Raise your labor rate to make more money with fewer customers
Everyone who knows this industry understands that things are changing very rapidly. Everyone also understands that there is an extreme shortage of competent technicians. The problem with this is that the issues in our industry are creating increasing costs, and these costs must be dealt with. Let’s assume the shop owner goes through the processes and have examined the operation very carefully and eliminated any waste to keep costs down without affecting the service levels delivered. Management has also examined the level of productivity per person to ensure that this issue is addressed. Everything has been approached with thoroughness, but management comes to the only conclusion that increased costs are higher than expected, and they must be passed on through an increase in the shop’s labor rates.
Now management’s mind starts to play games. Management doesn’t sleep too well at night. Management starts to think, “If I increase my labor rates, I will lose my customers and suffer financially.” Consider this: if you are competent and your clients trust you, and you never let them down, why would they leave you over a labor rate increase?
Consider that it is time to slow down and do the math in your business. How many customers could you let go (or even fire) and send them over to the competition? There is a formula; follow the example below:
Shop Assumptions:
- the shop labor dollars sold last year was $350,292
- the shop labor rate is $80
- the shop is averaging 1.48 labor hours billed per repair order
- the shop’s gross profit earned from labor is 94.5 percent (labor dollar sales minus sublet labor equals labor dollar gross profit. Labor dollar gross profit divided by labor dollar sales equals labor gross profit percentage)
- the shop needs a 15 percent labor rate increase taking it up to $92 ($80 X 15%= $12)
1. The first step is to take the labor dollars sold and divide it by the current labor rate: $350,292 divided by $80 = 4,378.6 hours billed for the year
2. Take the hours billed for the year and divide it by 12, which gives you the average billed hours per month: 4,378.6 divided by 12 = 364.88 average billed hours per month
3. Gross Profit Margin percent on labor divided by gross profit margin percent on labor plus 15 percent minus 1 = the percentage reduction allowed in billed hours: 94.5% divided by 94.5% + 15% = 94.5% divided by 109.5% = .8630; .8630 - 1.0 = .1369% (expressed as minus 13.69%)
4. Average labor hours billed per month times percentage reduction allowed in billed hours equals actual number of reduced labor hours allowed: 364.88 X 13.69% = 49.95 hours
5. Average labor hours per month minus actual number of reduced labor hours allowed equals new average labor hours to be billed at new labor rate: 364.88 – 49.95 = 314.93 average monthly hours
PROOF: 364.88 X $80 = $29,190.40
In other words, we can bill out less hours at the new labor rate and still retain the same labor dollars coming into the shop as we had at the old rate.
6. Now the interesting part occurs. It is certainly not the intent to lose any customers, but there are some customers management would probably prefer went somewhere else; therefore, how many customers could the business afford to lose (or fire) after management raises the labor rates, without affecting the total labor dollars brought into the shop?
Actual number of reduced labor hours allowed divided by average labor hours billed per repair order equals number of customers that can be “fired:” 49.95 divided by 1.48 = 34 customers
It is most unlikely that the shop will lose 34 customers in a month over a $12 labor rate increase; however, if some are lost, or fired, that can be good too because it frees up valuable time that can be spent with “clients,” not “customers.” Time that allows you to “slow down” and get focused on the client’s needs, which in turn, allows the shop to service them very well, and increase total revenue substantially beyond the old labor rate revenue. All costs are now covered, and revenue growth begins, coupled with bottom line growth. With satisfied clients, the shop most likely gets “client” referrals, not “customer” referrals.
Many shop owners fear a labor rate increases, and yet if they would do the math, it could mean the difference from going to a financially stable shop providing good salaries for all, versus trying to run a stressed out cash strapped shop. Shop owners (management), too many times, can be the real enemy to a successful enterprise, not the technicians, not the client, just the person in the mirror who writes the check. Work out your numbers to ensure you are not the one holding your shop back from moving to the next level that it must get to if it is going to succeed over the next five years.
About the Author
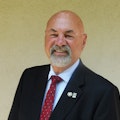
Bob Greenwood
Robert (Bob) Greenwood, AMAM (Accredited Master Automotive Manager) was the President and C.E.O. of Automotive Aftermarket E-Learning Centre Ltd. (AAEC). AAEC is a company focused on providing Business Management Resources and Development for the Independent Sector of the aftermarket industry utilizing the Internet environment. AAEC content and technology is recognized as part of the curriculum of the Fixed Operations Diploma and the Aftermarket Degree courses taken at the Automotive Business School of Canada in Georgian College located in Barrie, Ontario, Canada. This school is the leader and only college in Canada that offers an automotive business education. AAEC is also recognized by the Automotive Management Institute (AMI), located in Colleyville, Texas USA, allowing 80 credits for successful completion of the AAEC E-Learning portion of the site towards the 120 credits required to obtain the reputable Accredited Automotive Manager (AAM) designation. The Automotive Management Institute’s Accredited Automotive Manager designation is the first business management accreditation exclusively for the automotive service professional. To date, AMI various programs have attracted more than 212,000 enrolments throughout North America.
Greenwood died on Sept. 9 in Surrey, British Columbia, Canada, from a heart attack. He was a regular contributor to Motor Age magazine and will be greatly missed. See some of his recent work here:
Where is your shop today: Do you have a career or job culture?
Part one of a three-part series looks at a sample policy manual for your team
How should you measure the real cost of running your business?
A few quick calculations can provide powerful insights into business productivity and profitability.
Shop of the future is becoming reality
Thousands of independent shops will disappear over the next few years, but those that survive will be great businesses. Let's look at what these shops will have done to remain successful.
See more of his articles below.