A 1987 Chevrolet Caprice station wagon sat in his driveway, with a horrible rust-brown tinge covering the exterior.
Robert Rodriguez wanted to repaint it, but he had little money and no painting experience, which led him to enroll in his high school’s auto body class.
Ten years ago, learning basic painting techniques and proper filling methods was just a means of restoring that Caprice to its former glory. But the summer following his graduation, it became a lifestyle: His teacher set him up as a prepper at a local shop, and Rodriguez never looked back.
Able Body Shop
Location: Anchorage, Ala.
Size: 13,000 square feet
Staff: 20+
Average Monthly Car Count: 175
Combined Annual Revenue: $6 million
“I fell in love with everything about the industry and have been doing it ever since,” he says. “There’s just something about getting your hands on a vehicle and feeling the bodylines, the smoothness of the paint. I can’t explain it. It feels like what I should be doing.”
Eventually, Rodriquez moved to Able Body Shop in Anchorage, Ala., where he started out as a helper in the paint department. He has worked his way to head painter status by working on improving efficiency in the paint department each and every day.
AS TOLD TO TRAVIS BEAN
In our paint department, it’s our paint shop manager, then myself, and then a prepper and a buffer. The manager and I work in a split shift, and I'm in the later shift. I get here around 9 a.m., and my shift starts at 10. The other painter on my team works the 6 a.m. to 3 p.m. shift.
When I get here, I walk the floor and see what the teardown workers are doing. I'm seeing if there are any little quick bumper jobs. I’ll find out what's going from them to the body side, then visit the body men. I check what they’re welding, or if they're doing a final skim coat of Bondo, and find out what work they have coming in the next couple of hours that will be coming over to the paint side.
Then I usually clock in, check in with our production manager, see what our schedule is looking like, then head over to my department. Then I check the schedule once again with my head painter, split the work down the middle, and then hunker down and get spraying.
It’s definitely about teamwork between the paint shop manager and me. There will be times when I’m color matching and I’m just stumped. He’s had previous experience as a tinting professional at Sherwin-Williams and a couple other paint companies, so after I’ve gone through every single step, it’s nice to just sit back and let him say, “This just needs a bit more reddish blue in there.” I’ll do the same for him when needed.
It’s so important to have healthy lines of communication with everyone during the process. All the way from our front office staff down to the detailers, having quality open lines of communication and staying constructive with everybody is key. You have to check your ego at the door every day. It’s about the team—not about you.
I make a very concerted effort to speak with front office staff at least once a day. Not even about the shop. Just asking how their day is. Showing there are people that care about them. It makes them smile and it makes them happier, and the customers see that smile and they can't help but smile. It gets you in the mood for the day and builds shop camaraderie.
The first thing I’ll do is walk around the car. I’ll grab the repair order, read every single line, and inspect what the preppers have done. As a painter, you make sure that job is flawless before you start painting, because there’s no sense in painting it twice. So I'll walk around the car, closely examine the Bondo and primer and make sure there aren’t any little pinholes or chipped paint that was missed.
There are a lot of precautionary measures I take to save time on jobs. With all the snow and rain in Alaska, water is a huge issue, so before I bag the car and head into the booth, I take a Scotch Brite pad and get inside that wheel well and blow out every single little jam to get any dirt remnants out. If you get a little bit of water in there, it can warp your physical base coat and make it look like beads of water hit it.
You have very little downtime as a painter, so to make the job go a lot quicker, I don’t just focus on the job in the booth, but the next job coming down the line and getting the color for that one ready. If you’re trying to tint color with a car that's in the booth ready to go, you're losing time on that job.
From there, I’ll bag the car, wipe it down, and do some color matching. When I grab color chips and look up the paint code, we see all the different variants for the different plants the vehicle was sprayed at. From there, if I get a good enough color match, I’ll go to the bank and start mixing my color.
About every other car we get has suffered from a bad paint job. Sometimes there will be four or five different colors all over the vehicle. If we have a poor color match, we have this really interesting camera (Axalta’s Acquire Plus EFX) that takes a physical picture of the pane. Then it will go through on the computer and give a best exact match. Even if the camera comes up with a pretty good match, you can tinker with it to make it more exact.
If we don’t find something with the camera, or we don’t find something with our chips we have, we’ll use some other paint line to see if they have anything that's a color match.
Then it’s on to the paint booth. A big step in improving efficiency here has been switching to waterborne, which we actually just did a couple months ago. That has definitely been a very large learning curve for the head painter and myself. We went down to California for three days of training. It’s a game changer for us.
If you’re spraying solvent, your blend technique is completely different. You want to do medium to medium-wet coats, whereas with waterborne, you lay down your wet beds super heavy. And then, depending on the color, you’re looking at a coat-and-a-half in covers. The transition from doing those medium coats and finessing a blend out to hammering on a base coat and doing a small little orientation coat has been really fantastic for improving our workflow.
We’re very cognizant of paint department efficiency numbers here. Right now, our goal is to be operating at 170 percent efficiency. We’re at 164 percent right now. We come up with ideas and strategies for reaching our goals at monthly meetings.
One way is sealing less repair panels. We’re just trying to use more of our 1K (one-component) paint—which
has a nice phosphorus acid edge to it—strictly to seal brand new parts. That makes us way more efficient and cuts down on our wet bill, which we
get monthly reports on.
I help by keeping track of how much clear we use. I’ll take our clear can and put a piece of tape down the side of it, write an RO number and how many hours that job is. Once we get through that can, we’ll tally how many hours we sprayed out of it. I put a little rubber bladder in a hard plastic cup and then mix into that. I’ll take 34 ounces of that, set it aside, and anytime I mix up my clear coat, any little bit that’s left over, I’ll tip it into there and track how long it takes me to fill up that 34 ounces.
I’m usually the last one still at the shop. My job is to lock everything down, and even then I can find ways to make the next day go smoother. I walk the lot and make sure all the keys are pulled from the vehicles. This gives me another opportunity to see what was dropped off.
From there, I stage everything for the next day for the morning painter. I usually like to have one car parked,
bagged, and wiped down. Best-case scenario: I’ll have a color picked out and ready for him to go, that way all
he has to do is walk in, mix and start going, which makes our day go quite a bit quicker.
About the Author
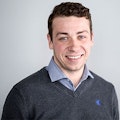