If you’ve ever watched a racecar driver climb from a flaming wreck and marveled at how lucky he or she was, know that much of that luck was by design. In addition to safety features built into the track and the car itself, everything that touches drivers is highly engineered to keep them in place, absorb impact forces and give them precious seconds of fire protection.
A driver’s safety equipment has come a long way in a relatively short time. When Mario Andretti started driving professionally, he wore a single lap belt, cotton overalls and an open-face helmet that wasn’t much more advanced than a 1960s-era football helmet. During testing two years ago, Andretti walked away from a crash after the car became airborne and flipped end-over-end at 200 mph. Had he been wearing anything other than modern equipment, the results would surely have been quite different.
In the beginning
Drivers’ safety equipment all starts with what’s referred to as the SFI. What we now know as the Specialty Equipment Market Association (SEMA) started out in 1963 as the Speed Equipment Manufacturer’s Association. Part of the early SEMA’s function was to develop performance specifications for racing equipment, and because the association included some important members of the racing equipment manufacturing community, many sanctioning bodies adopted those specs right away.
The specs program gained momentum quickly, and SEMA-spec components became required to get a car onto the track at more and more race events each year. This was and still is viewed as a good thing, and specifications development eventually became a stand-alone program within SEMA. It was called the SEMA Foundation Inc., or SFI for short.
Forty years later, SEMA is no longer devoted exclusively to performance equipment, and the specs program has been spun off as an independent body. Its name has officially been shortened to SFI Foundation Inc., but it’s still voluntarily funded and operated by its members, except for a small, paid managerial staff. The list of members includes many well-known names in the performance equipment industry, as well as sanctioning bodies like NASCAR, Indy Racing League (IRL), the National Hot Rod Association (NHRA) and some lesser-known sanctioning bodies like the National Tractor Pull Association, the American Power Boat Association and the Finnish Hot Rod Association. In all, 49 race sanctioning bodies are SFI members, and many, many more specify SFI-rated equipment in their rule books.
SFI specifications are applied to roll cages, bell housings, superchargers and their containment devices, as well as a wide variety of other items on the car. Personal safety items covered by SFI specs include driver suits, helmets, window nets, seat belts and other restraints and padding. Next time you see something that looks like a driver’s suit in the pits or on television, look for the SFI patch on the left sleeve or shoulder.
Where Nomex rules
The most important function of a driver’s suit is fire protection, so the SFI ratings for drivers’ suits are based on their thermal protective performance (TPP). In the presence of direct flame or radiant heat at 1,800 degrees Fahrenheit, TPP is a measure of the time it takes for a person wearing the suit to suffer a second-degree burn (blistering of the skin).
There are six different TPP ratings for drivers’ suits, with the minimum providing three seconds of protection and the maximum providing 40 seconds of protection. Different ratings are required for different types of racing. For instance, some classes in Sports Car Club of America (SCCA) racing require only single-layer driver suits with the minimum SFI rating of 3.2A/1, while NHRA Top Fuel drivers must wear suits with the maximum rating of 3.2A/20.
How the ratings are accomplished varies according to the suit’s manufacturer and the technologies they use, but layering and insulation are as important as the material’s ability to resist burning, especially for protecting against radiant heat. In some rule books, fire-resistant long underwear can be worn to increase the rating of a lower-rated suit.
Although it’s not the only one, the best-known and most commonly used material for drivers’ suits is Nomex, the brand name of a flame-resistant material created by DuPont™ in the 1970s. It’s also used for aircraft upholstery, and it can be formed into stiff sheets for insulation and other uses. In a driver’s suit, each layer of Nomex adds seconds to the TPP rating, and wearing Nomex underwear can multiply the rating further. The air gap between layers acts as insulation, and a somewhat loose-fitting suit is more effective. A side benefit of Nomex is its natural resistance to abrasion, which not only enhances protection in an emergency situation, but also prevents wear from constant contact with the seat belt and shoulder harness.
