If there is one thing that Carl Garcia is passionate about, it’s education. He’s the chairman of his local workforce investment board, which provides job training in his area. He’s brought in training to his shop from places as far away as Italy, all with the goal of providing the best education he can to his employees.
“I think anytime you can bring training to the shop or different cultures to the shop, [it] brings people together and closer,” he says.
With a drive for constant education, it’s no surprise that the owner of Carl’s Collision Center in Fall River, Mass., has had a designated space in his shop for education for years, and now that space will turn into an off-site training center.
He recently purchased a center that will completely be dedicated to staff education. Garcia will be able to transfer what he’s implemented in his shop to a much more comfortable space for his staff.
And, according to Jeff Peevy, president of the Automotive Management Institute (AMi), Garcia is the kind of shop owner you need to be. Both owners and employees need to take responsibility to keep educated and updated, he says.
It’s about the “sustainable competitive advantage,” as Peevy says. You can invest in all this equipment, which will give you a competitive advantage, but it’s not sustainable because it will go out of date. However, learning is sustainable.
Garcia and Peevy share the advantages of in-house training and when you do decide to designate a training space, what you should have in it to ensure that it’s used.
Designating the Space
From the moment he purchased a larger building back in 2005 when he officially became owner, Garcia had a vision of building a training center.
The space, which facilitated I-CAR classes and brought in outside training, was more efficient for Garcia as it prevented technicians from traveling back and forth for different classes.
As the business grew, the training space became smaller and smaller, he says. The only way to keep his vision alive was to purchase another building that used to be a training facility. There are five key components to the space:
1) The Space
Garcia says that having a dedicated training space has not only cut down on travel time for staff, but it also gives them an opportunity to actually absorb what they’re learning. Before, in the shop’s original training space, a technician could see when a customer came in and got distracted. Now, it’s a quiet area where he or she can put work on hold for a bit.
More importantly, it will give him an opportunity to take in people that aren’t from the industry and give them an opportunity to learn the trade.
He recently had three young apprentices start and the apprentices and their mentors will use the space to do additional training.
The center will also serve as a place for strategic planning, he says, where they can hold meetings.
2) The Technology
Since the space was previously a training center, Garcia uses that to his advantage as the hookups for computers and TVs are already set up.
There will be a computer room for several desktops for technicians to do online training. The shop is Tesla certified, which requires a lot of online training, he says. He is even thinking about doing an in-house IT training program because its important that his staff understands how the technology works.
3) The Tools
In addition to online training, Garcia wants to make sure his center is filled with parts and tools that his staff would benefit from learning what they are. “Little things,” he says, or tools they wouldn’t necessarily recognize, like PBS converters.
Garcia plans to build panels with fish eyes and pin holes, possibly paint defects, to have a physical example of things on which he could train his guys.
4) The Reading Resources
Just as the tools are necessary for training, so are the reading materials. Peevy says that the one thing that he sees frequently in more shops are trade magazine lying around. That type of reading materials can prove very useful for your shop.
The industry magazines are a big plus, Peevy says. Whether it’s an OEM magazine or any other type, it’s a good place to start as far as building reading material into training or just having reading material available for your staff.
In those magazines, identify certain articles or highlight takeaways so your staff can read exactly what you think is beneficial. Peevy says that now he or she can receive AMi credit for the articles they read, which will tackle formal class education and in-house education.
5) Visual Aids
Don’t be afraid to have charts and reference materials up on the walls, Peevy says. Make sure you have necessary office tools accessible, such as folders and three-hole punches for material.
Keeping everything clean and organized will help encourage staff members to come in.
The Implementation
One of the biggest mistakes that an owner can do is fail to recognize that their employees are more than labor. This is the “industrial-age mindset,” Peevy says.
Managers with this mindset will put employees down who take the time to sit down and read something, simply because they’re not doing physical labor. Instead, you need to be encouraging and set the expectation that learning is mandatory.
Don’t dictate how often the space is used, but implement strategies that require some discipline. For example, Peevy has seen some shops have a “checkout system,” similar to that of a library.
If there is an interesting article in a magazine or book, have the employee check it out and sign that he or she has read it. This will drive some consistency on what is read and what everyone's thinking and learning.
If this is the first time you’re designating a space for learning in your shop, Garcia recommends to start slow.
“Don’t try to get it all going overnight,” he says.
Really try developing it and have obtainable goals for yourself and your staff using the facility, he says.
Also, don’t be afraid to reach out to those around you. There is grant money available for certain types of training and check in with your local community college or tech college and see if it can provide you with some resources.
About the Author
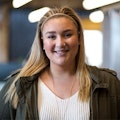