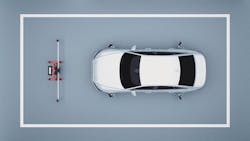
Thankfully our industry has seen a tremendous increase in attention paid to advanced driver assistance systems (ADAS) work. I am referring to what is presented during industry events, formal training from prominent sources such as I-CAR, and in articles published in the trade press. Our repair industry has been lagging behind new technology, so this awakening is good news for the consumer and shops. Vehicle manufacturers have helped this through their own training, shop certification programs, and their own increased involvement with our repair industry.
Though, speaking as a repairer, there has been little public attention paid to how shops, especially MSOs, incorporate this new type of repair work into their business model. Mastering the process is as big of a challenge as mastering the technology.
When I refer to non-body repairs, I am primarily thinking of ADAS, high-tech electrical, and traditional mechanical work. However, most of the same process steps would also apply to glass work, clear guard replacement, and paintless dent repair (PDR). All of these are usually not handled by traditional body technicians and are often sublet to other companies or departments.
Let’s walk through the typical steps of a vehicle collision repair starting from when the vehicle arrives.
Teardown
Most of us would agree with the philosophy of a complete and thorough teardown of the vehicle damage followed by preparing an estimate as thoroughly as possible (often referred to blueprinting), minimizing the chance for a supplement.
The body technician who performs the teardown must now be aware of the many ADAS and other high-tech vehicle features. This tech doesn’t necessarily have to be an expert. Most likely someone else will be performing scans, calibrations, programming, and troubleshooting. But the body tech needs to be aware of these systems and their components so that they can take appropriate steps of precaution when disassembling the damaged area as well as passing on relevant observations to the blueprinting estimator and the tech who will work on high-tech features such as ADAS. I-CAR training is helpful for this. If the MSO has their own calibration or high-tech departments training in house may be another option.
Blueprint
Typically the estimator who performs the blueprint (repair estimate) will work in cooperation with the body tech who disassembled the damaged area on the vehicle. In today’s world this is where we as repairers must start thinking differently and embracing high-tech systems. In the past often mechanical or other non-body items were handled through a sublet process. Often the thinking was to perform the majority of the collision repair work then send out the job for the non-body repairs. In a typical repair with insurance coverage the sublet cost and explanation was added to the estimate afterward. In other words, there was often a perception that the sublet source was the expert and the collision shop and insurer typically just accepted their guidance and billing. Even today many insurers ask to have an entry on an estimate describing the non-body operation and ask that the price be left off until the sublet invoice is received. Since these non-body operations usually come late in the repair process this represents a situation where supplements are being submitted at the end of the repair, which makes negotiations more awkward and creates a lot of last-minute administration work to close out billing. And the percentage of jobs requiring such outsourcing used to be much smaller. Due to changing technologies and vehicle sophistication, many jobs require it. Perhaps soon it will be most.
A far better scenario is one where the blueprinting estimator knows what operations will be required for the job, as well as the pricing, and then gets them on the estimate immediately. This requires knowledge and competence on the part of that estimator. Again, training is critical. I-CAR is a great source as they are significantly increasing their curriculum on ADAS and other high-tech features.
Looking up vehicle manufacturer repair procedures (and documenting them in the file) is mandatory. As vehicle sophistication increases, we have no choice but to become dependent on the manufacturer for repair procedures.
Knowing what options and features are equipped in vehicles has become a major challenge. In the past, most of us could easily pick out options. But in today’s world there may be little or few opportunities for visual evidence. Blind spot, lane observation or monitoring, and emergency braking are among many features that may not be evident. In the MSO that I work for we’ve started using a tool by CalPro. It uses an app on a cell phone to read the vehicle identification number (VIN) and deciphers many features and options including paint and trim codes. It uses artificial intelligence to show other likely equipped ADAS options. The user can indicate the area of damage and the tool will suggest some likely required calibrations. It is surprisingly accurate and very helpful. And there are others by different brands.
Because the MSO I work for does all ADAS and other high-tech work in-house, we’ve grown our staff and they have become very competent. Some of this staff works within our collision shops and some are mobile. Each collision shop has at least some presence from these people every day. We set up a process where every blueprint for every job that may include ADAS or other mechanical work is to be reviewed and input provided. These people with ADAS/mechanical expertise often point out required procedures that the collision people weren’t aware of. And these ADAS/mechanical people have developed expertise in finding repair procedures that collision people may struggle to find.
I can’t overemphasize the importance of getting every operation and price on the initial estimate. It streamlines the process. I see no point in waiting for sublet invoices if we know the operation is required and we know the price. And the insurer request for verification is a weak argument. We don’t wait for sheet metal part invoices. Why should we wait for a known ADAS or other operation from a different department or source?
Repairs begin
Once we have a completed blueprint (estimate), customer authorization, parts, and any needed agreement with an insurer we put the repair into process. At this point most shop management systems indicate the vehicle has been assigned to a technician to start repair. Typically, we’ve communicated with the customer regarding a completion date, even if to discuss steps and a point where we can project a date. Here is where a new step should be inserted — Communicate with the entity that will perform the non-body repair operation. If nothing else, that entity will know that the job will be coming to them at some point. As soon as possible give that entity a date so that they can schedule their portion of the job. This not only applies to ADAS and mechanical work, but also for glass, clear guard, upholstery, PDR, etc. At the MSO I work for we use an automated spread sheet for each non-body department that is to be updated and submitted daily. And in most of our shops we have a representative from our ADAS/mechanical staff attend daily collision shop production meetings. Those meetings are an opportunity to discuss variables and timing and to prioritize jobs that are shared. Our collision staff has come to learn that an efficient ADAS/mechanical department is busy and must schedule its work as well as businesses. It is not reasonable to expect other departments to have capacity without notice.
Transfer
Final billing
About the Author
Darrell Amberson
Vice president of industry and OEM relations
Darrell Amberson is the vice president of industry and OEM relations at Quality Collision Group.
Previously, he was president of operations for LaMettry's Collision, a 10-location multi-shop operator in the Minneapolis area purchased by Quality Collision Group in November 2024. Amberson has more than 40 years of collision industry experience and served as chairman of the Collision Industry Conference for the 2021-2022 term, as well as interim chairman for the first two CIC meetings of 2024.