Driver fatigue plays a big role in safety, especially during longer races, so keeping a driver cool under all that fire-resistant clothing is important. Drivers can carry ice packs in the pockets of a vest worn under the suit, or in pockets built into the interior of the suit. For longer races, a cool suit is a better choice. It’s basically an undershirt with several yards of small-diameter tubing sewn to it. Using dry-break quick disconnect fittings, the tubes are connected to several feet of insulated hose leading to an ice chest mounted somewhere in the car. A small electric pump circulates water from the shirt’s tubes to a heat exchanger in the ice, sending chilled water back up to the tubes in the shirt.
The brain bucket
A driver’s helmet is one of the most highly engineered items in racing. Like all true helmets (as opposed to hard hats), the shell is made of advanced lightweight materials that fracture in just the right way to absorb impact energy. This allows the helmet to sacrifice itself to protect the head inside. Lining the shell is a layer of open-cell foam, such as Styrofoam, that absorbs energy, and its shape can help spread impact forces. Next is a layer of soft padding that is used to adjust the helmet’s fit. Some race sanctioning bodies also require the driver to wear a flame-resistant balaclava, or “head sock,” under the helmet.
In SFI competition-rated helmets, the inner lining is covered with material that must meet the same TPP specifications as a 3.2A/1 driver suit; all the other helmet materials will self-extinguish when no longer exposed to flame. There are specifications for impact performance, penetration protection and for a proper fit that prevents it from rolling off the head from back to front. SFI also has a motorsports rating for helmets, which is identical to the competition rating except for the fire resistant-lining specifications.
A helmet must maximize driver protection and still be comfortable. In just the last two years, attention has turned to the outside shape of the shell. In some open-cockpit cars, the driver is literally facing a 240-mph wind. The new shells are shaped to work with the aerodynamics of the car to prevent lifting and buffeting forces that distract and fatigue the driver. They also have inlet and exhaust air vents appropriate to the car’s aerodynamics.
Full-face helmets used in closed cars are often equipped for forced-ventilation with a hose fitting on the side of the chin bar. The hose brings in filtered fresh air supplied by a vent on the side of the car or by a blower. Sometimes that air is routed through the same ice chest used by the cool suit.
The clear shield on a full-face helmet is also an engineering challenge, particularly the hinge/latching mechanism. It must flip open easily for the driver but not for the wind, and it must be removable for easy replacement. The shield material is designed to protect the driver from projectiles as well as the wind. For open cockpits and motorcycle racing, the helmet can be fitted with “tear-offs” — layers of clear plastic stretched over the face shield that the driver can easily peel off with gloved hands, allowing the driver to “clean” the face shield.
Staying put in the vehicle
In oval racing, the driver’s neck muscles must support the weight of head and helmet against ongoing centrifugal forces. Some helmets have a threaded insert built into the shell, and a tether screwed into the insert is looped around the driver’s left arm or shoulder. Another device used in many forms of racing is a helmet support: a thick, flame-resistant collar that rests on the driver’s shoulders so the driver can rest his head by simply tilting just a bit.
One restraint that’s received a lot of attention recently is the HANS device. It was invented to limit forward motion of the head during a crash, thus preventing certain types of injuries. But it can also ease driver fatigue brought on by repeated side forces and heavy braking. It’s a hard plastic yoke that sits on a driver’s shoulders and is held in place by the shoulder harness. A collar extends up several inches behind the helmet, and a tether attached to each side of the helmet loops behind and attaches to the collar. The tether can slide sideways in the collar so the driver’s head can still turn side-to-side. However, the device limits the tilt of the driver’s head in all directions, particularly forward.
In a frontal crash without head restraints, the helmet’s “forehead” often contacts the steering wheel, causing the head to rotate upwards and jam the base of the skull against the neck. Though it was originally invented to prevent this one type of usually fatal injury, extensive testing of HANS restraints has demonstrated the probability of reduced injuries in crashes at any angle.
