000-$3,000 range. There should have been some type of warning sticker on the headlight cover to alert the installer that the fan was not installed directly under the removable cover. Luckily the vehicle never left the shop with the error light on the dash, and the shop owner addressed the concern immediately without releasing the car to the owner to satisfy the cycle time of repairs. These headlights run very hot with all the electrical demands within them and I could easily see an internal module prematurely failing from excessive heat load from a missing cooling fan. I hope this article enhances what you know and didn’t know about headlight systems on the market today.
About the Author
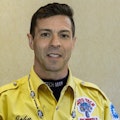
John Anello
Owner and operator of Auto Tech on Wheels
John Anello is the owner and operator of Auto Tech on Wheels, established in 1991 in northern New Jersey. He provides technical assistance and remote reprogramming with 21 factory PC-based scan tools. Driven by a passion for cars, John's business now services roughly 1,700 shops.