The Reviewer:
As a child, Mark Cipparone, owner of the five-location Rocco’s Collision in the Philadelphia area, was always in the shop with his father. His father opened his shop in 1957 and in 2000, Cipparone purchased the location from him.
The Shop:
Since Cipparone took over, he’s added three additional locations and is looking to expand even further. Currently, there are three locations spread across New Jersey and two in Philadelphia. The Rocco’s Collision team is made up of roughly 70 employees. Cipparone says he makes it a point to grow his own employees and he has a long history with the management staff.
The original location of Rocco’s had very limited space, so Cipparone needed to find ways to maximize production. Although his facilities have gotten larger, his dedication to efficiency has stayed the same.
“I’m really selective about how we fix cars,” Cipparone says.
Recently, his staff came to him and proposed myQCIQ.com. As a team, they made a list of the pros and the cons.
The shop was given a demo of myQCIQ.com to try out for 10 days. The shop had been using paper and pencil methods of tracking quality control, but the staff was looking to modernize and interested in seeing what a digital system could offer.
What sold Cipparone was when he had his 22-year-old son—who has knowledge of the industry but is not yet an expert—try it out. His son was able to perform a quality control check on a vehicle without missing any steps.
“Anyone with some sort of mild background can operate this tool,” Cipparone says.
How It Works:
Cipparone says that myQCIQ.com is an app that can be used on any PC, smartphone or tablet with web access. Once a shop has it, repair data from CCC ONE and Mitchell are automatically imported. Anytime throughout the repair process, a user can log into the program and go through the estimate line by line and mark it as either a pass or a fail. If it passes, that means someone physically looked at it and accepted the repair. If it is a fail, the user then takes a picture and selects a failure type to show why it didn't pass. The information is automatically uploaded. The management team and select employees will receive automatic alerts of failure occurences.
The Review:
The app is fairly new (released in the beginning of April), so as of print, Cipparone’s staff has only been using it for a few weeks but, so far, he’s happy with the results. Cipparone likes the fact that it’s easy enough for almost anyone to use and that it holds everyone accountable.
When compared to the paper and pencil method, Cipparone says that going digital has rejuvenated everyone’s commitment to quality.
The ROI:
“Customers are worth a lot of money,” Cipparone says. “So retaining those customers is huge, and I think this product helps with that.”
Cipparone says the entire process depends on the nature of the job, but on average he says it takes anywhere from 10-20 minutes. This extra time is well worth it when it comes to giving customers the confidence that their vehicles have been repaired correctly. Cipparone adds that this is a great feature to bring up during the point-of-sale conversation and he believes it will give him a competitive edge against other repairers in the area.
Another benefit is cutting down on comebacks. By ensuring that a vehicle is being repaired correctly every time, the customers are more satisfied and the staff doesn’t have to stop production when a car comes back in. Cipparone adds that it also reduces costs because the shop isn’t having to shell out money for a rental car if a customer has to come back.
About the Author
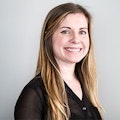