The other day, I was sitting in my office, and I could count 1, 2, 3, 4, 5, 6 major sheetrock cracks. We had some in our front office that opened up two inches. It’s just crazy to look at. Mostly, we had foundation damage at our main shop.
Yes, our recovery continued in the weeks following Anchorage, Alaska’s 7.0 earthquake on Nov. 30.
Looking back, our initial plan of attack on Nov. 30 was to make sure that everyone at all three of our locations was OK, first and foremost. Luckily, no roofs caved in; if the roof had come down, we would’ve been in a world of hurt.
Right after the earthquake, my general manager type, our maintenance guy and I went around to each facility and did a good inspection, looking at what was damaged and what needed attention, and trying to figure out what was unsafe.
Two of our buildings had pretty big issues. So, we met again the next morning, to come up with a game plan of what we were going to do with the two damaged buildings and to try and decide if we could work in them or not.
I was able to get a team of engineers to those two buildings, and that group of engineers condemned both buildings. One of the buildings wasn’t one of our production facilities, so it wasn’t a big deal. But the other one was our main location, which is 15,000 square feet and usually has 40 employees there.
When they said, “This building is condemned; you need to shut down business,” I asked them if it could eventually be fixed. They said they didn’t know, and that I might have to tear the whole building down.
Yikes.
We had almost 100 cars on site, and it was right before Christmas. We’re fortunate that we have other facilities to move employees to, but I couldn’t move everyone.
The engineers left and my head’s spinning, like, “What the heck am I going to do?” I ended up getting more contractors to come in and give me more feedback. Seven days after the earthquake, another engineer comes in, and I told him, “Please realize that I’ll do any repairs and anything I need to do; but if you say we have to shut the building down, you’re talking about a major impact to 40 families.”
We have every kind of insurance that we could other than earthquake insurance; something like 1 percent of all Alaska residents have earthquake insurance, because, if you’re a business owner, you would spend $100,000 per year just for the premium.
Finally, I got in touch with one engineer that, as it randomly turned out, had been the engineer for the building in 1977. So, fortunately, he came up with a repair plan that let us keep our doors open. He wanted some cracks tended to right away, but then he also came up with a longterm plan … and he’s going to give it to us in order of priority, noting that some stuff needs to be done immediately, and some stuff needs to be done in the next 6 months. That’s how we handled the whole situation.
We luckily were able to keep the whole area open the entire time. But it was pretty touch and go for 7 days.
That earthquake ordeal woke us up to the way that the facilities are laid out, and what equipment is stored up high and what’s not, and to consider if things could fall and threaten someone’s life. When you start stacking stuff on toolboxes, and stacking stuff up on top of things, someone could eventually get hurt.
That process taught me to get much more detailed in my insurance coverage. Ten days after the earthquake, we sat down and did a full insurance review. We went through every policy and every option, just to make sure that we’re doing everything we can to have our policies in place as necessary.
What that earthquake experience taught me, more than anything, was that it’s very important to stay very attuned with your insurance policies; if you’re not set up right, that can be the end of your business. Shop owners need to consider: if some bad, unexpected disaster happens like a tornado, hurricane, or flood, do you want it to be the end of your business, or just a bump in the road?
About the Author
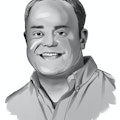