"Experts rank aluminum as one of the top options to meet new fuel economy standards," says Pat McNulty, an executive committee member of the auto and light truck group for the Aluminum Association, a trade association for producers of primary aluminum, recyclers and semi-fabricated aluminum products.
"Mass is the enemy when it comes to fuel economy," says McNulty, who also is director of the automotive market for Novelis Corporation, an aluminum rolling and recycling company. One of the most expeditious ways to reduce mass is to replace heavier materials, primarily steel, with lighter weight materials such as aluminum. "Direct material substitution is where manufacturers will see the biggest bang for the buck," says McNulty.With a density of .27 per cubic center, aluminum has about one-third the density of steel, says Peter Friedman, technology leader for Ford Motor Company. "But it's strength per pound approaches that of steel."
Aluminum comprises about 326 pounds, or 8.7 percent of the curb weight of the typical car sold in North America today, according to research and consulting firm Ducker Worldwide. That's nearly a fivefold increase since 1970, when aluminum comprised only 77 pounds, or 2 percent of curb weight.
The strong growth trend is expected to continue for the foreseeable future. Ducker expects aluminum to account for 9.6 percent of the average North American vehicle's weight by 2015 and 10.4 percent by 2020. The aluminum content in a few of today's vehicles – including the Honda Pilot, the Acura MDX and some the BMW X6 models – already exceeds 10 percent. (See related story "Research plots aluminum gains".)Initially aluminum found its way into parts of the vehicle that are fabricated using a casting process, such as engine blocks. For 2009, Ducker estimates that nearly 70 percent of engine blocks are made from aluminum and that engines comprise more than a third of the total aluminum used on the typical vehicle, measured in pounds.
Other areas where aluminum has made significant inroads are automotive knuckles, control arms and suspension links. Nearly half of vehicles made today have knuckles that contain aluminum, according to Ducker, while a third of current production vehicles have aluminum in their control arms or suspension links.
Using aluminum for parts that normally are made of sheet metal rather than castings can be a bit trickier, but automakers have devised some innovative solutions. The exceptionally large lift gate on the 2010 Lincoln MKT seven-passenger crossover vehicle, for example, uses lightweight magnesium castings in combination with sheet aluminum, making it 40 percent lighter than it would have been using traditional steel construction.
"One big casting can integrate many sheet parts to make one big functional part," Friedman says. "Magnesium is even less dense than aluminum and can be cast into very intricate shapes."
One reason aluminum wasn't used more extensively in the past is that it is more costly than steel – about three times the price on a per-pound basis, according to Friedman. "But, you'll use considerably less," he says. "On a closure system, you can save 40 to 50 percent in mass."
Manufacturers of high-performance vehicles traditionally were the ones most concerned about vehicle weight because a lighter vehicle has faster acceleration and improved handling. Buyers were willing to pay extra for enhanced performance. But as fuel economy standards become more stringent, even manufactures of more mainstream vehicles are able to justify the extra cost of aluminum manufacturing.
"A rule of thumb used in the industry is that a 10 percent savings in total vehicle weight represents a 3 percent savings in fuel economy, and it can go as high as 7 percent if you can do power train re-matching," says Friedman.
If a car model weighing 4,000 pounds has its weight reduced to 3,500, for example, the manufacturer should be able to downsize the engine. "There's also less unsprung mass," Friedman says. "You can change the springs and brake systems because the car is lighter."
The goal of improving fuel economy and efficiency is not just to conserve fuel, but also to reduce pollutants.
"Every kilogram reduction in weight can reduce CO2 emissions by nearly 20 kilograms," says Jeffrey Makarewicz, vice president of the materials engineering division for Toyota Motor Engineering & Manufacturing North America.
Increased use of aluminum reduces the impact on the environment even further when the total vehicle lifecyle is taken into consideration. "Aluminum is much easier to recycle. It takes less energy to turn it back into a useable product," McNulty says. "We call it infinitely recyclable because it can be re-used without losing the properties it needs."
About half of the aluminum used in automotive applications today is recycled, according to Ducker researchers, who expect those levels to remain the same until at least 2020.
Some properties of aluminum, however, could create challenges for the collision repair industry. "Typically one cannot apply the traditional filler in holes like one does for traditional steel, since the adhesion may be insufficient," Makarewicz explains.
And as Friedman notes, "The outer panels on closures are typically heat-treatable alloys and need the paint process to gain full strength." The upshot is that there could be problems if the same paint is not used in the repair process. The welding process is also different for aluminum than for steel, and parts may be joined in a different manner.
These concerns are not an issue for collisions involving parts such as hoods and deck lids, because these are typically purchased as an assembly and installed on the car. But if aluminum makes its way into parts of a vehicle that are not replaced after a collision, technicians will require special training.
That's a distinct possibility, according to Ducker researchers. Based on interviews with what Ducker calls "thought leaders" in the automotive industry, researchers say there is 60 percent probability that a significant number of vehicles with partial aluminum body structures will be in production by 2020.
About the Author
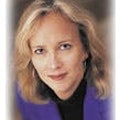