Chesiree Johnson started running auto repair shops in high school. Well … sort of. Her auto shop technologies class would take on repair jobs in the community, and the teacher assigned Johnson to be the manager of the school’s “shop” during her junior and senior year.
That teacher must have observed the same traits in Johnson that production manager Bill Huffine saw when he hired the then-18-year-old to be parts manager for Gerber Collision in Scottsdale, Ariz., two years ago.
“Although [Johnson] has only been in the industry a short two years, her skills far exceed parts managers I have worked with [with] three times the experience,” writes Huffine in his FenderBender Award nomination for Johnson. “With her attention to detail and following procedures to a ‘T,’ she has kept our returns to a minimum while increasing cycle time and tech productivity.”
Johnson is a shining example that age doesn’t always factor into success. If you’re organized and driven, you can keep a business running smoothly.
When I started here, the entire repair process was definitely something new to learn. I did have a background for part of it, but mechanical class in high school is a lot different than being in the industry. The key for me was organization. You have to keep everything in line, because if I get something wrong, then the tech is under the wrong impression, and then it just backs up the whole shop.
To start the day, I go through the list of vehicles that are in the shop, making sure all of my orders have been placed the night before and that they were all answered. Then I get ready for the morning meeting at 8 a.m., so when they do ask me about those parts and when they’re going to get in, I have answers.
Then we do a walkthrough of all the vehicles so we can see if they need additional parts and so I can collect any other information for our writers. I have my clipboards arranged on my office’s wall and separated out for each job. I order the parts for those vehicles and make sure the body techs have their sheets filled out so they know what vehicles they have for their parts racks and so they can put all their parts in their designated areas.
A lot of that information is derived from our CCC ONE estimating system. I pull the parts list from the estimates, and those parts are checked throughout the day by our writers. Our parts are pulled from there. I go one step above and take that information and set up sublets for glass when those get called in as the car progresses through the shop. It’s essential to keeping the flow going in the shop and getting things moving in the right direction.
I have a 1 p.m. meeting with Bill, and we go down to the vehicles that are going to leave that day or the next day, making sure all those parts are here, correct, ready to go. Usually by that time, the cars are together and washed.
I have filing bins where I have orders that are in process, and orders still waiting for ETAs. I have them stacked up by dates. I keep them all together. If they’re coming in today, they’ll be in my stack for those, and then if they’re coming in tomorrow or if it’s backordered, that will go in a separate bin.
Throughout the day, I’m constantly opening and checking parts as they arrive. I go out to the vehicle with the part to make sure it’s correct and that the tech doesn’t need anything else. If something is wrong, I make it a priority and can usually fix it pretty quickly.
I keep a huge log of all my different contacts. I’m constantly emailing, talking on my desk phone, calling them on my personal phone.
And then at the end of the day, I go back, rearrange my filing bins and make sure all the orders are placed for the next day.
About the Author
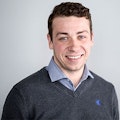