For 30 years, Robert Wisniewski has worked at Casey’s Auto Body, alongside the owner, Adam Gorsuch, and has dabbled in every position in the small shop. He began his career working as a floor sweeper. And he’s been there ever since.
What was the appeal of staying at one shop?
Part of the incentive to stay at Casey’s Auto Body came from the fact that it was a small shop and he wouldn’t be lost in the crowd. He says in order for a technician to make it through the evolving industry, the technician needs an “it” factor, like his own attention to detail, or even an engineering skill.
Ever since he started in the industry at the age of 16, Wisniewski has dabbled in almost every position and currently remains the head technician and the assistant manager at the shop. He spends 40 hours per week at minimum in the shop and helps work on roughly 50 cars per week, he says.
While the shop’s team numbers changed throughout the years, Wisniewski, a 2011 FenderBender Award nominee, says the factor that kept him successful and now working at a shop that is producing close to $1 million per year, has been following a motto of, “treat every car like it is your own.”
Always Progress
Wisniewski’s story is one of working his way up through the ranks. He started as the shop’s floor sweeper, worked his way to painter and eventually took over repairing the vehicles. When he was in high school, he attended a local vocational school for auto body and then came into the shop after school to paint the cars.
He says it was hard to get into the industry.
“I started going through the phone books and calling shops,” Wisniewski says.
Everybody that he called asked if he had his own tools and experience. Without tools, no one wanted to offer Wisniewski a position, he says.
Today, his experience at Casey’s Auto Body has taught him how to work in basically every position in the shop. He conducts repairs after the disassembly process, multitasks and takes over assistant manager duties when needed. He meets with his technician team and the manager each morning for roughly 15 minutes to go over the daily production schedule.
Gorsuch says while the shop has one painter, one bumper technician and one technician, Wisniewski takes on all the other shop responsibilities.
“He’s managing three individuals in the shop plus taking on his own workload,” Gorsuch says.
If the manager needs to step away from the front office to paint a vehicle, Wisniewski will take over the customer service tasks like answering the phone and greeting new people.
Today, the shop is receives more cars than it can handle and will most likely need to expand in the future, he says.
The “It” Factor
Wisniewski says that his success throughout the years is from maintaining an attention to detail and then applying that to the car.
Gorsuch says Wisniewski’s patience, methodology and attention to detail can also be seen when he made his own kitchen cabinets.
“I have a hawk eye and can pick out things fast when there is a problem,” he says.
In his free time, Wisniewski practices woodcrafting. For example, he made a dresser for his 12-year-old son and created it to look like a toolbox.
Teachable Moments
For 25 years, only Wisniewski and Gorsuch worked at the shop, with Wisniewski repairing vehicles and Gorsuch painting them.
Not only does Wisniewski practice his own skills, he also takes time to mentor other students.
“When a kid comes into the shop from school, it’s a different work speed and different environment,” he says.
Wisniewski will work with the students to work in the fast-paced environment and keep track of their responsibilities.
Gorsuch says Wisniewski will do the harder repair on the vehicle and then hand it off to other people.
“At some points, he will do absolutely anything to get the car out and get paid for the job,” he says.
About the Author
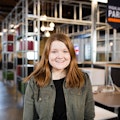