While many sanctioning bodies require use of the HANS device, it’s not the only head restraint. Off-road and other extreme types of racing utilize tethers attached to each side of the helmet and to both arms or to a harness worn like a jacket. Another type passes the tether through a loop of web attached to the back of the driver’s suit. These are meant to relieve fatigue and help the driver maintain control. While they will help limit head motion in a crash, they’re not as effective as a tether anchored to a collar that’s held in place by the driver’s shoulder harness.
Reducing the ‘third collision’
Along with helmets, seat belts were the first major advance in racing safety, and over the years they’ve been studied and improved almost as much as helmets. Today’s belts are made from a military grade (mil spec) nylon or polyester web. Just as steel is stronger than iron because it can bend, these materials are stronger because they can stretch.
In a crash, a driver’s body can exert thousands of pounds of force on the belts. The trick to reducing injury is to balance belt stretch with the need to hold the driver in place. Even a small amount of stretch helps to reduce what’s called “the third collision.” The first collision involves the vehicle, the second is the driver against the restraining device and the third causes injury to the driver’s internal organs.
The typical seat belt system is a five- or six-point harness that connects to the chassis in five or six places. All belts meet at a central quick-release in the driver’s lap. The lap belt holds the driver’s pelvis in place, and the two shoulder belts restrain the driver’s upper body. The remaining one or two belts extend down from the latch, sometimes right through the seat, to keep the lap belt low on the driver’s hips. This prevents the driver from “submarining” or sliding out from under the harness.
All the belts’ attachment point locations in the car are critical to the harness’ performance. In a proper belt installation, the driver’s body will stress all the belts evenly, distributing the energy of the second collision over the widest possible area. That’s also why the belts themselves are typically three inches wide.
In the wide-open cockpits of Midgets and Sprint Cars, many drivers wear restraints that prevent their arms from flailing outside the cockpit in a roll-over. They typically wrap around the driver’s forearms and attach to the driver’s harness quick-release latch. Most are padded and made of flame-resistant materials.
Time and exposure are the enemies of all belts. Sunlight, heat and the fumes present at most racetracks and garages can all attack the web material. A graph published by SFI shows the results of a belt left outside for 24 months. Its tensile strength was less than 20 percent of a new belt. SFI specifications and many race sanctioning bodies require belt replacement every two years. Most belt manufacturers will “re-web” a harness by installing new belts onto existing latches and other hardware.
Protecting the extremities
In some racecars, the pedals are so close together that a driver’s shoes must be little more than moccasins with hard soles. Most are made of leather or suede, but of course they have SFI ratings that match those of drivers’ suits, and Nomex socks are often worn under them. The shoes usually extend up the ankle enough so the driver’s suit can cover the tops. In some cars, the floor gets hot enough to require extra heat protection just to be able to drive the car. At least one company sells a quilted, strap-on heat shield that forms a cup around the back of the foot.
Flame-resistant clothing should not contain any elastic or other manmade materials that can melt. That means Nomex socks and underwear don’t fit or hold themselves in place the same way as the regular stuff. Without getting too deep into the subject, you can imagine how the clothing can bunch up, and why it takes time and concentration to get comfortable in a tight cockpit.
Gloves carry the same TPP ratings as driver’s suits, and while they may be multi-layered, some have leather sewn onto the palm to improve grip. It’s important that the leather is only sewn onto the palm, not wrapped around the hand, because high heat makes it shrink. Most drivers prefer the thinnest gloves they can get away with, not only for feeling the car’s feedback signals, but also for comfort in a hot environment.
Most of this equipment is expensive, and some of it must be replaced or officially inspected and recertified each year. But it’s an expense few racers complain about, because driver comfort is good for performance, and driver safety is priceless.
Some construction features of the car that protect a race driver in a crash have found their way into the cars we all drive on the street. We’re still a long way from being able to step out of even a 50-mph crash unscathed, but when the general public is ready to wear serious seat belts, it just might happen. Meanwhile, research continues at the racetrack.
About the Author
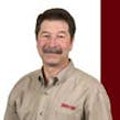