“This is truck country.”
Matt Parker lets the words linger for a moment. The answer, to him at least, was that clear cut. Parker Auto Body, his 18,000-square-foot West Monroe, La., collision repair facility, pushes through $3 million of work annually—nearly 40 percent of which comes from light-duty trucks.
“Louisiana is truck country,” he repeats. “That truck, it changed everything. Everything.”
First, here’s the question: Why should you invest in becoming capable of aluminum structural work?
The cost of entry can be steep—very steep—depending on circumstances, Parker admits. And, as of this story going to press, the number of aluminum structural repairs occurring throughout the industry have been a bit, well, lackluster (more on that later).
But, still, there’s that truck: the 2015 Ford F-150, North America’s first mainstream aluminum-bodied vehicle—the hulking, sparkling embodiment of what many believe to be the future of vehicle construction forged from an auto industry consumed by a furious race to lightweight designs and decrease fuel consumption.
As FenderBender reported in 2015 (“Advanced Materials: Collision Repair’s New Frontier,” June 2015), aluminum use in vehicles is on the verge of reaching critical mass, a point at which being capable of performing extensive work on aluminum will become a necessity for the majority of shops. The message from many across the industry was clear: The time for change is here.
But, roughly a year after the first aluminum-bodied F-150s hit the streets, how much change has really occurred? Is the collision repair industry ready for aluminum structural repair? And, maybe more importantly, should it be?
Do the Math: The Prevalence of Aluminum
According to FenderBender’s 2015 How I Work survey, only 5.2 percent of respondents said that “vehicle design enhancements” (which would include aluminum-body vehicle designs, by the way) as the “single biggest challenge” facing the repair industry. Compare that to the oft-cited technician shortage (32 percent) or insurer influence on repairs (28.3 percent), and you get a pretty good idea of where advanced materials sits on the hierarchy of shop operator concerns.
Other numbers, though, suggest more should pay attention.
In all, more than 500,000 pickups and electric vehicles produced in 2015 had aluminum bodies, Ducker estimated.
And as for the F-150, a shortage of vehicles due to manufacturing constraints caused a sluggish start to 2015 sales. When Ford reached full production in the second half of the year, though, sales ramped up. More than 65,000 F-series trucks were sold in November, a 10.4 percent year over year improvement, and Ford topped 85,000 trucks in December, the first time it had done so in more than a decade.
In all, more than 780,000 F-series trucks were sold in 2015, marking the 34th straight year it finished as the nation’s highest-selling vehicle.
Still, only a fraction of those aluminum-intensive vehicles will need repairs this year. Various reports suggest that there will be less than 70,000 aluminum-intensive vehicles coming into shops in 2016, roughly 700,000 if vehicle closures (trunks, hoods, etc.) are included.
But, this is just the start, according to Ducker. By 2025, when Corporate Average Fuel Economy standards are to be met, Ducker’s research suggests that 70 percent of all new light-duty trucks will have aluminum bodies, and all major automakers will have an aluminum-body platform. More than 75 percent of all pickup body and closure components will be aluminum, 24 percent for economy vehicles, 22 percent for SUVs, and 18 percent for minivans.
The Shop Experience
Currently, aluminum repair is simply another repair segment or specialty for a body shop, says Scott Biggs, president and CEO of Assured Performance Network (APN), which now administers the certified or recommended repair programs for six separate OEMs.
For its part, I-CAR holds a similar position—and stresses the importance of becoming capable of repairing advanced materials.
“As we approach the Corporate Average Fuel Economy (CAFE) standards requirement by 2025, we’re finding that collision repair professionals need to be prepared to repair increasingly complex and varied materials beyond aluminumand steel-intensive vehicles,” says Jason Bartanen, I-CAR’s director of industry technical relations. “Mixed-material vehicles comprised of steel, aluminum, composites and other materials are becoming more commonplace as solutions to reduce weight, increase safety and accommodate technology. Aluminum- and steel-intensive vehicles, along with mixed-material vehicles, require specific training, tools, and equipment for complete, safe and quality repairs.” So, again, what has the shop experience been like for early adopters?
Getting Ready: Aluminum Adoption
Parker started the process of becoming aluminum-ready near the end of 2014. It took roughly five months, he estimates, to purchase (and receive) the needed equipment, build an in-house aluminum clean room, and train himself and all three technicians. In all, he says the cost came out to just under $100,000.
“We didn’t spare any expense with it,” he says. “I tend to go all out when I do things—do it the absolute best way I’m able to. I’d guess, if we went with some [more affordable] options, like not constructing a clean room, having less people take the training, etc., it would’ve been more like $50,000 or $60,000.”
Today, Parker and Parker Auto Body are among the nearly 2,500 in APN’s group of certified shops, the majority of which hold multiple OEM approvals.
That accounts for a little more than 5 percent of the total industry, a drastic rise from the less than 1 percent in the program just two years ago. Of those involved today, only roughly 25 percent are dealership owned; the rest range from small independent facilities to the largest MSOs.
Specifically for Ford, there are already nearly 1,200 shops in its recommended network (which APN manages), roughly 700 of which are dealers. I-CAR has had more than 22,000 students go through its 2015 Ford F-150 Structural Repair Training Course, 63 percent of which were collision repair professionals; more than 5,700 organizations, overall, completed it.
Of course, there is also a large number of shops involved in programs run independently by automakers themselves, including Mercedes-Benz, Audi, Jaguar Land Rover, and, most recently, GM’s Cadillac.
