While OEM collision repair programs have taken off in speed in 2018, the GM Collision Repair Network Plan is a one-of-a-kind program that wants to include as many repair facilities as possible in the network.
The network launched at the beginning of August 2018, with the announcement that any collision repair facility in the U.S. could apply.
In just a few short months, 1,000 repair facilities including independent shops and dealership collision repair centers have joined the network, John Eck, manager of General Motors’ wholesale dealer channel, announced last week.
Compared to other OEMs like Nissan and Volvo, that also have collision repair programs in place, GM has been growing very fast. Nissan currently has around 1,500 repair facilities in its program and Volvo has the goal to reach approximately 350 shops in its network.
FenderBender reached out to GM to discuss what drove GM to form the program and John Eck shared some insight into the growing program.
Since the launch of the program, what repair standards have you rolled out?
We’ve been working to make sure we have the correct data and the right metrics for a repair scoreboard. We’re going to be measuring safe repair using OEM repair procedures. For example, Mitchell has successfully integrated mechanical and collision repair procedures into the estimate.
If a shop is using Mitchell’s estimating software, the staff will have access to General Motors and OEM repair procedures. The shop will no longer need to use a third-party system or spend time researching the repair procedure.
One example on time saving is how long it takes to properly document the repair process on a medium severity job. It takes about two hours. Now, this is written into the repair process.
What prompted the decision to create the program after so many years of not having it? Why was now the right time?
Today’s programs have to evolve to keep up with the rapid-fire pace of technological innovation in the auto industry, especially in areas like safety systems.
Our new program is designed to measure critical behaviors and procedures that will help ensure every collision repair is done to the highest standards, whether the work is done at a dealership, an independent body shop, or by a multi-shop operator.
GM has been working toward a program for quite some time. We’ve had the Cadillac aluminum repair network in market for a few years and have learned much through that program. It was through those lessons that we realized we needed a full repair network.
Why did you pick this type of repair plan model? Why did it seem like the right fit for General Motors?
We didn’t create GM’s collision repair network in a vacuum. This customer-focused program was developed with feedback from dealerships, independent repair facilities and customers, to drive safety for all.
We’re focusing on getting vehicles back into pre-crash condition and getting our drivers back on the roads. We’re doing this in a way that creates efficiencies for dealers and independent repair facilities. This network allows us to do that and help ensure shops have the right type of tools, equipment and training.
Do you think other OEMs will follow suit?
It is up to to each OEM to determine objectives of their program and how they execute.
I believe what we are seeing is the natural evolution and growth of these programs and other OEMs with programs are putting into place metrics that will help achieve their program objectives.
The one thing that is common across all these programs is the need for proper, safe repair.
As of now, how many dealers and independent shops are part of the network?
We do have some who have gone through the application process (roughly 1,000 repair facilities, according to the announcement at the 2018 SEMA Show) but that number is changing every day.
We’ll hold off on revealing this number until we go live with the store locator for the program this year.
About the Author
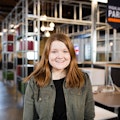