With vehicle innovations like ABS, airbags and crush zones, OEMs continue to meet — and surpass — demands for more safe, high-tech vehicles. Consequently, when a high-tech car is involved in a collision, vehicle design must be taken into consideration during the repair process. “Twenty years ago, if a car was involved in an accident, repairing it was a pretty basic thing,” says Randy Gard, president and CEO of Chief Automotive Technologies. “In today’s environment with crush caps, crush zones, accelerometers that measure deceleration G-forces that deploy airbags and that type of thing, shops are going to have to fix a vehicle the way the OEM-recommended repair procedure says.” There are two very good reasons for repairers to embrace design-based repair — customer safety and shop liability — and those two factors create opportunities for shops as the industry evolves. “There’s more and more coming,” Gard explains. “Volvo’s technology can sense an impending collision and automatically applies the vehicle’s brakes. Then you’ve got things like headlights that turn as the vehicle turns. It’s a heck of a revenue opportunity for body shops because these are parts that need replaced and if they’ve got technicians that have some level of training, they can replace these parts.” Gard says shops need the tools to validate that these different components work or don’t work so they can identify and replace them. “If a body shop knows an accelerometer doesn’t work, they know they can buy one and put a new one on and get paid for that.” Design-based repairing makes good business sense, and Gard is no stranger to how businesses work. He’s been at Chief Automotive Technologies for six years now, and sits on the Board of the Equipment and Tool Institute (ETI). Before coming to Chief he worked in the Engine Components Division of Eaton Corporation. His background even goes a bit beyond the automotive industry. “I’ve been in the heavy-duty equipment business, I’ve been in the gaming business making slot machines and I’ve been in the ammunition business oddly enough. I’ve been in a lot of different industries but automotive is truly where my passion is. I’m kind of a car nut and always have been.” It’s no surprise that Gard would have an interest in something like design-based auto repairs, since he’s loved cars his entire life. He can still remember the day he knew he would be around cars for a long time. “I realized I was a car nut the first time my brother took me drag racing. My older brother bought a ’65 Olds 442. He was 17 and I was 14 years old, we were racing some guy and I was scared to death. It was so exhilarating that I thought, ‘Man, I gotta get one of these things.’ ” Gard knows from firsthand experience the importance of spreading the word about design-based repair awareness at the shop level. Accountability and liability are going to become larger and larger issues for repair shops, and those that are set up to best handle the repair situation are going to be the most successful. As part of Gard’s work he’s often visiting shops and talking to technicians. In one shop Gard observed a technician working on a Dodge Ram pickup with a kink in the crush zone and he was just going to pull it back, measure and put the vehicle back together. “I said, ‘How do you know that the accelerometers work? How do you know that the airbags are going to deploy? How do you know that that crush zone is going to absorb energy at the same rate it was designed to?’ He said, ‘Well I don’t’, but it’s a good fix. It drives good, it aligns good and it looks good.’ But when you say design-based repairs, when the car is repaired and returned to the customer, there has to be a level of confidence that that vehicle's systems will perform the way they were designed.” The industry is still in a state of flux in the area of design-based repair, and many shops today still make most of their money on painting and sheet metal. But those days are fading away, and successful shops of tomorrow will be the ones that are proactive today. “I’ve seen some very proactive shops where they have service bays with diagnostic tools and they’re okay with aligning the car. They’re okay with changing out wire harnesses and other similar types of repairs because, one, they make money on the parts, and two, they don’t lose control of the vehicle by outsourcing it out to a local dealer or service shop. So their throughput time is better.” Gard believes that as shops start to understand design-based repairs, the way a body shop is managed is going to focus on training and education. Shops are also going to need to invest in the proper equipment. Many OEMs now have specific procedures and equipment requirements for repairing their vehicles, and this trend will continue. Equipment manufacturers will develop more and more equipment with input from OEMs. “Repairers are going to struggle with education, they’re going to struggle with tools to do the job and some are going to ask, ‘Why do I have to fix it the OEM way? This is my business — I do it my way.’ That’s really not the issue; the issue is you just want to fix it right.” Design-based repair not only creates opportunities for body shops, it creates opportunities for suppliers as well. Gard sees those opportunities and his company is currently working on several new products to address the issue. And while there are opportunities, Gard says that a big challenge repairers must face is the number of totals. He says this is the biggest thing that has affected the industry in the last 10-15 years. But, he’s optimistic about changing that trend. “If you can repair the vehicle faster and better, and you can validate the repairs, maybe we can start to reverse the trend of higher percentages of totals.
|
About the Author
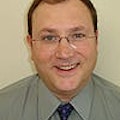