These days, when I’m channel surfing, I often land on a couple reality TV shows that, to me, are extremely intriguing: Bar Rescue and Hotel Impossible.
When the hosts of those TV shows visit struggling businesses, they often observe staffs that do things simply because that’s the way they’ve always been done. What really stands out to me is how often you notice staffs get complacent. Employees walk past a situation where a wall needs to be painted, for example, and never take action. A lot of times, those issues can be fixed by someone viewing things from a different perspective and pointing it out to the struggling business’ staff. You could have trusted colleagues from 20 Groups come visit your shop and observe your shop floor, for starters.
But here’s another, extremely helpful solution that can initiate positive changes at your shop: Utilize the Ohno Square. The Ohno Square gets its name from Taiichi Ohno, who helped inspire Toyota’s extremely efficient production system and the lean processes that automaker has made a habit of using.
When Toyota used to hire a new manager, they would literally draw a square on the ground in a factory and make that new manager stand and watch employees work—have a notepad and observe what people were doing, and become aware of what the workload was for their staff.
Sometimes, the answer to solving your shop’s inefficiencies comes from simply being observant. I’ve used the Ohno Square method in my shop before. I used to put on a safety vest on the shopfloor, and no one was allowed to talk to me because I was observing the staff at work.
As shop operators, we tend to assume a lot of things. The more that we can move away from simply assuming things and actually verify and track employees the better off we’ll be. Track employees and their movements, to learn, for example, if you have your shop’s tools and equipment placed in the proper areas.
It comes down to being aware of what your team members are going through. Because when we, as shop operators, sit in our corner office and simply make assumptions based off our business’ history, it can lead to problems like not being properly staffed. Maybe you’ll become aware that, ‘Holy cow, I’ve got to get my staff some additional help.’ Sometimes you might discover that “Hey, my staff can actually handle more.”
When I used the Ohno Square method a while back, we were one big shop team, and we were thinking about breaking our staff into multiple shop teams. I had to become more aware of what the day-to-day workload had become for my employees. And I learned it helps to just sit back and watch them, and to, eventually point out elements of our workflow that have become complacent.
One shocking thing for me at that time was my staff’s tool placement—how often, and how far employees would have to walk to track down tools, and then walk to put them back. I said to my staff, “Okay, if you have to walk all the way over here and grab this welder every time, I’m going to move it into your stall.” And, of course, I got feedback from my staff, too.
Another issue for us at that time was materials; that whole process had become inefficient. So, what we did was use material carts; each team now has material carts so that, when they’re working in a certain area, the cart rolls to that area, right where they need it to be.
If you want to avoid letting complacency set in on your shop floor, using the Ohno Square is a rather easy solution.
About the Author
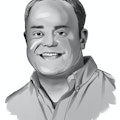