Danny Szarka refuses to lament his industry’s issue of a growing lack of technicians.
He’d rather search for solutions.
“Some people say, ‘Oh, we have a technician shortage; feel sorry for us.’ Well, no—you have to change your mindset,” says Szarka, the owner of Dynamic Collision Services, in Baltimore. “No longer can you put a [job ad out] and have 15 people in front of you, and you get to just pick someone that’s going to make you money—those days are over.”
According to multiple national organizations, the industry needs to hire about 120,000 new technicians per year through 2028 to meet demand. And, in order to accomplish that daunting task, Szarka feels shops need to alter the way they pay entry-level technicians.
Quite simply, they need to start compensating technicians better, he contends.
“So many businesses want to grow their business, but they don’t want to shrink their profit margin,” notes Szarka, a 15-year veteran of the industry. “Look at the big tech companies; you look at Amazon, you look at these [companies] that are paying $15–$18 per hour to start, and they understand that they can’t move product without people.”
So, as a shop operator, Szarka concludes, you have to ask yourself how much money you might be losing by not having a technician in a stall for an extended period.
At Dynamic Collision Services, all of the technicians are largely paid differently, Szarka says, mainly because no two technicians work at the exact same pace. At his shop, entry-level technicians are paid hourly, in addition to production incentives.
But these days, Szarka adds, body shop operators need to make the role of a technician enticing even beyond applying larger numbers to paychecks.
Because, to put it bluntly, what much of the industry has tried simply hasn’t captivated young people—many of whom would be suitable collision-repair technicians.
THE COLD, HARD REALITY
It’s a staggering statistic, yet one that’s verified by multiple collision-repair organizations:
The industry needs 1.2 million technicians over the next 10 years.
“It’s obviously a very big issue,” admits Brandon Eckenrode, the director of development for the Collision Repair Education Foundation. “We know it’s a problem now, and it’s only going to get worse if we can’t help address that issue.”
For various reasons, the collision-repair industry isn’t overly appealing to Generation Z.
“What’s different with this generation,” says Eckenrode, is that a lot of them have the mindset ‘You know, when I get out of college, I believe I’m going to make $100,000, and it won’t be long after that that I’ll be running a shop.’”
“What happens in a lot of instances is, a [collision repair] student graduates, they go to a shop, they can’t do some of the basic [repair tasks]. They’re pushed into a corner with a broom to clean up, they get frustrated, they end up quitting, and they don’t come back to the industry.”
Making matters worse is that, these days, entry-level pay in the collision-repair industry pales in comparison to other trades. Few are more aware of that fact than Greg Settle, the director of national initiatives with TechForce Foundation, an organization that has thoroughly researched the industry’s technician shortage in an effort to solve it.
“I took 15 skilled trades, and I looked at plumbers, welders, electricians, HVAC, and even wind-turbine technicians,” Settles says. “If you look at auto and collision entry-level positions versus some of the other skilled trades, it’s horrendous—they’re down at the bottom of the scale as far as pay.”
The numbers might surprise many shop operators. According to Bureau of Labor Statistics figures from 2017, among 15 of the most popular current trades, automotive body technician ranked 11th. According to the BLS, the lowest 10 percent of earners among “automotive body and related repairers” throughout the industry are making an average of $12.24 per hour.
That per-hour figure is less than the minimum wage in Washington, D.C.
What’s more, according to the 2018 FenderBender Industry Survey, 43.2 percent of collision-repair respondents paid their employees disability insurance, 55.8 percent offered employees a retirement plan, and 69 percent made health insurance available to their staff.
In Settles’ view, shop operators need to consider compensating employees—especially entry-level technicians—better. Consider: according to ASE’s 2018 Training Managers Council ATMC Benchmark Survey, roughly 33% of responding collision techs made $40,000-$60,000 per year; only slightly more than 25 percent of respondents made more than $80,000 annually (and many of the respondents were presumably past the entry-level stage).
“For the most part, if you talk about young men and women, they’re going to be focused mainly on starting pay,” Settles says. “Not many of them are going to be looking long term, like ‘Where am I going to be in 20 or 30 years with this career?’”
Another factor to bear in mind: the auto industry has had fewer and fewer potential hires to
choose from in recent years. After all, the average family simply isn’t producing as many children as in previous generations (according to statista.com, the average U.S. household decreased from 3.33 to 2.54 between 1960 and 2017). And, an immense amount of youth are attending college in this generation; according to the National Center for Education Statistics, the number of students attending American colleges and universities in 2018 reached 19.9 million―up from 15.3 million in 2000 (and nearly 67 percent of that group attended 4-year colleges).
“The issue we have,” Settle explains, “is every parent wants their kid to go to college. So, we have not been sending kids through trade schools” in recent years.
In effect, body shop owners are fishing in a rapidly shrinking pond, and their bait isn’t all that appealing to today’s youth.
THE YOUNGER PERSPECTIVE
Roughly six years ago, Michael Lamm got his foot in the door in the auto industry.
Thanks to a letter of recommendation from one of his instructors at Dunwoody College of Technology, Lamm landed a job as light-duty technician at nearby Porsche Minneapolis. He quickly learned just how in demand young techs are in the auto industry.
“I was working afternoons, after school,” recalls Lamm, now 32. “And they actually asked me, before I graduated, if I would just quit going to school and just drop out and work full-time, because they needed the help because they were so short” on staffing.
Lamm can understand why so few members of his generation are flocking toward careers as collision-repair technicians.
