What it Takes to Become an Award-Winning Body Shop
Jay Cassel feels many years removed from his time working on a shop floor—though, in reality, only about a decade has passed. The reason the body shop manager feels that way is that the technology involved is now light years ahead of where it was.
“It’s a very complicated process working on a vehicle that’s been in a collision anymore,” said Cassel, the collision center manager at Bennett Toyota, in Allentown, Pa. “It’s not the good ol’ days of strapping the car to a backhoe [out] back and pulling the frame out; you can’t do that. The tolerances on these vehicles anymore are millimeters, not inches. … There’s not a lot of room for error.”
Despite such challenges, Cassel has helped his shop find its way. So much so, in fact, that Bennett Toyota recently became one of three Toyota Certified Collision Centers to be presented with a 2017 Shop of the year award. Recipients were chosen based on areas such as strong financials, consistent improvement in KPIs, and exceptional customer satisfaction scores.
While Bennett Toyota boasts a stellar, 97.02 CSI score, Cassel said the main reason his shop has been deemed award-worthy is the fact each body shop employee is exhaustively trained.
“We strive to make sure that all my technicians and my staff are all up-to-date with current training, through Toyota and I-CAR and other resources, as well--we do a lot of training through our paint supplier, and through I-CAR for my estimators,” Cassel noted. “I, myself, have taken advantage of a lot of training that Toyota has to offer.”
Cassel, a veteran of 27 years in the auto industry, has no qualms about spending money to send employees to training—even if it involves expenses like airline tickets—because he knows that having highly-qualified employees is invaluable.
“Especially with the way the industry’s going,” Cassel said. “These cars are not getting any easier to work on. … With the advancement of computers, and sensors and safety systems on these vehicles, they’re very manufacturer-specific now. So it’s real important to make sure you’ve got a highly trained staff to work on these cars, and especially to work on them correctly.”
While the challenges of being a body shop manager might feel like they’re mounting in 2018—with more on the horizon, like training for aluminum repairs—Cassel is confident that time-tested philosophies can help any collision-repair center thrive.
“The big thing is communication with your customers,” the industry veteran said. “For some reason, communication between the body shops and the customers has sometimes gone by the wayside.
“We strive heavily [to] sure that we communicate with our customers what, exactly, is being done to their vehicles.”
About the Author
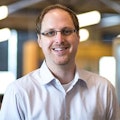