When Hurricane Dorian clipped the Raleigh, N.C., area a few months back, it elicited a flood of memories for Tana Malerba.
Mother Nature hasn’t always been kind to Malerba’s community.
The biggest example of that came back on April 16, 2011, when nine tornadoes occurred in Greater Raleigh, some producing winds of around 110 mph. Unfortunately for Malerba and her husband, Jim, their body shop was directly in the line of destruction. Coats Auto Body, located near downtown Raleigh, was left without a roof.
“It was absolutely surreal; everything was just torn apart,” Malerba says, recalling a story she first shared with FenderBender in 2017 (fenderbender.com/forceofnature).
“We had to level everything and start over from square one. … You’re in fight-or-flight mode at that time.”
The Malerbas completely rebuilt their Raleigh facility. And, while the experience tested their collective will, they used the aftermath of the storm as an opportunity to reconfigure their shop floor in a far more efficient manner.
Below, Tana Malerba shares the biggest lessons she has learned in recent years about how to ideally configure a shop floor.
Eliminate wasted movement.
In the wake of that devastating, spring day in 2011, Coats Auto Body’s Raleigh facility was condemned. Fortunately, the shop’s owners—who had already planned to shore up shop floor inefficiencies before the tornados struck—consulted with industry peers, and consultants at Sherwin-Williams, for insight on how to build their shop better than before, on the same footprint.
“Sometimes it’s best to have somebody who has no idea of how you run your daily business say, ‘This is what you could change to make things more efficient,’” Tana Malerba notes. “Sometimes, somebody that has an objective view can help.”
After considering several suggestions, the Malerbas’ general focus became eliminating wasteful movements for their shop workers.
Nowadays, the shop’s office, for example, is positioned closer to the shop floor. And, estimators are positioned at the front of the office, as close to technicians as possible, aiding quick communication between the employees. Reconfiguring the shop office also created room for an Enterprise rental car company office.
“It’s a much more comfortable environment that it was,” Malerba says of the shop setup. “It’s more efficient.”
Position the paint area strategically.
Prior to 2011, the Raleigh shop’s paint booth was positioned in the middle of the shop. And, that fact created quite the roadblock during busy times.
“Before,” Malerba notes, “you had to play ‘musical cars’ when you wanted to get a car in and out of the booth, if the techs had a lot of jobs. It was very difficult to maneuver everything.”
These days, cars rarely need to be backed out of the shop area in an effort to create room for employees to work.
“We reconfigured the shop, and the way we designed it, we put all the work bays on one side,” Malerba explains. “We designed the paint shop so … you come in one door and we have a prep area; if need be, we can do smaller jobs in that prep station. You pull vehicles into the booth, and then there’s another bay door on the end. We just pull it right out and into the tech’s bay.
“We made the most out of what we had.”
Create flow throughout the facility.
More than anything, the shop operators focused on easing congestion on their shop floor. For example, the shop floor now has an indoor area dedicated to cleaning up vehicles following repair work. In the past, that clean-up process took place outside. In 2019, the facility also features twice as many bay doors (10) than in its original configuration and, as a result, “the flow of bringing vehicles in and out of the shop is more efficient,” Malerba says.
Coats Auto Body was a high-volume setup even before its rebuild. Now, the nearly 12,000-square-foot facility is as productive as ever. Cycle time has been reduced from six days to four days in recent years. The Raleigh shop boasts an average monthly car count of 200 and combines with its newer, Garner, N.C., sister location to produce an annual revenue of $6.7 million—an increase of $1.5 million from just a couple years earlier.
While it doesn’t hurt that the Raleigh area is experiencing a population boom, their shop rebuild has clearly had the desired effect for the Malerbas.
“Now that we look back, everything worked out,” Tana Malerba says. “That, in itself, is a blessing.
“The shop is set up efficiently. Can we use more room? Yeah, we can—because we’re bursting at the seams. I look at the shop’s numbers this year and it’s amazing.”
About the Author
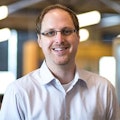