We all know how to fix cars, right? I mean, that’s what you and your teams do every day. And you might see certain vehicles with certain problems again and again and again. So, we must know all the correct processes to repair those, right? I mean, there’d be no reason to look up the OEM repair procedures, right?
Wrong. If I’ve had the pleasure of meeting you on my travels, I’m guessing you’ve heard me say this: We must—and huge emphasis on the word must here—research OEM repair procedures for every repair. There’s no leeway here. But, my friends, I don’t have to tell you that this isn’t being done.
I’ve seen a number of surveys (including my own “Who Pays for What? Survey”) that say somewhere between 17 and 20 percent of all shops research OEM repair procedures on every repair. That’s a huge concern for our industry, as it’s shops, technicians and insurers that aren’t taking the time to look up the correct procedures.
I can already sense some eyes rolling out there.
If we’re doing the same repair on the same vehicle every day, we know the procedure; why waste valuable time in looking it up?
If that’s what you’re wondering, here’s an example: Let’s say you you replaced a quarter panel on a certain vehicle six months ago. You looked up the procedure, and the manufacturer required the roof to be replaced as well. You followed that guideline. Good work. All done. Now, that same vehicle with that same issue comes into your shop today, but maybe the manufacturer two months ago amended that repair information to include sectioning procedures that mean you don’t have to replace the roof.
The bottom line is that you don’t know what you don’t know. And the only way to ensure we repair vehicles correctly every time is to research OEM repair procedures every time.
OK, that ends my speech—but it doesn’t put an end to this topic appearing in this column. You see, one of the reasons I brought it up is that even among shops that want to do the proper research on each repair, there’s often a roadblock getting and interpreting the information. I get emails all the time asking where OEMs have diagnostic scanning information, for example, or how to understand the differences between specific markings and formats within the procedures for each OEM. These are valid concerns, because if you’re not that familiar with these repair procedures, it can be daunting to go in and quickly find the info you need.
For instance, let’s look at single-use parts really quickly. The fact is that there are a lot of shops incorrectly handling these parts, even those that do look up the proper repair procedures. Yes, OEMs have parts graphics we can use to get this information, but single-use parts aren’t easy to identify. BMW uses the word “replace” to identify them. Ford uses a trash can symbol. Nissan is a black circle with an “X” in it. Toyota is just a black circle.
If you only work on one BMW every couple months, how would you know that?
There are a number of ways to find repair information. Fortunately, a lot of it is available through your information provider—but not all of it is. One of the best resources out there is a website called OEM1Stop, which I’ve written about here before. The site offers quick links to each OEM’s site. Some require subscriptions or fees for access; some don’t.
That site is a great starting point, but you then need to understand how to use each OEM site to its maximum capacity.
So, here’s the plan: Moving forward, I’m going to do a series of columns explaining the different sites, taking on one OEM each column and explaining the ins and outs of its offerings. It’s one thing to say, “Here’s the information.” It’s a far different thing to actually learn how to use it to your benefit—and keep this research phase of the repair process from becoming a drain on efficiency.
Let’s get out of this cycle where we sit back and assume we know the correct procedures, or that doing proper research will only hinder us in an industry too often only judged by speed. Let’s admit that we don’t know what we don’t know, and that the only solution is to make research part of our standard processes. Let’s change now.
About the Author
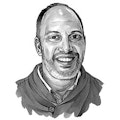
Mike Anderson
Mike Anderson, the former owner of Wagonwork Collision Centers in Alexandria, Va., operates CollisionAdvice.com, a training and consulting firm that assists shop operators nationwide. He is also a facilitator for Axalta Coating Systems’ 20 Groups in the U.S. and Canada, and is an Accredited Automotive Manager. Reach Anderson at [email protected].