A lot of time, money and effort goes into setting up an apprenticeship program. But if you don’t have the right mentor? It all falls apart.
That’s why, in addition to training technicians, Service King took on an initiative that cultivates mentors as well. Service King’s Apprentice Development Program hires experienced employees as full-time instructors to coach and guide first-year technicians for 52 weeks.
Ralph Gonzales, who has spent over 40 years in the industry, 15 of which have been with Service King, served as the guinea pig for the program at the company’s northeast Dallas location, spending 40 hours each week mentoring three technicians who achieved CSI scores over 98 percent, including one technician who experienced zero comebacks. All three technicians graduated from the program and are now employees at Service King.
Gonzales, who schedules his day around training technicians and tracking their progress, shares his observations as a full-time mentor and how that level of dedication ensures industry-ready talent.
I feel I am now doing the most important work of my life. You work your whole life to build knowledge and the skills you’ve got. You carry them with you, and you should pass them on to young students, have them take over your steps.
It’s frustrating that apprenticeship programs aren’t more popular. The problem is most shop owners don’t want to start all over with an open position. Why try finding somebody with years and years of experience when you’ve got a senior tech on hand that’s put in his time, paid his dues, and is ready to pass it on?
Technicians have to learn through hands-on experience. At most of these technical schools, they learn quite a bit on the books side, but I’ve found out they lack a lot of experience and it becomes difficult for them to get a job. We give them the chance to work on real jobs that come through our shop.
We take these kids step by step on how to properly repair cars. The way I learned to repair a car was watching others. Every shop you go to, there’s always a good tech that’s better than you. They’ve always got their opinions and techniques on fixing a car, and that’s how I learned.
I designed a list of repairs that they need to complete before finishing the course, and we just send real jobs their way as they come through the shop. Then I’m checking their work, pointing out things they missed, what they could have done differently.
In the morning, between 9 and 10 a.m., I have them go over the vehicles and plan their day. They must inspect their list, and then they must check and see if their orders are in. And then I help them schedule the day, which cars need to go in what order.
Then pretty much the rest of their day is booked. I’m just there making sure everything is running. It’s just all quality control for me. I make them repeat all their procedures day in and day out, every day. I have them measure and check suspension, check for previous damage, hidden damage, and look up all the documentation on every car that comes in.
I’m really just trying to drill processes into their heads. Every manufacturer, every vehicle has a certain way to be repaired, but they can’t forget about the basic things that ensure we don’t get comebacks. It seems simple, but they need someone there constantly reminding them, leading the way. Once they get those basics down, then you see them develop their own styles and really start to flourish.
It’s really about them gaining the confidence to go out and do the work on their own. Young techs have a lack of confidence. Getting to talk to them and witnessing their accomplishments is overwhelming. These kids are eager to learn, and all they want is a chance. They tell me time and time again that they appreciate the knowledge I’m giving them, how unsure of themselves they were before. They can see their careers, their finances, their plans unfolding in front of them. These kids are now going to be able to go out and make a living.
FenderBender Awards Insights feature past FenderBender Award nominees. To nominate an inspiring collision repair professional, or for more information, go to fenderbenderawards.com.
About the Author
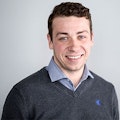