In recent columns, we’ve been focused on systems and processes that you will find valuable for your damage analysis or blueprinting process. Let’s continue with a few more tips, setups and procedures you can use to create your own robust damage analysis processes.
Having a dedicated teardown area in your shop will be crucial for a successful implementation of the blueprint process. This well-lit teardown area needs to be large enough to accommodate a vehicle with enough floor space around to accommodate parts removed off of the vehicle. The area will also need a two-post lift, a small rolling toolbox, a rolling work table, space for rolling parts carts and a small stand-up desk with the estimating computer and scan tool for the person doing the blueprinting. This isn’t the complete list of items you’ll need in this area, but I’d caution you to not clutter up the area with unnecessary stuff. Let me elaborate on some of the items listed above.
A two-post lift is ideal for your teardown area because it gives you full access to the underside of any vehicle you are blueprinting. This means you are able to remove under-shields, inspect and measure for structural damage, remove damaged exhaust components, inspect suspension components, etc., without interference and without laying on your back with a creeper. Your technicians that do the teardown will be more productive and will thank you for watching out for their health and welfare.
Even if your techs provide their own tools, you should consider setting up a company-owned toolbox stocked with the tools that are commonly needed for teardown. The toolbox itself should be an inexpensive 30-inch, five-drawer mechanics box, which you can buy for $250. When we were deciding what tools to put in the box, we had one of our techs do teardowns for one week. Each time the tech used one of his own tools for doing a teardown, we asked him to put that tool in our company-owned toolbox instead of putting it back into his toolbox.
At the end of the week, we had an inventory of tools that were used for teardowns and we were then able to go out and purchase those tools to stock our toolbox. In our inventory we have fewer than 25 items including the toolbox. The tools are arranged in the drawers with shadow-board type liners. We did cut-outs in the liners in the shapes of the tools so that it’s easy to see where the tools should be returned.
We also photographed each stocked drawer and assembled a laminated montage of the pictures as a guide to where the tools belonged. We attached the laminated photos to the underside of the tool box lid for quick reference. I know of some shops that do something similar but they use a peg board on a wall to display and hold the tools instead of keeping them in a tool box. Either way, it’s easy to maintain a small set of tools for teardown and it’s highly visible if something goes missing or needs replacement due to normal wear and tear.
A rolling work table that is 48 inches by 30 inches is extremely helpful in your teardown area. Put a shipping blanket on the table top and use it for disassembling bumper assemblies and other large assemblies. The shipping blanket will protect from scratched paint on the components you’re working on. The size of the table lets your tech sort fasteners, nuts, bolts, and other small parts and get them labeled for your parts storage system (more on that in future columns). I recommend the space under the table top not have a second shelf since this is likely to become an area that collects unnecessary “stuff” in your teardown area.
The blueprinters workstation will be your next project. As you can surmise, I believe the blueprinter should be stationed in the shop right in the teardown area. You might be tempted to use a process where the blueprinter typically stays in the office while the teardown is going on, then, when notified, will go to the car and take notes about the damaged parts, repairable panels, and other operations, and take a few photos of these areas. After doing that, the blueprinter goes back to the office and attempts to write a thorough repair plan.
There are several problems with that system and there will be a lot of wasted time and inaccuracies if you stick with it. How many times will your writer stop in the middle of the estimate to go back to the car and verify options that can’t be determined from the photos that were taken? Trust me, it happens all the time. More often than not, the writer will get interrupted by someone in the shop with questions about another vehicle or situation. These are just a couple of examples of why it makes sense to move your blueprinter, the estimating system and all relevant tools out to the teardown area.
The blueprinters’ workstation should include a good computer with a solid internet connection for using the cloud based estimating systems. You should install a widescreen 32-inch monitor or use dual monitors so that the blueprinter has plenty of visual real estate for the programs that will be running simultaneously such as the estimating system, the EPC, the OEM repair instructions, and parts search systems, among others. Make sure to include a good LED inspection light, a nice digital camera, a set of posca markers for mapping the repair plan on the vehicle, and a reasonably priced mobile phone or tablet to use for virtual assist interactions and other inspections.
I believe that the blueprinting process is one of the most important systems you should implement and in my next column I’ll outline some of the step-by-step procedures used by successful shops to get a thorough, accurate and virtually supplement-free repair plan.
About the Author
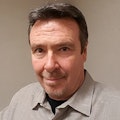
Steve Morris
The late Steve Morris was the regional director for Classic Collision in California (formerly Pride Collision Centers). He was an Accredited Automotive Manager (AAM) and ASE-certified master technician. Morris died April 22, 2022, at the age of 63 of complications following surgery.