On July 15, American Honda Motor Co. announced that all of its vehicles involved in a collision require a pre- and post-repair scan to determine if any diagnostic trouble codes (DTCs) are present. Safety and driver assistance systems will also require inspection, calibration and aiming after the repair, according to the announcement. Both Fiat Chrysler Automobiles (FCA) and Toyota made similar announcements, and General Motors (GM) is rumored to have a statement coming, signaling a dramatic trend in the industry.
During this year’s NACE/CARS Conference & Expo in Anaheim, Calif., FenderBender columnist Mike Anderson led a panel of OEM and insurance representatives on the topic, and the consensus among the automakers represented (Honda, Toyota, FCA, GM, Audi, and Nissan North America) was that pre- and post-repair scanning is a quality issue for all parties involved and the only way to accurately identify damage. Chris Tobie, collision business specialist at American Honda, took part in that panel and shares why Honda decided to take this position and what it means for collision repairers.
Why did Honda feel it was necessary to release a position statement on pre- and post-repair scanning?
We are always listening to our ProFirst shops and attending events to learn the issues that are facing the industry. The topic of pre- and post-repair scanning became very hot last year and we started researching the actual situation. Our initial research showed considerable “gray area” and most manufacturers hadn’t provided any guidance to the collision industry on which diagnostic scans and post-repair calibrations were required and expected in these situations. Frankly, some of the misinformation floating around the industry caused us great concern. American Honda is committed to the complete and proper repair of our vehicles and we felt there was an obligation to inform the entire industry of our position on the matter, the reason behind that position and where to obtain scanning resources. When the ever-increasing electrical complexity of our vehicles was also taken into consideration, the time was right for this position statement.
What is the importance of pre- and post-repair scanning, particularly as it relates to the collision repair process?
A pre-repair scan must be done during blueprinting for the final estimate to learn which DTCs are stored in the vehicle and, therefore, what systems may have been affected by the unknown collision forces. This helps ensure any damage becomes part of the estimate and repair plans and might help reduce surprises and repair supplements. If vehicle damage prevents scan tool communication, then the pre-scan must be done as soon as repairs can safely allow scan tool communication to be re-established. A post-repair scan confirms that all issues related to the collision have been corrected, including those DTCs that might have been set during the repair process.
The position statement says that scanning must be done on all vehicles that have been in a collision. Why is it imperative to do this with every vehicle?
Basically, a proper repair is that important and we wanted to place sufficient emphasis where necessary. In a mechanical repair situation, we often have a customer complaint that leads us down a diagnostic path where scans and calibrations are an integral part of the published repair procedures. In a collision, we have a complex situation where a vehicle has received some unknown G-force impact to the body and electronic components. Without the proper diagnostic scans, we don’t know what problems might exist or whether the vehicle was completely and properly repaired. We recognize that cost control is required and a necessary part of any business. However, cost control at the expense of a complete and proper repair is an unacceptable situation to American Honda.
“American Honda expects the industry to adapt and follow the guidelines detailed in the position statement.” —Chris Tobie, collision business specialist, American Honda
For shops that weren’t previously doing pre- and post-repair scans, what will they have to do to prepare for this?
There are basically three options. The shop can establish a business relationship with a local Honda and Acura dealer to handle all of the requirements. Or, the shop can do the scan and calibration work themselves by purchasing our i-HDS software and equipment, plus any other required tools and service information specified in the position statement, and then train personnel to use the i-HDS. Lastly, the shop can contract with a third-party vendor to do the required tasks. For shops that choose that option, you must carefully evaluate the capabilities and skills of available providers. American Honda does not currently recommend or endorse any third-party diagnostic scan and calibration providers.
Will Honda be providing any type of training support for scanning?
Using a scan tool to read DTCs is pretty straight forward and a matter of following on-screen prompts. However, if training is required, all of the online technical training we provide to Honda and Acura dealers can be purchased and downloaded from Helm Incorporated. We are already planning to create an online training course on driver support systems calibrations as part of our HON collision repair training series delivered by I-CAR. A second online HON course about pre- and post-repair scanning is also under consideration.
Shortly after Honda made the announcement, Toyota made a similar one. Do you think this is the direction that all OEMs will go?
Several OEMs have now issued similar statements, but any comment on whether others in the industry would follow would be speculation.
What impact do you think this announcement will have on collision repairers?
This position statement represents change. Like any other change, it will take some time for the industry to get used to it. American Honda expects the industry to adapt and follow the guidelines detailed in the position statement.
What feedback have you received from the industry since the release of the position statement?
American Honda has received overwhelmingly positive feedback from the collision industry. We spent extra time during the development of this position statement sharing our proposal with selected industry contacts so we could better understand the actual situation from different industry perspectives. That led us to making significant revisions to our original draft.
About the Author
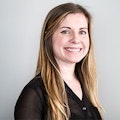