At Diehl Collision Centers, dry erase boards serve as a scoreboard.
At all three of the western Pennsylvania body shops, the big, white boards sit in production offices, and note the efficiency of each technician in the company.
“I did that as a motivator, as a friendly competition,” explains Matt Whittenberger, Diehl’s collision center director. “Any time a technician walks into that production office, they see where their hours are. They see where they’re at, and where everyone else is in the organization.”
Whittenberger’s strategy has worked wonders; the average technician efficiency at Diehl’s three locations is currently 150 percent.
“It’s pretty cool,” he says, “because now I have [technicians] coming to me, telling me where they’re gonna be at for the pay period. It’s cool to see them being proactive and coming to me.
“I didn’t have that before.”
Indeed. Five years ago, when Whittenberger came back to work for Diehl after six years spent as the GM of an independent shop, he took the helm of a rudderless ship.
Whittenberger attacked the challenge the only way he knew how:
“Just rolled up my sleeves and started working at it.”
The Issue
When Whittenberger returned to the fold at Diehl, back in 2013, he swallowed hard the second he saw the state of the business.
“I came back to a body shop that was just full of inefficiency, with no direction,” he says.
At that point, Diehl’s body shops had no blueprinting process to speak of. Because of that, incomplete estimates were often written, causing repair plans to unravel.
“We would get a vehicle into the shop with a horrible estimate,” Whittenberger explains, “and then we would take the car apart for blueprinting it and [need] a second order of parts. …”
And, lo and behold, once those parts came in, vehicles were disassembled further, which often revealed a third set of parts that required ordering.
“The blueprinting process is where I find 80 percent of efficiency faults,” he says.
“It was horrible [in 2013]. There was no blueprinting process, at all. So, it was a big challenge.”
The Answer
In Whittenberger’s experience, a body shop can usually make a swift, and dramatic, improvement in efficiency with one slight tweak: focus on completely disassembling vehicles at the outset of the repair process.
“The easiest improvement for any technician is to work with them on the front end—to be more thorough about dismantling a vehicle through the blueprinting process,” he says.
“If a technician is rushing on the front end of a job, they’re going to pay for it. And so is the shop … on the back end, putting it back together.”
After some careful consideration in 2013, plus the consultation of his 20 Group, Whittenberger addressed the issues limiting Diehl’s efficiency. His plan of attack included the following steps:
Insist on blueprinting. Lately, the biggest process that has enhanced efficiency in Whittenberger’s body shops is blueprinting vehicles completely.
“If you don’t blueprint a car,” he explains, then “we order parts more than once, we paint parts more than once. Hours go down—everything goes down.”
Monitor processes via the management system. Whittenberger’s staff heavily utilize their CCC ONE management system to make repair plans, and then closely monitor the progress of repairs.
“If we make a repair plan in CCC and something isn’t going as planned,” he says, “it turns red and it’s a big red flag. It’s a visual … Anyone, including the secretaries, should be able to answer any question for a customer wanting an update on a vehicle, or an insurance company, because everything is [noted] in CCC, in the management end of it, and we can see what’s going on with all the cars.”
Give estimators autonomy. Whittenberger wanted to limit the amount of second and third parts orders his facilities were required to make. As such, he gave his estimators the authority to control each job from start to finish.
“I gave them the authority to refuse anything less than a full blueprint,” Whittenberger says. “So, if a technician pulled a car in for a blueprint and, say, a panel wasn’t fully dismantled, the estimator had the authority to enforce that that panel gets completely taken apart before they finish that estimate.”
Utilize parts carts. At the suggestion of one of his 20 Group mentors, he purchased nearly 100 bakers carts (at $100 each) on Amazon, which could easily be converted into parts carts.
“They work great,” Whittenberger says of the converted parts carts. “We modified them by putting hooks on them. Then, we purchased bins that we secured to each cart, and they have divider trays for nuts and bolts.
“It wasn’t efficient having parts here, parts there, and we were losing stuff and breaking stuff. So, these parts carts that go along with each job helped.”
The Outcome
Diehl’s path to improved technician efficiency wasn’t without a detour or two. For example, a fair amount of veteran technicians fought the changes that Whittenberger implemented, meaning the collision repair center parted ways with roughly 25 percent of the technicians on its payroll.
Yet, the 15 body technicians that remain have bought into the plan for efficiency that Whittenberger has preached.
The results: Diehl’s average technician efficiency currently sits at 150 percent—in fact, one technician is currently at 300 percent. And the average CSI score of Diehl’s three locations is 93.8.
What’s more, Diehl has improved its length of rental by two days since a year ago.
By any measure, Whittenberger is experiencing professional success. Yet, the way he see it, the scoreboard clock hasn’t hit triple zeroes, and work remains.
“I’m constantly trying to improve” efficiency, he says. “I’ll never stop trying to make it better.”
About the Author
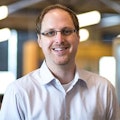