“When you go to a 2-year, private tech school, a lot of students come out with $30,000 in loans,” the young technician notes. “And you jump into the bottom of a dealership or collision center, and you’re making less than $20 per hour to start? It just doesn’t make sense to some people.”
Andy Roiniotis, a 25-year-old body tech in Wisconsin, has similar sentiments regarding the industry’s entry-level pay.
“There’s definitely a pay issue starting out,” notes Roiniotis, who says he didn’t earn flat-rate pay in the industry until he significantly exceeded employers’ expectations in terms of his production.
“I had to pay for school, and tools, and I had to pay off my student loans,”Roiniotis recalls. And “starting out, some shops don’t really want to pay what you’re worth, until you can push out what some of these experienced [technicians] can.”
Add in the daunting challenge of mastering evolving vehicle technology, and the physical strain that collision repair can put on a person’s body, and the body shop world just isn’t all that attractive to many young people, by the sound of it.
Tane’a Winters, a high school senior working a paid internship at Tom and Ed’s Autobody in Merrillville, Ind., says her generation largely favors a sedentary lifestyle, and thus, careers in collision repair aren’t on many teenagers’ radar these days.
“In my generation,” Winters says, “most people might feel like [collision repair] is hard, or too much work. My generation, they don’t want to … take the the time to make sure they do [work] right.”
Most young people, in the opinion of Roiniotis, “don’t want to work with their hands. They want to get an office job. It’s turning from what it used to be, but people still look at [collision repair work] as a dirty job.”
Says Lamm: “It’s a labor-intensive job, and, with the pay as low as it is, it’s difficult to keep doing this that long.”
Many young adults lack the finances or patience to work their way up the company ladder, spending months making entry-level, hourly wages.
“It takes a long time to become one of those A-techs,” says Roiniotis, a body tech at Pulera Collision Center in Kenosha, Wis. “They tell me all the time ‘Just wait, you’re going to make a lot of money here.’ But you look at your bills from school and your tools, and it’s tough.”
Make no mistake: Lamm, Roiniotis, and Winter appreciate their current jobs, and insist
they’re passionate about the industry they work in. But making ends meet when you’re an entry-level technician isn’t easy.
“You need to work up the ladder pretty quickly to be able to continue doing this that long,” Lamm says. “It is intimidating―a sink-or-swim type of thing.”
POSSIBLE SOLUTIONS
As dire as the technician shortage might currently seem, there are steps that shop owners can take to guard against feeling its effects.
Potential solutions include:
When Hiring, Don’t Obsess Over Experience.
In the last year, Szarka has hired five employees who had next to nothing in terms of auto industry experience. Those new hires did, however, have enthusiasm for cars, and that youthful exuberance has translated into employees who appreciate the opportunity given to them at Dynamic Collision Services. … And employees who have few complaints about their pay.
“We’re willing to [make such hires] because no one’s really giving these kids experience anymore, unless you’re stealing them from another shop,” Szarka explains.
When Szarka needs to hire a young technician, he doesn’t sit on the sidelines, waiting for job prospects to come to his doorstep. Instead, he actively seeks out job candidates. He frequently checks job websites like Indeed, Monster and CareerBuilder.
“The last guy I hired actually had no job history,” Szarka says. “But I called him, because it only takes 10 seconds for me to call him. I found out he was a number one student in an automotive program in high school.”
Offer Work/Life Balance.
In his research with TechForce Foundation, Settle has discovered that young adults value professional perks like getting involved with charitable endeavors in the workplace.
“Doing something that makes a difference is important to” today’s young adults, Settle says. “That’s the type of stuff that attracts these kids.”
Many members of the industry say today’s young workers tend to appreciate flexible scheduling, as well. At Lamm’s workplace in Minneapolis, for example, technicians are appreciative of the fact their employer only requires them to work one out of every eight Saturdays—in fact, Lamm says he considers that kind of scheduling “a bonus.”
“The person I hire, I want to figure out what makes them tick,” Szarka adds. “Sometimes it’s not money; sometimes it’s flexibility of hours. Maybe, if they have a family, they can come in at 10” each workday.
Provide Incentives.
As Eckenrode notes, entry-level employees often enter the industry and are taken aback by the amount of tools they need at their disposal. And, in his mind, employers should provide those tools to young technicians … with a contractual assurance from the employee that they’ll continue to work at that shop for a set period of time.
Eckenrode also feels that body shop operators should consider offering tuition reimbursement to employees who are taking college courses.
“Those kinds of things showcase how they’re going to save money,” Eckenrode notes of employee incentives. That’s “what I think this generation of students would get excited about.”
Lamm largely agrees. The young technician feels shop operators need to re-examine the overall compensation they provide entry-level technicians, thus allowing the young employees to make ends meet. Because, the Minnesotan noted, he has grown weary of hearing young industry peers speak of their overall financial struggles while earning perhaps $25 per hour in flat-rate pay.
Plot Out Career Paths.
Settle feels its imperative, in 2019, to help potential job prospects envision the potential career they could have in collision repair. All too often, the national foundation executive has observed young technicians get frustrated by their lack of career advancement after two or three years.
Settle suggests that shop operators should clearly explain how long an entry-level technician can expect to be given certain types of repair jobs before being given the opportunity for a promotion.
“You know, give them something where they can [envision] themselves in that path, instead of just [saying] ‘We’ll hire you and see how it goes.’ Well, that’s not going to cut it nowadays,” Settle says.
About the Author
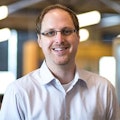