I was reflecting back on significant events of the last month and I was struck by two things: the sudden influx of numerous “re-dos” that came to our shops, and the profoundly disturbing and increasingly common story of repairers forgetting who their customers are and our obligations to that customer. I am alarmed at what I am seeing and hearing when it comes to utilizing proper repair methods in the body shop.
The redos that I’m referring to aren’t the dreaded “comebacks” that occur as a result of an internal failure of our own processes. Rather, these are workmanship and service issues generated by other shops where the customer has lost confidence in the original repair shop and has brought the vehicle to us to be corrected. I am not thrilled by redos and we don’t solicit them. I take no pleasure in pointing out the flaws and shortcomings of other shops’ workmanship nor do I enjoy the inevitable difficult conversation that occurs with the good people from the original repair shop. Our practice is to try to convince the customer to give the original shop a chance to correct the mistakes. This is what I would want if I was in this situation. Unfortunately, some customers can’t be convinced or are just so fed up with the situation that they won’t return to the original shop. Then we are stuck with the repair.
By coincidence, two of the recent reworks involved rear body panel replacements on BMWs. The BMW replacement procedure requires the use of rivets and glue to attach the rear panel. No welding is allowed, yet the shop that did the original repairs chose to use conventional welding techniques to attach the panel. It wasn’t a “bad job” visually, but upon closer inspection, the onset of corrosion in the weld zones was already evident. The primary reason that BMW utilizes the rivet bonding method is because the chances of corrosion occurring after the repair is minimal.
The second BMW repair was “almost right” because the original shop did use rivets and glue to attach the panel. There were several significant problems that came up. First, based on the shop’s final bill, the shop used aftermarket rivets and glue instead of the OEM products. Secondly, the shop failed to install the required EMC screws that create an electrical ground for the electrical components that are attached to the rear panel. (The glue that is used to attach the panel acts like an insulator). As a result, when the customer drove the car after the repairs, the trunk would randomly open itself whenever the trunk latch circuit got just enough ground from the connection that flowed through the aftermarket rivets. Finally, BMW requires the use of a dedicated frame bench when pulling structural components and/or replacing them. The shop used a conventional frame machine to make the pulls and caused extensive damage to the rocker panel pinch clamps.
What I’ve seen recently isn’t pretty and I think we all need to take a moment to contemplate where we really are as an industry and then put into practice a few simple steps that can prevent most of the issues I witnessed. As an industry, we revel in the fact that we are craftsmen and can figure out a way to MacGyver a solution to just about any repair challenge. Unfortunately, this mindset can become our undoing. Unlike MacGyver, we don’t possess a vast scientific knowledge that allows us to thwart our challenges. But the good news is that we have access to a vast amount of scientific knowledge and it’s at our fingertips just begging to be used.
This knowledge is found on the pages of the OEM repair guides. I’m convinced that one of the biggest failures that occurs in the repair process happens during the repair planning stage. Too many of us are relying on old knowledge and past experiences when we create our repair plans. I’ve spoken with the managers and estimators at hundreds of shops and when we get on the topic of consulting the repair guides when creating our repair plans, I get way too many blank stares. This is just wrong thinking. As leaders in our shops, how can we expect our teams to properly repair customer vehicles unless we provide them with access to the repair guides? It seems to me that as an industry, we all need to create an SOP in the shop to obtain the repair instructions when creating a repair plan. Doing so will allow you to prepare for welding, riveting, bonding or a combination of these processes. Having the information about required materials will allow for you to get those materials ordered at the beginning of the job. To me, there are no reasonable objections to obtaining and following OEM repair instructions. The cost of the information shouldn’t be an issue because a lot of the information is free and the rest can be obtained for a nominal cost.
The costs of not having the repair instructions and not following them are far greater than the cost of a subscription to the information. Right now, there are shops writing checks to other shops because they didn’t follow OEM repair guides. Right now, there are attorneys that are lining up to sue shops that don’t follow OEM instructions. Right now, there are already shops on the hot seat in court, enduring expensive litigation because they didn’t follow OEM instructions.
What are you going to do, right now?
About the Author
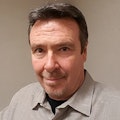
Steve Morris
The late Steve Morris was the regional director for Classic Collision in California (formerly Pride Collision Centers). He was an Accredited Automotive Manager (AAM) and ASE-certified master technician. Morris died April 22, 2022, at the age of 63 of complications following surgery.