In all, it’s estimated that there are nearly 4,000 facilities in the country capable of aluminum structural repairs. And it appears the industry is on a strong pace to becoming aluminum ready, says State Farm spokesman Justin Tomczak.
“Obviously, State Farm doesn’t repair vehicles but we do have the opportunity to observe repairer work, hear feedback from our customers and engage in discussions with the repairer community,” Tomczak says. “ … Our customers have not reported having difficulties in finding a repairer for their aluminum repair needs. We think that may be a good indicator that the industry is adapting to the needs of customers in their local market.”
Getting Paid: Real-World Experience
The first aluminum structural job that ran through Parker’s shop in mid-2015 was an extensive repair on an F-150. The total ticket topped $20,000.
“It was a job that went through Progressive”, he says. “And they paid it without question, including our aluminum labor rate.”
“[Progressive] paid the next one, too, without question,” he says. “But I’ve had some issues at other times. I had one truck that [an insurer] chose to total rather than pay my rate. Some have had no problem, some have, but I refuse to do it for any less.”
State Farm’s Tomczak says, “The market will determine what is competitive for the repairs performed.”
Steve Trapp, North American strategic accounts manager at Axalta Coating Systems, says that typical rates accepted by insurers have tended to be around “1.5 times the normal body rate.”
That calculation jives reasonably well with the results from National AutoBody Research’s variable rate surveys. The average rate for structural aluminum work in each of the 11 states that have posted, public results, all range between 1.5 and 2 times the average body labor rate. Although none top that, the “high rate” for structural aluminum work in multiple states was above 2.5 times the average body rate.
Those rates are up to the shops to determine, Biggs says, and he says he has heard “virtually nothing” about pushback from insurers. He feels that many carriers have a strong understanding of what it takes to make these advanced repairs and are willing to pay for what is necessary.
Education will continue to play a crucial role, says John W. Eck, manager of the wholesale dealer channel at GM. For the company’s Cadillac program, launched in late 2015 in anticipation of the release of the aluminum-intensive 2016 Cadillac CT6, GM has set up self-guided courses for insurers that detail the repair process of the new vehicle.
“We want a best-in-class repair experience for [CT6 divers],” Eck says. “We want the vehicle restored to the OE standard, and we want everyone involved to understand what that entails.”
Getting a Return: Recouping Costs
As of December 2015, Parker estimated that less than 3 percent of his shop’s $3 million annual workload came through his certification programs—about what he expected for a transition year into aluminum work, he says.
“Still, this is a long-term investment,” he says. “I wasn’t expecting to make back my $100,000 in a few months.” “This is about positioning myself for the future.”
Some automakers require vehicle owners to only use their certified shops, and that’s where some advantages for those in various networks come in.
Cadillac is going that route for structural work on its CT6, Eck says. And the company will only sell certain parts and vehicle components to certified shops to ensure it stays that way. Repairing the vehicle “requires an additional level of readiness,” he explains, and the company doesn’t want to take the chance.
There is a misconception, though, Biggs says, about the purpose of the certification programs, and “immediate” gains shops may or may not get.
“Certainly, shops are choosing certification as an alternative to DRPs, but it doesn’t work the same,” he says. “There’s no one turning on the faucet for you once you have the certification, the way it might go for a DRP. You have to gain that business still. You still need to market it.”
Ford, for instance, does not require its vehicle owners go to a Ford recommended shop for aluminum structural work. The auto giant has no restrictions on its parts.
Biggs does not see that as a problem; neither does Parker.
“This is an expensive vehicle,” Parker says. “I have a 2015 [F-150] King Ranch, and it was $63,000. People spend money on these vehicles, and they care about them. They aren’t going to trust just anyone repairing it.”
“Consumers are smarter than we often give them credit for,” Biggs says. “They know, above all else, they want their vehicles repaired correctly—especially if they’re driving a vehicle that would be in one of these [repair] programs.”
APN does a great deal of consumer-facing marketing, and Eck says Cadillac will have “a glovebox companion” available to educate customers.
In a more tangible sense, the costs of certification (normally an annual fee ranging between $2,500 to $5,000) is recovered in a couple repairs. The initial cost of entry (equipment, tools, facility enhancements, training, etc.) can take several years.
A Look Ahead
Advanced materials are not going away, I-CAR’s Bartanen says. And the industry is going to need to continue to push its education and training as vehicles continue to advance.
The launch of the 2015 F-150 changed the landscape of aluminum repair, and according to the Ducker Worldwide Study, last year marked a turning point for wide adoption of the material in vehicle design. The next 10 years will see a rapid increase.
“Is it a must for shops to be doing this today?” Biggs asks. “It depends on how you look at it. I can tell you that it’s imperative to get in today, as the cost of entry will only get greater and greater in terms of capturing that market share.”
Parker Auto Body is part of eight different repair programs (General Motors, Ford, Fiat Chrysler, Hyundai, Nissan, Infiniti, Honda and Acura), and Parker feels his business is in a position to capitalize on its expertise in the future—while competitors will be left behind.
“It’s sort of a waiting game right now,” he says. “We’re building that reputation, and waiting for the market to [saturate] with those vehicles. The vehicles will come. This is truck country. I have no doubt they’ll come.”
About the Author
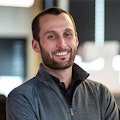
Bryce Evans
Bryce Evans is the former vice president of content at 10 Missions Media, overseeing an award-winning team that produces FenderBender, Ratchet+Wrench and NOLN.