This is my first column for FenderBender but I have been associated with this publication for close to two years as a member of the advisory board. I consider this magazine to be the Wall Street Journal of the collision repair industry with thoughtful and relevant content produced by a highly motivated and engaged group of reporters and editors. I’m happy to be a part of the team and look forward to sharing some of my thoughts, observations and solutions with you in upcoming columns.
I’m proud to be part of the collision repair industry. During my career, I’ve been fortunate to be a leader, mentor and coach to over 500 team members in the shops where I have served as director of operations. I’ve also been lucky to be associated with some of the finest men and women in the country who work so hard to be successful as owners and operators in a business that generates very slim margins and requires significant capital investment in equipment, infrastructure and technical training.
Our business is evolving at a rapid pace and this rate of change will increase exponentially in the very near term. I’ve been thinking about all the changes that have occurred in the last two or three decades and how resilient you, the body shop owners and operators, have been to rise to every challenge.
It wasn’t very long ago that we painted cars with single-stage acrylic enamel that we bought as a factory pack from a jobber, or we’d give the jobber a fuel door from the car so that the jobber’s paint match guru could match the paint for us. Now we mix our own paint using computerized scales referencing formulas generated from photo spectrometers and apply it in up to four stages. You’ve adapted to that change.
Many of you recall that it was common to weld replacement panels using open flame gas torches, and coat hangers or brazing rods. Now we may attach panels using high amperage spot welders that generate 1,000 pounds of clamping force in the weld zone. You’ve adapted to that change.
Do you remember the Chevy Citation or the Chrysler “K-car” when they first started showing up in your shop? Many of us worked hard to understand these vehicle design changes and the strange ways the vehicles reacted in an accident. We are now dealing with an alphabet soup of construction materials that include HSS, UHSS, SMC, PVC, as well as aluminum, magnesium, and carbon fiber. You’ve adapted to these changes.
Very few businesses operate in an environment where the customer pays for only a small portion of the cost. We’ve witnessed the advent and evolution of the DRP model in all its various forms, and the accompanying balancing act that repairers perform to achieve certain KPIs while still repairing vehicles to OEM standards.
We are saddled with the inefficiencies associated with being directed to use certain types of non-OEM parts from specific vendors using one of several electronic parts procurement platforms. Salvage yards are now selling parts with newly created titles (opt-OE) and several independent companies have entered the parts space, moving these parts outside of the normal dealer supply chain. You are adapting to these changes.
Like a surfer dropping in on the Banzai Pipeline, we are riding a massive wave of technological advancements in vehicle systems that will crush us if we don’t master the techniques and processes for safely repairing and restoring these systems. More on this will be discussed in future columns but for now, many of you are adapting to this change.
I’ve only touched on some of the challenges we’ve dealt with in the recent past, but these few examples remind me of just how good we really are. Many of you have created a positive, values-based, employee-centric culture within your organization and have fostered a system of continuous improvement. One of the things that makes me most proud of this industry is the fact that despite all the adversity that comes with this business, I see so many owners and operators giving their time and resources generously to their communities. For example, how many single moms, veterans and struggling families are now the proud owners of a great vehicle that was lovingly restored and then donated to them by a body shop? The original idea for this benevolence program was created by body shop owners many years ago and it has blossomed into something of which we can all be proud.
What are our current challenges and what can we expect to face in the future? I’ll talk about that in upcoming columns and I’ll share my insights and possible solutions to these challenges.
We will continue to adapt and prosper. See you next month.
About the Author
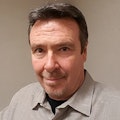
Steve Morris
The late Steve Morris was the regional director for Classic Collision in California (formerly Pride Collision Centers). He was an Accredited Automotive Manager (AAM) and ASE-certified master technician. Morris died April 22, 2022, at the age of 63 of complications following surgery.